The spot size of XRF (X-ray Fluorescence) typically ranges from 20 mm to 60 mm in conventional systems. This large spot size allows for the use of a wide angle of tube radiation for excitation, and the analyzed sample volume is averaged over the entire spot area. XRF is a non-destructive technique used for elemental and material analysis, offering fast and accurate results with minimal sample preparation. It is widely used in industries for verifying material composition and coating thickness, making it a versatile tool for quality control and research applications.
Key Points Explained:
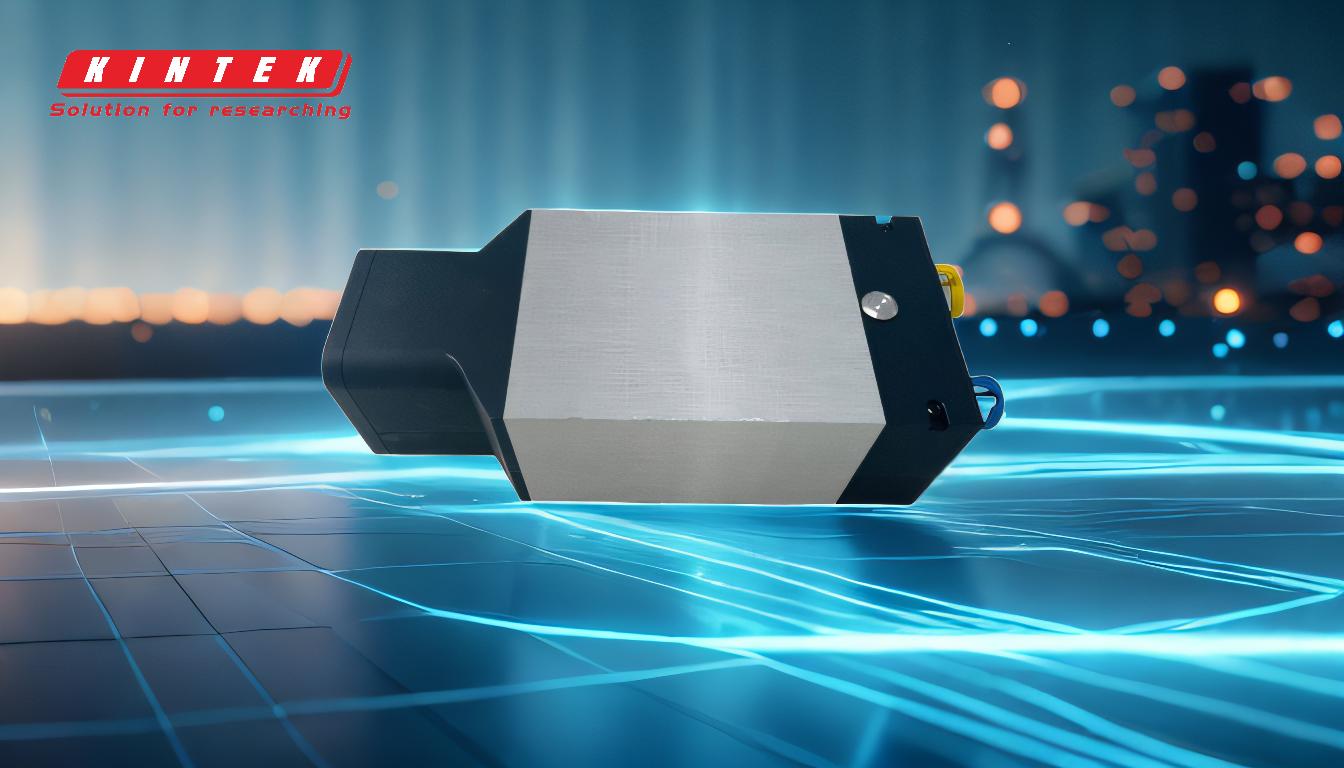
-
Spot Size of XRF:
- The spot size of conventional XRF systems typically ranges from 20 mm to 60 mm.
- This large spot size is advantageous because it allows for the use of a wide angle of tube radiation for excitation, ensuring a larger analyzed sample volume.
- The composition calculated by XRF is averaged over the entire analyzed volume, providing a representative analysis of the sample.
-
Non-Destructive Nature of XRF:
- XRF is a non-destructive technique, meaning the sample is not damaged during analysis.
- This feature is particularly beneficial for analyzing valuable or irreplaceable samples, as they can be reused after testing.
-
Fast and Accurate Analysis:
- XRF provides rapid results, with analysis times ranging from 10 seconds to a few minutes.
- The technique is highly accurate, with a detection limit of 0.0005 mg g-1 and an analysis accuracy of 0.02% to 2.0%.
-
Wide Range of Elemental Analysis:
- XRF can analyze elements from Beryllium (Be) to Uranium (U), although lighter elements (below Sodium) are harder to detect.
- It offers a wide linear range of analyzed element content, from trace levels (0.0001%) to high concentrations (99.999%).
-
Minimal Sample Preparation:
- XRF requires little to no sample preparation, allowing for direct analysis of solid, liquid, or powdered samples.
- This reduces the time and cost associated with sample preparation, making XRF a convenient choice for many applications.
-
Applications of XRF:
- XRF is widely used in industries for quality control, material verification, and coating thickness measurement.
- It is also used in research and development for elemental analysis and material characterization.
-
Detection Depth:
- The detection depth of XRF ranges from 0.03 mm to 3 mm, depending on the sample and the elements being analyzed.
- This makes XRF suitable for analyzing both surface layers and bulk materials.
-
Instrument Features:
- Modern XRF instruments are equipped with advanced electronics and state-of-the-art algorithms, providing high-quality measurements within seconds.
- Many XRF systems feature touch screen displays for easy operation, requiring minimal training for users.
In summary, the spot size of XRF is a critical parameter that influences the analysis volume and the accuracy of the results. With its large spot size, non-destructive nature, and fast analysis capabilities, XRF is a powerful tool for elemental and material analysis across various industries.
Summary Table:
Feature | Details |
---|---|
Spot Size | 20 mm to 60 mm |
Analysis Time | 10 seconds to a few minutes |
Detection Limit | 0.0005 mg g-1 |
Accuracy | 0.02% to 2.0% |
Elemental Range | Beryllium (Be) to Uranium (U) |
Sample Preparation | Minimal or none |
Applications | Quality control, material verification, coating thickness measurement |
Detection Depth | 0.03 mm to 3 mm |
Instrument Features | Advanced electronics, touch screen displays, state-of-the-art algorithms |
Discover how XRF can revolutionize your material analysis—contact our experts today!