Compression molding is a highly significant manufacturing process, particularly in industries like automotive manufacturing, due to its ability to produce high-strength composite structures and complex parts with precision and efficiency. This process involves using heat and compression to shape raw materials such as metal, plastic compounds, or rubber into molds, resulting in parts with net size and shape, excellent surface finishes, and outstanding repeatability. Supported by hydraulic presses, compression molding is fast, cost-effective, and reduces material waste and labor costs. It is ideal for creating automotive interior components like sun visors and gear knobs, making it a cornerstone of modern manufacturing.
Key Points Explained:
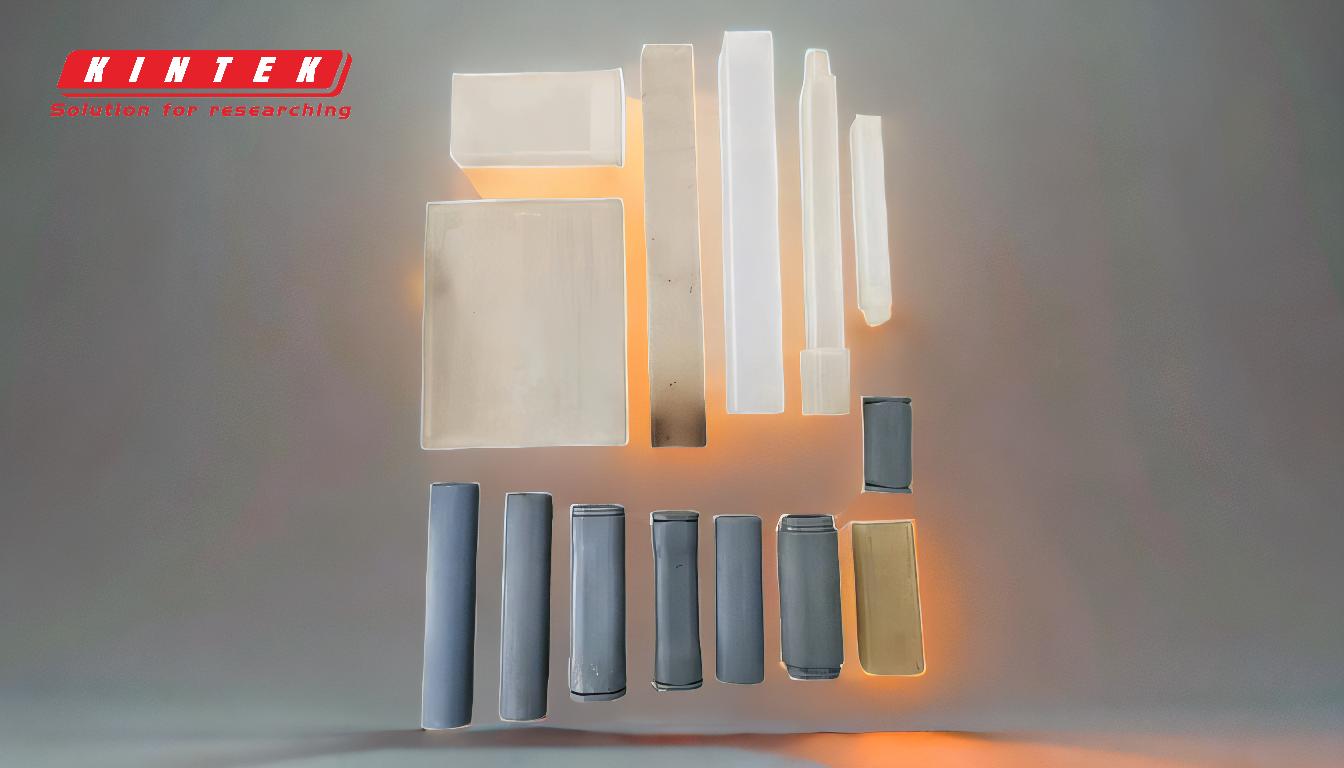
-
High-Strength Composite Structures and Complex Parts:
- Compression molding is renowned for producing parts with exceptional strength and durability. This is particularly important in industries where structural integrity is critical, such as automotive and aerospace.
- The process is capable of creating complex shapes and sizes, which are often required in modern manufacturing. This versatility allows for the production of intricate components that might be challenging to achieve with other methods.
-
Net Size and Shape with Excellent Surface Finishes:
- One of the standout features of compression molding is its ability to produce parts with net size and shape, meaning minimal post-processing is required. This reduces additional labor and costs.
- The process also results in two excellent finished surfaces, which is crucial for applications where aesthetics and surface quality are important, such as automotive interiors.
-
Outstanding Part-to-Part Repeatability:
- Compression molding ensures high consistency and repeatability across multiple parts. This is vital for mass production, where uniformity and reliability are essential.
- The consistent quality of parts reduces the likelihood of defects and ensures that each component meets the required specifications, enhancing overall product reliability.
-
Cost-Effectiveness and Efficiency:
- The use of hydraulic presses in compression molding makes the process fast and efficient. Hydraulic systems provide the necessary force and control to shape materials accurately and quickly.
- This efficiency translates to reduced material waste and lower labor costs, making compression molding a cost-effective solution for large-scale production.
-
Applications in Automotive Manufacturing:
- Compression molding is particularly significant in the automotive industry, where it is used to manufacture interior components such as sun visors, gear knobs, and trim covers.
- The ability to produce high-quality, durable parts with excellent surface finishes makes it ideal for automotive applications, where both functionality and aesthetics are important.
-
Material Versatility:
- The process can handle a variety of raw materials, including metal, plastic compounds, and rubber. This versatility allows manufacturers to choose the most suitable material for their specific application.
- For example, well-shaped un-branched rubber stock is commonly used in compression molding to create parts with precise dimensions and excellent mechanical properties.
-
Reduction of Material Waste:
- Excess material, known as mold flash, flows out of special grooves during the molding process. This feature helps in minimizing material waste, contributing to the overall cost-effectiveness of the process.
- Efficient use of materials not only reduces costs but also aligns with sustainability goals by minimizing environmental impact.
In summary, compression molding is a pivotal manufacturing process due to its ability to produce high-strength, complex parts with excellent surface finishes and outstanding repeatability. Its cost-effectiveness, efficiency, and material versatility make it indispensable in industries like automotive manufacturing, where precision, durability, and aesthetics are paramount.
Summary Table:
Key Benefits | Description |
---|---|
High-Strength Composite Structures | Produces durable, complex parts with exceptional strength and structural integrity. |
Net Size and Shape | Creates parts with minimal post-processing and excellent surface finishes. |
Outstanding Repeatability | Ensures consistent quality and uniformity across mass-produced parts. |
Cost-Effectiveness | Reduces material waste and labor costs through efficient hydraulic press systems. |
Automotive Applications | Ideal for manufacturing interior components like sun visors and gear knobs. |
Material Versatility | Works with metals, plastics, and rubber for diverse manufacturing needs. |
Sustainability | Minimizes material waste, aligning with environmental and cost-saving goals. |
Transform your manufacturing process with compression molding—contact us today to learn more!