The synthesis of carbon nanotubes (CNTs) involves several methods, with chemical vapor deposition (CVD) being the most commercially dominant. Traditional methods like laser ablation and arc discharge are still relevant, but CVD offers scalability and control. Emerging methods focus on sustainability, utilizing green or waste feedstocks. Key factors influencing CNT growth include the use of hydrogen in thermal conversion processes, optimal residence time, and the choice of carbon sources like methane and ethylene. These factors collectively determine the efficiency, quality, and sustainability of CNT production.
Key Points Explained:
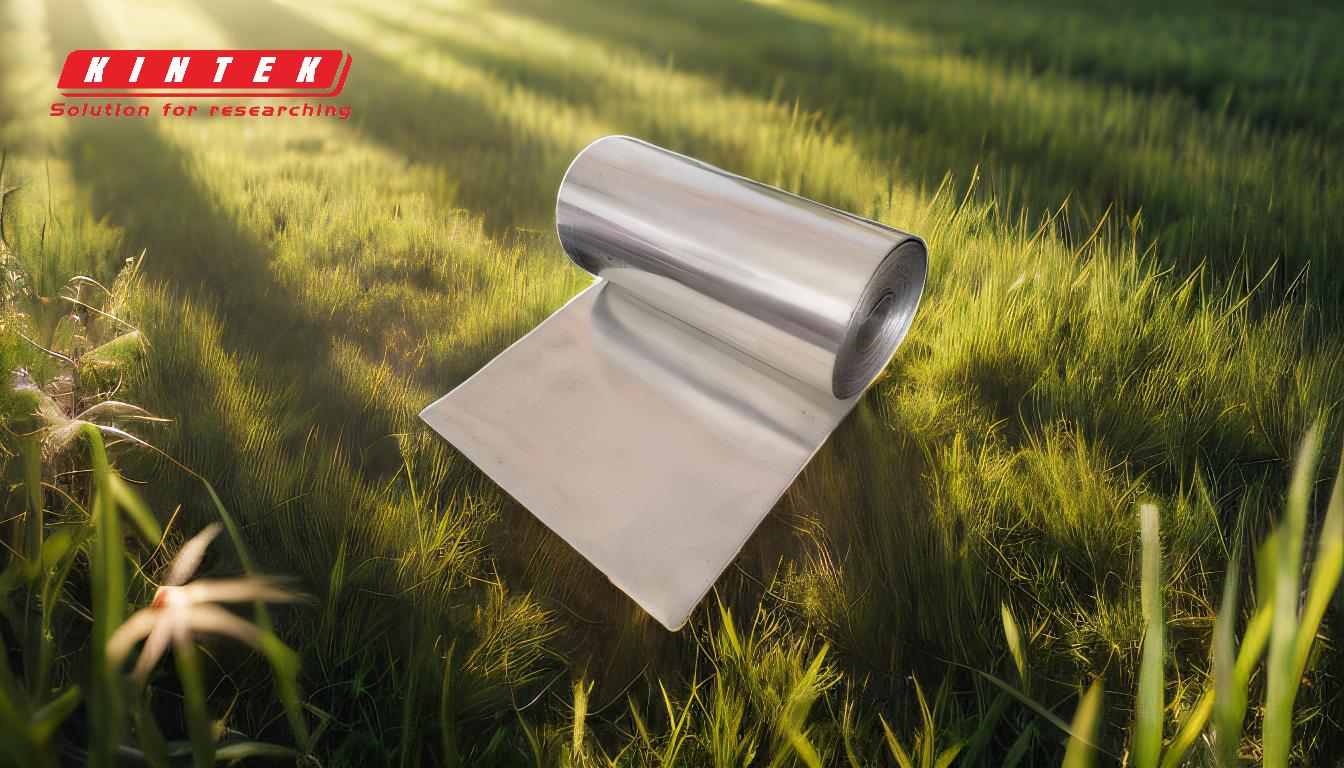
-
Traditional Methods:
- Laser Ablation: This method involves using a high-power laser to vaporize a carbon target in the presence of a catalyst. The vaporized carbon condenses to form CNTs. While effective, it is less scalable and more energy-intensive compared to CVD.
- Arc Discharge: In this method, an electric arc is generated between two carbon electrodes in an inert gas atmosphere. The arc vaporizes the carbon, which then forms CNTs. This method is also less scalable and more suited for research purposes.
-
Chemical Vapor Deposition (CVD):
- Dominant Commercial Process: CVD is the most widely used method for CNT synthesis due to its scalability and control over the growth process. It involves decomposing a carbon-containing gas (like methane or ethylene) on a substrate coated with a metal catalyst (like iron, cobalt, or nickel) at high temperatures.
- Process Details: The carbon source gas is introduced into a reaction chamber where it decomposes at high temperatures (typically 600-1200°C). The carbon atoms then diffuse into the catalyst particles, forming CNTs as they grow.
-
Emerging Methods:
- Green or Waste Feedstocks: Newer methods focus on sustainability by using carbon dioxide captured by electrolysis in molten salts or methane pyrolysis. These methods aim to reduce the environmental impact of CNT production.
- Sustainability: Using waste or green feedstocks not only reduces the carbon footprint but also makes the process more economically viable by utilizing readily available materials.
-
Role of Hydrogen:
- Thermal Conversion: Hydrogen plays a crucial role in the thermal conversion of methane and ethylene. It helps in reducing the catalyst and participating in the thermal reaction, especially at low concentrations.
- Growth Promotion: Hydrogen can promote the growth of CNTs by ensuring that the catalyst remains active and by preventing the formation of amorphous carbon, which can hinder CNT growth.
-
Residence Time:
- Optimal Residence Time: Maintaining an optimal residence time is crucial for achieving a high growth rate of CNTs. Too short a residence time may result in insufficient carbon source accumulation, leading to material waste. Conversely, too long a residence time may cause limited carbon source replenishment and by-product accumulation.
- Balancing Act: The residence time must be carefully balanced to ensure efficient use of the carbon source and to maximize the yield and quality of the CNTs.
In summary, the synthesis of carbon nanotubes involves a combination of traditional and emerging methods, with CVD being the most commercially viable. Factors like the use of hydrogen, optimal residence time, and sustainable feedstocks play critical roles in determining the efficiency and sustainability of CNT production.
Summary Table:
Aspect | Details |
---|---|
Traditional Methods | Laser ablation and arc discharge, less scalable but effective for research. |
CVD (Dominant Method) | Scalable, controlled process using carbon gases and catalysts at high temps. |
Emerging Methods | Focus on sustainability using green or waste feedstocks. |
Role of Hydrogen | Promotes CNT growth, reduces catalyst, and prevents amorphous carbon. |
Residence Time | Optimal timing ensures efficient carbon source use and high CNT yield. |
Interested in optimizing your carbon nanotube synthesis process? Contact our experts today for tailored solutions!