A muffle furnace is a critical piece of equipment in laboratories and industrial settings, primarily used for high-temperature applications such as ashing, heat treatment, and material testing. The settings of a muffle furnace, particularly its temperature range, are determined by the specific application, the materials being processed, and the furnace's design. High-temperature muffle furnaces typically operate between 1000°C and 2000°C, while laboratory models often range from 1100°C to 1200°C. Key factors influencing the furnace's performance include the type of material being heated, the fuel source (electricity or gas), environmental conditions, and safety features like temperature control and auto-cut-off sensors. Proper placement and ventilation also play a significant role in ensuring optimal heating efficiency and longevity of the furnace.
Key Points Explained:
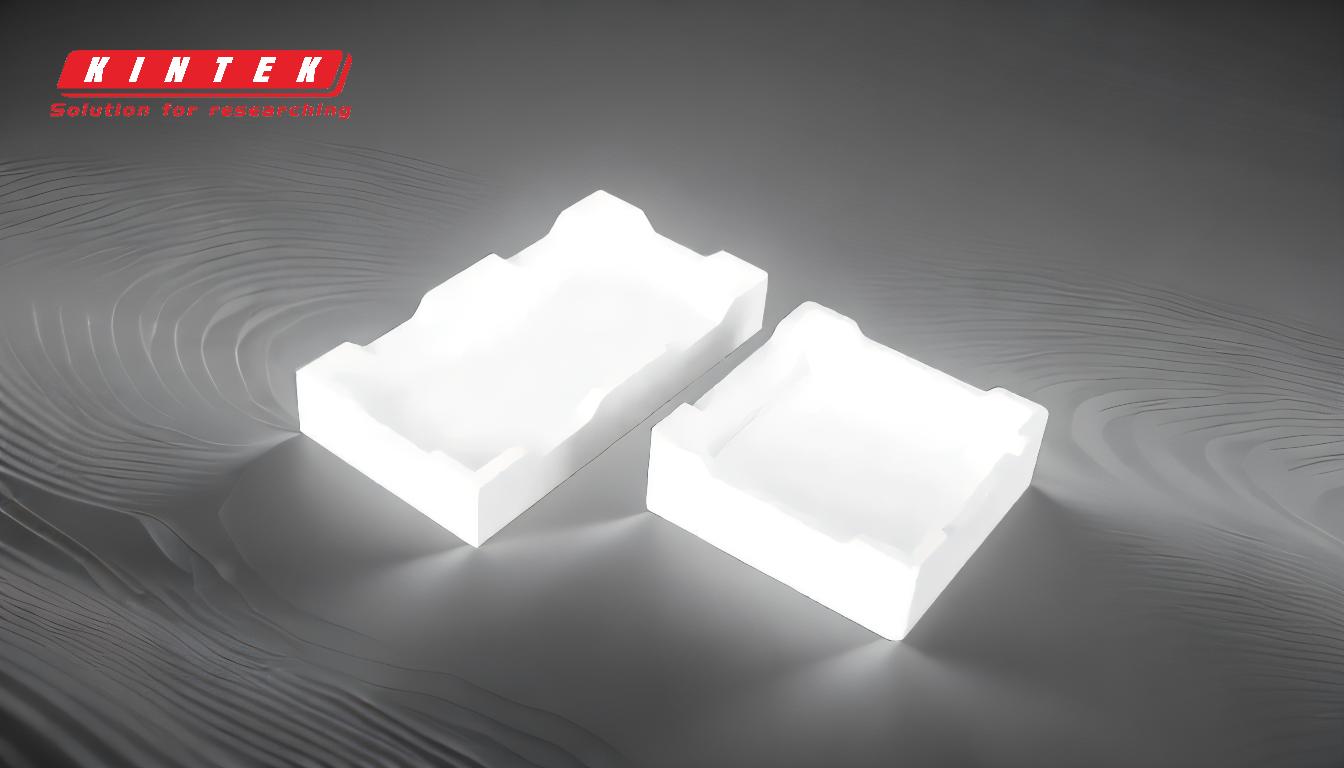
-
Temperature Range:
- The temperature setting of a muffle furnace depends on its intended use. High-temperature models typically operate between 1000°C and 2000°C, while laboratory furnaces are designed for 1100°C to 1200°C. Some specialized models can reach up to 1200°C, making them suitable for applications like ashing and heat treatment.
- The chosen temperature range should align with the specific requirements of the material or process being conducted. For example, ashing organic samples may require lower temperatures, while sintering ceramics or metals might necessitate higher temperatures.
-
Material Considerations:
- The type of material being heated significantly influences the furnace settings. Common materials include borosilicate, alumina, silicon carbide, and carbon steel. Each material has unique thermal properties, which dictate the optimal temperature range and heating duration.
- For instance, silicon carbide heating elements are ideal for high-temperature applications due to their durability and thermal conductivity, while alumina is preferred for its resistance to thermal shock.
-
Fuel Source and Energy Efficiency:
- Muffle furnaces can be powered by electricity or gas (e.g., propane or natural gas). Electric furnaces are more common in laboratory settings due to their ease of use and precise temperature control. Gas-powered units, on the other hand, are often used in industrial applications where higher temperatures are required.
- Energy efficiency is a key benefit of muffle furnaces, as they are designed to minimize heat loss and maximize thermal conductivity, reducing operational costs.
-
Environmental and Placement Factors:
- The surrounding environment, including ventilation and ambient temperature, can impact the furnace's performance. Proper placement ensures adequate airflow, preventing overheating and extending the lifespan of the heating elements.
- Elements inside the furnace are shielded from direct contact with vapors and gases, which enhances their durability compared to traditional electric furnaces.
-
Safety and Control Features:
- Modern muffle furnaces are equipped with advanced safety features, such as auto-cut-off sensors and temperature controllers, to prevent overheating and ensure consistent performance. These features are critical for maintaining the integrity of the samples and protecting the equipment.
- Software integration allows for precise temperature programming and monitoring, making it easier to achieve uniform heating and repeatable results.
-
Chamber Size and Design:
- The dimensions of the furnace chamber and door opening options are important considerations, especially when processing large or irregularly shaped samples. A well-designed chamber ensures even heat distribution and efficient sample handling.
- The heating element and power supply must be compatible with the intended use, ensuring reliable operation and consistent performance.
By carefully considering these factors, users can optimize the settings of their muffle furnace to meet specific application requirements, ensuring efficient and reliable operation.
Summary Table:
Key Factor | Details |
---|---|
Temperature Range | 1000°C–2000°C (high-temperature), 1100°C–1200°C (laboratory models) |
Material Considerations | Borosilicate, alumina, silicon carbide, carbon steel |
Fuel Source | Electricity (precise control) or gas (higher temperatures) |
Environmental Factors | Proper placement, ventilation, and ambient temperature |
Safety Features | Auto-cut-off sensors, temperature controllers, software integration |
Chamber Design | Dimensions, door options, and heating element compatibility |
Need help optimizing your muffle furnace settings? Contact our experts today for tailored solutions!