The roll bending process is a manufacturing technique used to bend metal sheets, plates, or other materials into curved or cylindrical shapes. This process involves passing the material through a set of rotating rolls, which apply pressure to gradually bend the material into the desired shape. It is widely used in industries such as construction, automotive, aerospace, and shipbuilding to create components like pipes, tanks, and structural beams. The process can be performed using various types of roll bending machines, including three-roll and four-roll configurations, each suited for specific applications and material types. The roll bending process is valued for its precision, efficiency, and ability to handle large or thick materials.
Key Points Explained:
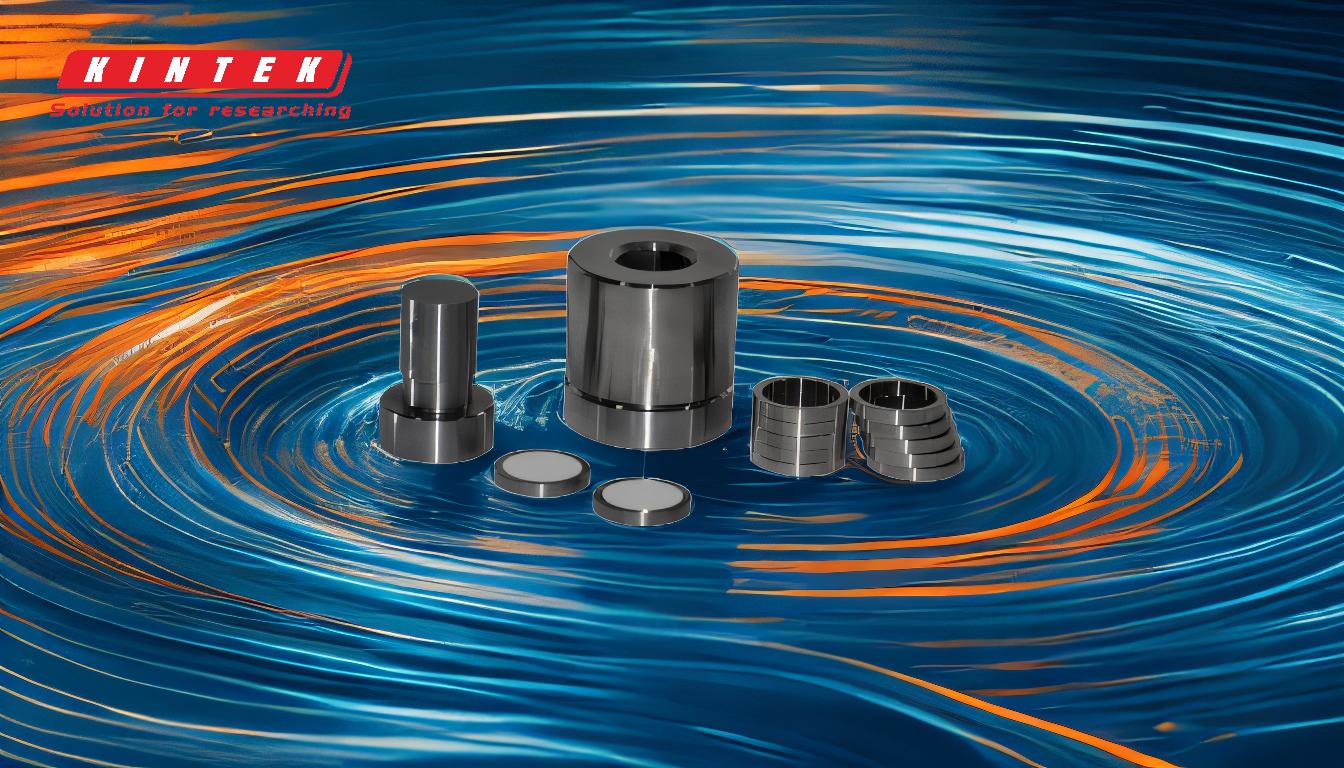
-
Definition and Purpose of Roll Bending:
- Roll bending is a metalworking process that transforms flat sheets or plates into curved or cylindrical shapes.
