The rule of thumb for sintering temperature is typically 30% to 50% of the material's melting temperature. This range ensures a reasonably fast sintering rate while minimizing excessive grain growth, which is crucial for maintaining the material's properties. Sintering temperature and time are influenced by factors such as material type, desired density, and the specific application. The process must balance temperature and time to achieve optimal porosity, density, strength, and hardness without causing defects like scorching or degraded properties. A controlled atmospheric environment and careful consideration of heating rates, pressure, particle size, and composition are also essential for successful sintering.
Key Points Explained:
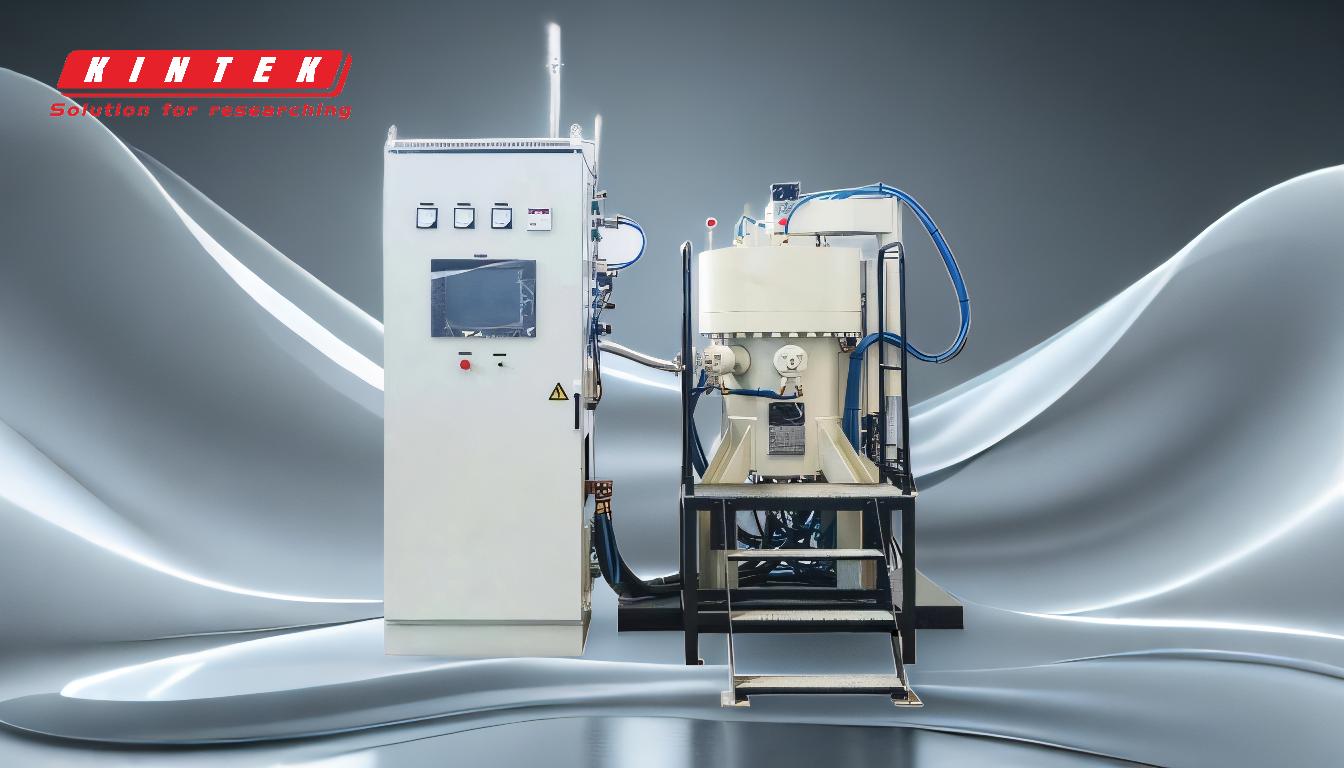
-
Rule of Thumb for Sintering Temperature:
- The general guideline for sintering temperature is 30% to 50% of the material's melting temperature. This range ensures efficient sintering without excessive grain growth, which is particularly important for crystalline materials.
-
Importance of Temperature in Sintering:
- Temperature is critical because it must be high enough to allow atomic diffusion across particle boundaries, facilitating particle fusion. However, it must remain below the material's melting point to prevent liquefaction and maintain structural integrity.
-
Factors Influencing Sintering:
- Material Type: Different materials have unique sintering requirements based on their melting points and thermal properties.
- Desired Density: The required density of the final part influences the sintering temperature and time.
- Application: Specific applications may demand tailored sintering conditions to achieve the desired material properties.
-
Impact of Sintering Temperature and Time:
- High Temperatures and Long Times: Can reduce product properties and lead to defects like scorching.
- Low Temperatures or Long Times: May result in degraded properties due to insufficient sintering.
-
Controlled Atmospheric Environment:
- Sintering furnaces operate in carefully controlled environments to ensure consistent and optimal sintering conditions. This control is vital for achieving the desired material properties and avoiding defects.
-
Heating Rate and Pressure:
- Heating Rate: Affects densification; a controlled rate is necessary to achieve uniform sintering.
- Pressure: Enhances particle rearrangement and helps eliminate porosity, contributing to a denser final product.
-
Particle Size and Composition:
- Particle Size: Smaller particles promote better densification due to increased surface area and enhanced atomic diffusion.
- Composition: Homogeneous compositions facilitate more uniform sintering and better material properties.
By adhering to these principles, one can optimize the sintering process to achieve high-quality, durable materials with the desired properties.
Summary Table:
Key Factor | Description |
---|---|
Sintering Temperature | 30%-50% of material's melting temperature to balance efficiency and grain growth. |
Material Type | Determines sintering requirements based on melting points and thermal properties. |
Desired Density | Influences sintering temperature and time for optimal porosity and strength. |
Application | Tailored conditions ensure desired material properties for specific uses. |
Heating Rate & Pressure | Controlled rates and pressure enhance densification and eliminate porosity. |
Particle Size & Composition | Smaller particles and homogeneous compositions improve sintering uniformity. |
Need help optimizing your sintering process? Contact our experts today for tailored solutions!