The temperature of a cracking furnace, also known as a pyrolysis furnace, is a critical parameter that directly impacts the efficiency and performance of the cracking process. Cracking furnaces are used in industries such as petrochemicals to break down large hydrocarbon molecules into smaller, more valuable ones. The temperature in these furnaces typically ranges between 750°C and 900°C, depending on the specific process and feedstock being used. Factors such as residence time, pressure, and proper maintenance also play a significant role in ensuring optimal performance and safety. Below, we explore the key aspects of cracking furnace temperatures and their implications.
Key Points Explained:
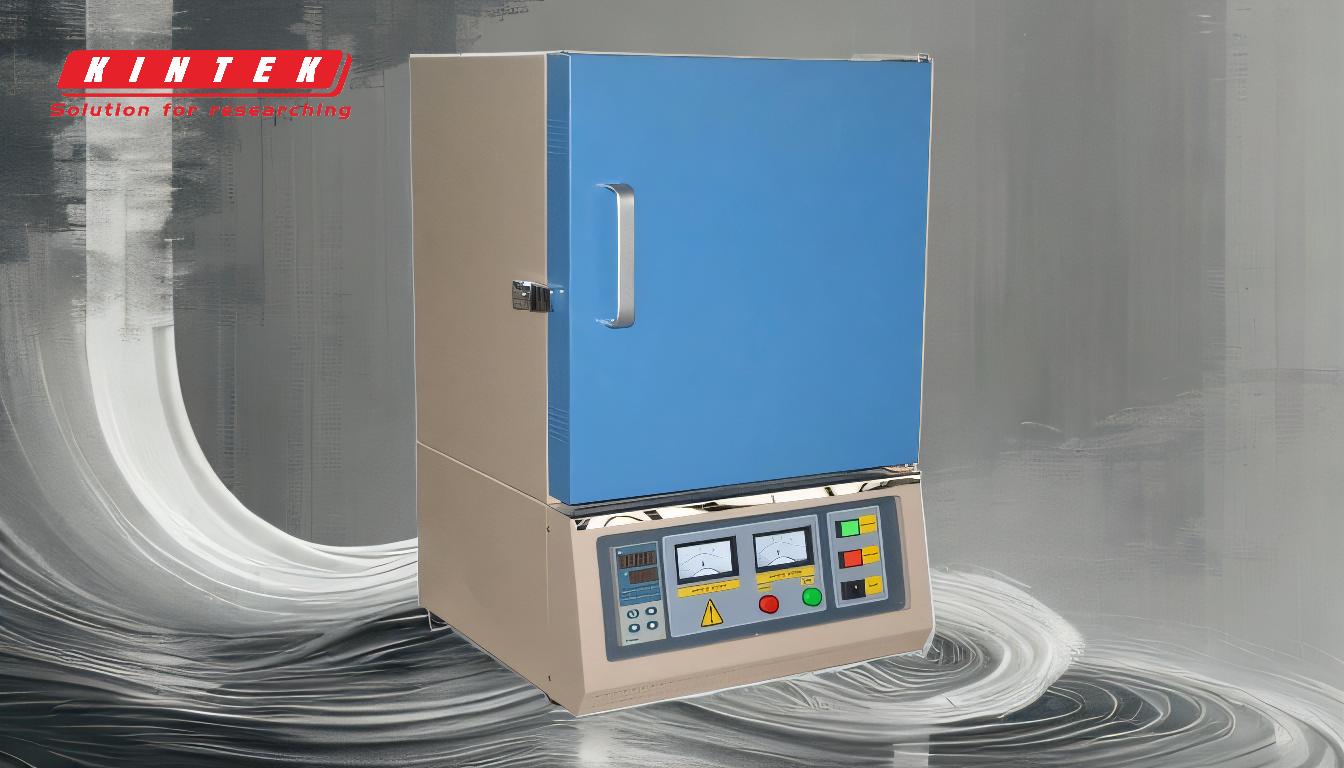
-
Typical Temperature Range of a Cracking Furnace
- The temperature in a cracking furnace generally ranges between 750°C and 900°C.
- This high temperature is necessary to provide the energy required to break the chemical bonds in large hydrocarbon molecules, a process known as thermal cracking.
- The exact temperature depends on the type of feedstock (e.g., naphtha, ethane, or propane) and the desired end products (e.g., ethylene, propylene).
-
Factors Influencing Furnace Temperature
- Feedstock Composition: Different hydrocarbons require different temperatures for optimal cracking. For example, lighter feedstocks like ethane may require lower temperatures compared to heavier feedstocks like naphtha.
- Residence Time: The time the feedstock spends in the furnace affects the cracking efficiency. Longer residence times at lower temperatures can achieve similar results to shorter times at higher temperatures.
- Pressure: Operating pressure can influence the cracking temperature. Lower pressures often favor cracking reactions, allowing for slightly lower temperatures.
- Furnace Design: The design of the furnace, including burner configuration and heat distribution, plays a role in maintaining consistent temperatures.
-
Importance of Temperature Control
- Optimal Cracking Efficiency: Maintaining the correct temperature ensures that the feedstock is cracked efficiently, maximizing the yield of valuable products like ethylene and propylene.
- Safety: Excessive temperatures can lead to unwanted side reactions, such as coking, which can damage the furnace and reduce its lifespan.
- Energy Consumption: Proper temperature control minimizes energy waste, reducing operational costs and environmental impact.
-
Challenges in Temperature Management
- Temperature Fluctuations: Variations in feedstock composition or flow rates can cause temperature fluctuations, requiring precise control systems.
- Coking and Deposits: High temperatures can lead to the formation of coke deposits on furnace walls and tubes, reducing heat transfer efficiency and increasing the risk of overheating.
- Aging Equipment: Over time, furnace components may degrade, making it harder to maintain consistent temperatures. Regular maintenance is essential to address these issues.
-
Comparison with Other Furnace Types
- Unlike continuous furnaces used for heat treatment processes (e.g., annealing or hardening), cracking furnaces operate at much higher temperatures and are designed for specific chemical reactions.
- Dental furnaces, for example, operate at much lower temperatures (typically below 1500°C) and are influenced by different factors, such as the type of materials being fired (e.g., ceramics or alloys).
-
Operational and Maintenance Considerations
- Monitoring Systems: Advanced temperature monitoring and control systems are essential for maintaining optimal conditions in a cracking furnace.
- Regular Maintenance: Cleaning furnace tubes to remove coke deposits and inspecting burners and heat exchangers can prevent temperature-related issues.
- Energy Efficiency: Proper burner settings and furnace design adjustments can reduce energy consumption while maintaining the required temperature.
In summary, the temperature of a cracking furnace is a critical parameter that must be carefully controlled to ensure efficient and safe operation. By understanding the factors that influence temperature and implementing proper maintenance practices, operators can optimize the performance of their cracking furnaces and achieve the desired product yields.
Summary Table:
Key Aspect | Details |
---|---|
Temperature Range | 750°C–900°C, depending on feedstock and process. |
Key Factors | Feedstock, residence time, pressure, and furnace design. |
Importance of Control | Ensures efficiency, safety, and energy savings. |
Challenges | Temperature fluctuations, coking, and aging equipment. |
Maintenance Tips | Regular cleaning, advanced monitoring, and energy-efficient adjustments. |
Need expert advice on cracking furnace temperature control? Contact us today for tailored solutions!