- It is commonly used to produce components such as pipes, tanks, cones, and structural arcs.
- The process is essential in industries requiring precise curvature, such as construction, automotive, and aerospace.
-
Types of Roll Bending Machines:
-
Three-Roll Bending Machines:
- These machines consist of three rolls: two fixed bottom rolls and one adjustable top roll.
- The material is fed between the rolls, and the top roll applies pressure to bend the material.
- Suitable for simpler curves and lighter materials.
-
Four-Roll Bending Machines:
- These machines include an additional roll, providing better control over the bending process.
- The extra roll allows for pre-bending the edges of the material, reducing the need for additional processing.
- Ideal for complex shapes and thicker materials.
-
Three-Roll Bending Machines:
-
Steps in the Roll Bending Process:
-
Material Preparation:
- The material is cut to the required size and shape before being fed into the machine.
-
Feeding the Material:
- The material is positioned between the rolls, ensuring proper alignment.
-
Applying Pressure:
- The rolls rotate, and pressure is applied to gradually bend the material.
- The operator adjusts the rolls to achieve the desired curvature.
-
Final Adjustments:
- The material may undergo additional passes through the rolls to refine the shape and ensure accuracy.
-
Material Preparation:
-
Advantages of Roll Bending:
-
Precision:
- The process allows for high levels of accuracy, ensuring consistent curvature across the material.
-
Versatility:
- Roll bending can handle a wide range of materials, including steel, aluminum, and stainless steel.
-
Efficiency:
- The process is faster and more cost-effective compared to manual bending methods.
-
Scalability:
- Suitable for both small-scale and large-scale production.
-
Precision:
-
Applications of Roll Bending:
-
Construction:
- Used to create structural components like beams, arches, and columns.
-
Automotive:
- Produces curved parts for vehicle frames, exhaust systems, and body panels.
-
Aerospace:
- Manufactures components for aircraft fuselages and wings.
-
Shipbuilding:
- Creates curved sections for hulls and superstructures.
-
Construction:
-
Factors to Consider in Roll Bending:
-
Material Thickness and Type:
- Thicker materials require more powerful machines and precise adjustments.
-
Radius of Curvature:
- The desired curvature determines the type of machine and process parameters.
-
Machine Configuration:
- Choosing the right machine (three-roll or four-roll) based on the complexity of the shape.
-
Operator Skill:
- Skilled operators are essential for achieving accurate and consistent results.
-
Material Thickness and Type:
-
Challenges and Solutions:
-
Springback:
- Materials may return slightly to their original shape after bending.
- Solution: Adjust the bending angle to compensate for springback.
-
Material Deformation:
- Improper settings can cause wrinkles or cracks.
- Solution: Use appropriate roll configurations and apply gradual pressure.
-
Machine Maintenance:
- Regular maintenance ensures consistent performance and extends machine life.
-
Springback:
By understanding the roll bending process, its types, steps, advantages, and applications, manufacturers can effectively utilize this technique to produce high-quality curved components for various industries.
Summary Table:
Aspect | Details |
---|---|
Definition | A metalworking process to bend flat sheets/plates into curved/cylindrical shapes. |
Types of Machines | - Three-Roll: Simpler curves, lighter materials. - Four-Roll: Complex shapes, thicker materials. |
Steps | 1. Material Preparation 2. Feeding 3. Applying Pressure 4. Final Adjustments |
Advantages | Precision, versatility, efficiency, scalability. |
Applications | Construction, automotive, aerospace, shipbuilding. |
Key Factors | Material thickness, curvature radius, machine type, operator skill. |
Challenges | Springback, material deformation, machine maintenance. |
Need expert guidance on roll bending for your project? Contact us today to get started!