The temperature of a rotating kiln is not fixed and varies significantly depending on the material being processed and the specific industrial application. Generally, rotary kilns operate within a wide temperature range, from as low as 200°C to as high as 2500°C. For example, indirect rotary kilns typically maintain furnace tube temperatures between 1200-1300°C, while the material inside remains below 1150°C. The exact temperature is influenced by factors such as the material's chemical composition, heat of reaction, thermal conductivity, and the desired process outcomes. Additionally, the design and size of the kiln, including factors like retention time and bed profile, also play a role in determining the operating temperature.
Key Points Explained:
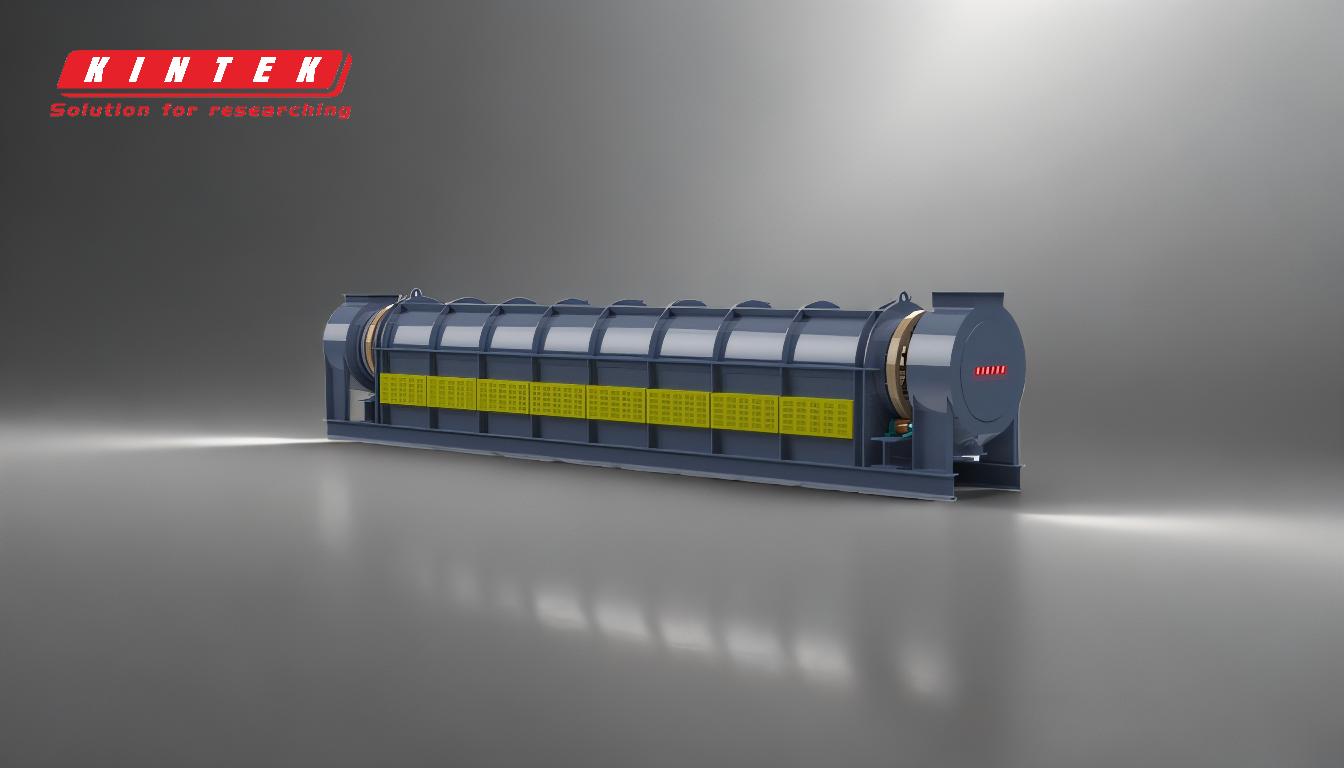
-
General Temperature Range of Rotary Kilns:
- Rotary kilns operate within a broad temperature range, typically from 200°C to 2500°C, depending on the material and process requirements.
- This wide range allows rotary kilns to support diverse industrial applications, from low-temperature processes like drying to high-temperature processes like calcination or sintering.
-
Temperature in Indirect Rotary Kilns:
- In indirect rotary kilns, the furnace tube temperature is maintained between 1200-1300°C, while the material inside the kiln remains at a lower temperature, typically less than 1150°C.
- This design ensures that the material is heated indirectly, reducing direct exposure to extreme temperatures and minimizing potential damage or unwanted reactions.
-
Factors Influencing Kiln Temperature:
- Material Properties: The temperature is heavily influenced by the material's chemical composition, particle size distribution, bulk density, abrasiveness, corrosiveness, specific heat, heat of reaction, and thermal conductivity.
- Process Requirements: The desired outcome of the process (e.g., drying, calcination, or reduction) dictates the temperature profile needed.
- Kiln Design: Factors such as retention time, bed profile, and heat generation from material combustion or volatilization also affect the operating temperature.
-
Zoning in Electric Heating Rotary Kilns:
- Electric heating rotary kilns often include multiple temperature zones, such as a pre-heating zone and a high-temperature heating zone.
- Each zone can be set to a specific temperature based on the process requirements, allowing for precise control over the heating process.
-
Reducing Conditions and Temperature:
- In processes requiring reducing conditions, the temperature is influenced by:
- The temperature, reactivity, and quantity of the reductant.
- The residence time of the material in the kiln.
- The charge holdup at the discharge end of the kiln, which affects how long the material is exposed to reducing conditions.
- In processes requiring reducing conditions, the temperature is influenced by:
-
Design and Size Considerations:
- The size and design of the kiln are tailored to the required capacity, heat generation, feed rate, retention time, and desired bed profile.
- These factors ensure that the kiln can achieve the necessary temperature profiles for the specific material and process.
By understanding these key points, a purchaser can better evaluate the temperature requirements for their specific application and select a rotary kiln that meets their process needs.
Summary Table:
Aspect | Details |
---|---|
General Temperature Range | 200°C to 2500°C, depending on material and process requirements. |
Indirect Rotary Kiln | Furnace tube: 1200-1300°C; Material: <1150°C. |
Key Influencing Factors | Material properties, process requirements, kiln design, and zoning. |
Electric Heating Kilns | Multiple zones (e.g., pre-heating, high-temperature) for precise control. |
Reducing Conditions | Temperature influenced by reductant properties, residence time, and holdup. |
Need help selecting the right rotary kiln for your application? Contact our experts today for tailored solutions!