The temperature and holding time for sintering are critical parameters that depend on the material being processed, the desired properties of the final product, and the specific sintering technique used. Sintering temperatures typically range from 70% to 90% of the material's melting point, and the holding time can vary from milliseconds to over 24 hours. These parameters influence porosity, density, strength, and hardness of the sintered body. High temperatures and long holding times can reduce porosity and increase density but may also lead to defects or grain growth, while insufficient sintering can degrade material properties. The choice of sintering conditions must balance these factors to achieve the desired product characteristics.
Key Points Explained:
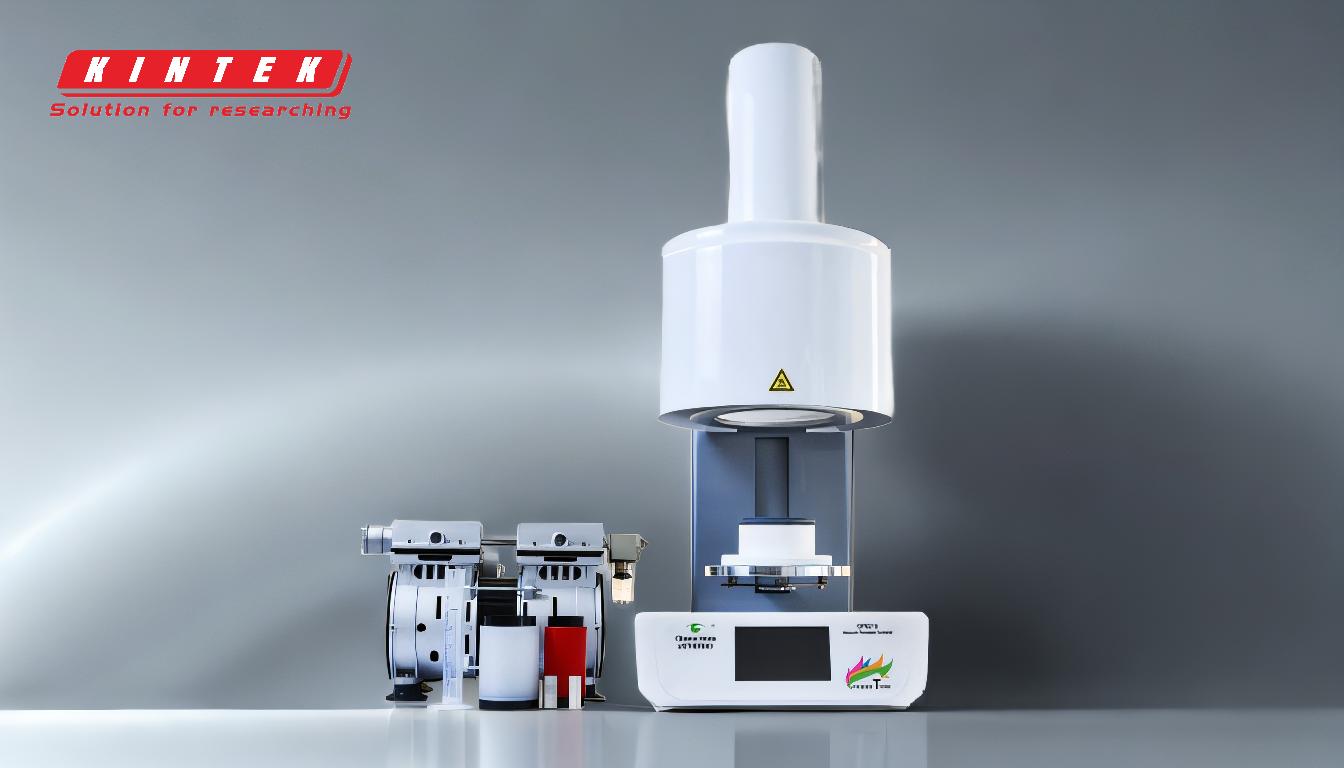
-
Dependence on Material and Desired Properties:
- The sintering temperature and holding time are tailored to the specific material and the required density, strength, and hardness of the final part.
- For example, metals like steel or titanium may require higher temperatures (e.g., 1000°C to 1400°C) compared to ceramics or polymers.
-
Typical Temperature Range:
- Sintering temperatures are generally 70% to 90% of the material's melting point.
- For instance, if a material has a melting point of 1500°C, the sintering temperature might range from 1050°C to 1350°C.
-
Holding Time Variability:
- Holding times can range from milliseconds (in techniques like spark plasma sintering) to several hours (in traditional furnace sintering).
- Longer holding times are often used for materials requiring high densification, while shorter times may be sufficient for materials with lower melting points or when using advanced techniques.
-
Influence on Material Properties:
- High Temperature and Long Holding Time: Can reduce porosity and increase density but may cause grain growth, defects, or reduced mechanical properties.
- Low Temperature or Short Holding Time: May result in insufficient densification, leading to poor mechanical properties and higher porosity.
-
Role of Sintering Atmosphere:
- The sintering atmosphere (e.g., air, vacuum, argon, or nitrogen) can affect the process by preventing oxidation or controlling diffusion rates.
- For example, vacuum sintering is often used for materials prone to oxidation, like titanium.
-
Impact of Particle Size and Composition:
- Smaller particle sizes and homogeneous compositions promote better densification and faster sintering.
- Larger particles or heterogeneous compositions may require higher temperatures or longer holding times.
-
Advanced Sintering Techniques:
- Techniques like selective laser sintering (SLS) or field-assisted sintering (FAST) can reduce sintering times significantly.
- For example, FAST can achieve full densification in minutes, compared to hours in traditional furnaces.
-
Trade-offs in Sintering Parameters:
- Increasing temperature or holding time can improve density and strength but may also increase the risk of defects or grain growth.
- Faster sintering techniques may reduce processing time but could result in residual porosity or uneven densification.
-
Importance of Cooling Rate:
- The cooling rate after sintering can influence the final microstructure and properties.
- Controlled cooling is often used to prevent thermal stresses or phase transformations that could degrade material performance.
-
Optimization for Specific Applications:
- The choice of sintering parameters depends on the application requirements, such as high strength, wear resistance, or thermal conductivity.
- For example, sintering conditions for aerospace components may prioritize strength and fatigue resistance, while those for biomedical implants may focus on biocompatibility and corrosion resistance.
By carefully balancing these factors, manufacturers can achieve the desired properties in sintered materials while minimizing defects and processing costs. The optimal sintering process is a trade-off between material characteristics, processing techniques, and application requirements.
Summary Table:
Factor | Impact on Sintering |
---|---|
Material Type | Determines required temperature and holding time (e.g., metals vs. ceramics). |
Temperature Range | Typically 70%-90% of the material's melting point. |
Holding Time | Ranges from milliseconds (spark plasma sintering) to hours (traditional sintering). |
Sintering Atmosphere | Prevents oxidation or controls diffusion (e.g., vacuum for titanium). |
Particle Size | Smaller particles promote faster and better densification. |
Advanced Techniques | FAST or SLS reduces sintering time significantly. |
Cooling Rate | Influences microstructure and prevents thermal stresses. |
Application Requirements | Tailored for strength, wear resistance, or biocompatibility (e.g., aerospace vs. biomedical). |
Need help optimizing your sintering process? Contact our experts today for tailored solutions!