The sintering process in powder metallurgy is a critical heat treatment step that transforms compacted metal powder into a solid, durable component. It involves heating the powder to a temperature just below its melting point, allowing the particles to bond and densify without fully melting. This process enhances the material's strength, hardness, and structural integrity. Sintering typically follows powder selection, mixing, and compaction, and it is influenced by factors such as temperature, heating rate, pressure, particle size, and composition. The process is widely used in manufacturing to produce complex metal parts with precise dimensions and properties.
Key Points Explained:
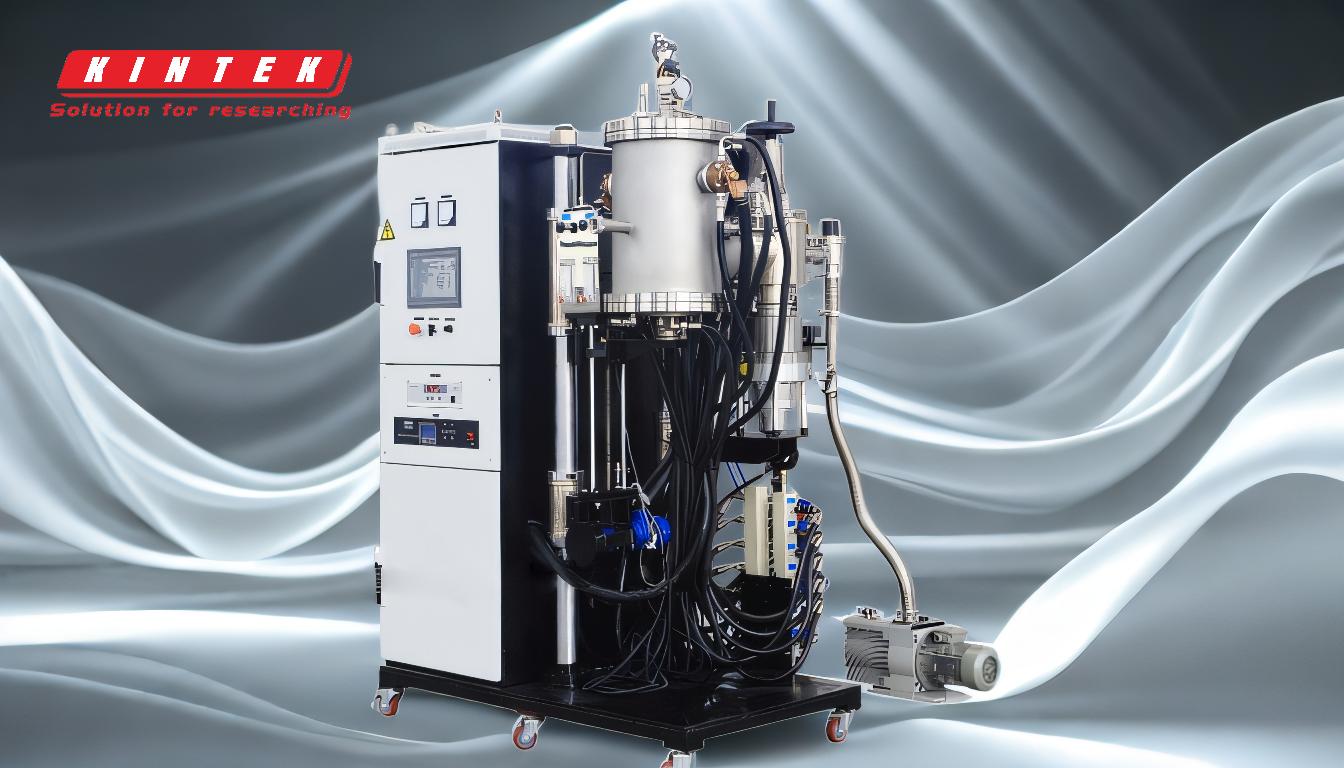
-
Definition and Purpose of Sintering:
- Sintering is a heat treatment process in powder metallurgy where compacted metal powder is heated to just below its melting point.
- The purpose is to bond the metal particles together, enhancing the part's strength, hardness, and density while maintaining its shape.
-
Steps in the Sintering Process:
- Powder Selection and Mixing: The process begins with selecting the appropriate metal powders (e.g., iron, nickel, molybdenum, or copper) and mixing them with lubricants or other additives to achieve the desired composition.
- Compaction: The mixed powder is pressed into a specific shape using a die press, creating a "green" part with initial strength.
- Sintering: The green part is heated in a controlled furnace environment to a temperature just below the melting point of the metal. This allows the particles to bond through diffusion, forming a solid piece.
- Post-Treatment: After sintering, additional treatments such as machining, heat treatment, or surface finishing may be applied to achieve the final properties and dimensions.
-
Factors Influencing Sintering:
- Temperature: Determines the sintering kinetics and the final material properties. Higher temperatures generally improve particle bonding but must be controlled to avoid melting.
- Heating Rate: Affects the densification process. A slower heating rate allows for more uniform particle bonding, while a faster rate may lead to uneven densification.
- Pressure: Applied during compaction and sometimes during sintering to enhance particle rearrangement and reduce porosity.
- Particle Size and Composition: Smaller particles and homogeneous compositions promote better densification and bonding due to increased surface area and uniform material properties.
-
Mechanism of Sintering:
- During sintering, metal particles bond at their contact points through diffusion, forming necks between particles. Over time, these necks grow, reducing porosity and increasing the part's density.
- The process can be likened to ice cubes in a glass of water, where the cubes fuse at their contact points before melting.
-
Applications of Sintering:
- Sintering is used to manufacture a wide range of metal parts, including gears, bearings, filters, and structural components.
- It is also employed in the production of ceramics, glass, and other materials where bonding of powdered particles is required.
-
Advantages of Sintering:
- Enables the production of complex shapes with precise dimensions and minimal material waste.
- Improves material properties such as strength, hardness, and wear resistance.
- Suitable for a wide range of metals and alloys, making it a versatile manufacturing process.
-
Challenges and Considerations:
- Controlling the sintering environment (e.g., temperature, atmosphere) is crucial to prevent oxidation or other undesirable reactions.
- Achieving uniform densification can be challenging, especially for parts with complex geometries or varying wall thicknesses.
By understanding these key points, equipment and consumable purchasers can make informed decisions about the sintering process, ensuring they select the right materials and parameters for their specific applications.
Summary Table:
Aspect | Details |
---|---|
Purpose | Bonds metal particles, enhancing strength, hardness, and density. |
Key Steps | Powder selection, mixing, compaction, sintering, and post-treatment. |
Influencing Factors | Temperature, heating rate, pressure, particle size, and composition. |
Applications | Gears, bearings, filters, structural components, ceramics, and glass. |
Advantages | Produces complex shapes, improves material properties, and reduces waste. |
Challenges | Requires precise control of temperature and atmosphere for optimal results. |
Ready to optimize your sintering process? Contact our experts today for tailored solutions!