Arc melting is a high-temperature process used in metallurgy to melt metals using an electric arc. The temperature of arc melting typically ranges between 3000°C and 3500°C, depending on the operational conditions and the type of furnace used. This process is highly efficient for melting metals like scrap steel without altering their chemical properties. The electric arc is generated by converting 220V or 380V into a low voltage and high current, creating a self-sustaining discharge phenomenon that maintains stable combustion. This makes arc melting a reliable and effective method for industrial metal melting applications.
Key Points Explained:
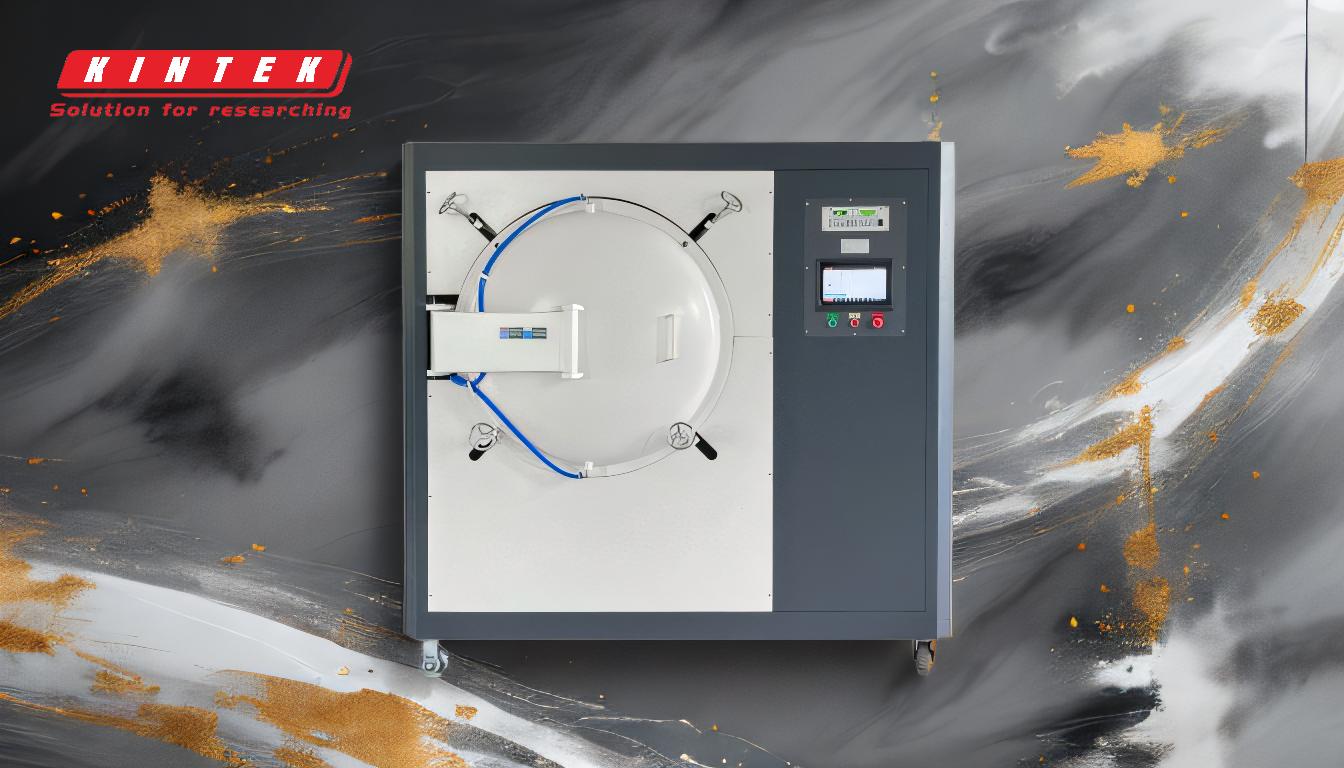
-
Definition of Arc Melting:
- Arc melting is an electrothermal metallurgical method where electric energy is used to generate an electric arc.
- The arc is formed between the electrode and the material to be melted or between two electrodes.
- This process is primarily used for melting metals, such as scrap steel, without altering their chemical properties.
-
Temperature Range of Arc Melting:
- The electric arc in an arc melting furnace produces temperatures between 3000°C and 3500°C.
- This high temperature is sufficient to melt most metals, including steel, efficiently and quickly.
- The maximum temperature of an arc melting furnace is typically around 3000°C.
-
Mechanism of Arc Melting:
- The arc is generated by converting standard voltages (220V or 380V) into a low voltage and high current.
- The arc is triggered by the instantaneous short circuit of the positive and negative poles.
- Once initiated, the arc is a self-sustaining discharge phenomenon that maintains stable combustion without extinguishing.
-
Applications of Arc Melting:
- Arc melting is widely used in industrial settings for melting metals, particularly scrap steel.
- It is favored for its ability to melt metals quickly and efficiently without altering their chemical composition.
- This method is also used in specialized applications, such as the production of high-purity metals and alloys.
-
Advantages of Arc Melting:
- High Efficiency: The process can reach extremely high temperatures quickly, making it energy-efficient.
- Precision: The temperature can be controlled to ensure the metal is melted without overheating.
- Versatility: Suitable for a wide range of metals and alloys.
- Consistency: The self-sustaining nature of the arc ensures stable and consistent melting conditions.
-
Technical Details of Arc Melting Furnaces:
- The main component of an arc melting furnace is the electric welder, which generates the arc.
- The furnace operates under low tension (L.T.) conditions, which help maintain the high temperatures required for melting.
- The design of the furnace ensures that the arc remains stable and does not extinguish during operation.
-
Comparison with Other Melting Methods:
- Induction Melting: While induction melting is also used for melting metals, it typically operates at lower temperatures (up to 1600°C) compared to arc melting.
- Resistance Melting: Resistance melting relies on electrical resistance to generate heat, but it is generally less efficient and reaches lower temperatures than arc melting.
- Arc Melting vs. Blast Furnace: Arc melting is more energy-efficient and faster than traditional blast furnaces, which rely on combustion and can take longer to reach the required temperatures.
-
Challenges and Considerations:
- Energy Consumption: While efficient, arc melting still requires significant electrical energy to maintain the high temperatures.
- Equipment Wear: The high temperatures and intense energy can lead to wear and tear on the furnace components, requiring regular maintenance.
- Safety: The high temperatures and electrical energy involved necessitate strict safety protocols to prevent accidents.
By understanding these key points, a purchaser or user of arc melting equipment can make informed decisions about its application, maintenance, and operational requirements. The process is highly effective for industrial metal melting, offering a combination of high efficiency, precision, and versatility.
Summary Table:
Aspect | Details |
---|---|
Temperature Range | 3000°C – 3500°C |
Key Applications | Melting scrap steel, high-purity metals, and alloys |
Mechanism | Electric arc generated by converting 220V/380V to low voltage, high current |
Advantages | High efficiency, precision, versatility, and consistent melting conditions |
Challenges | High energy consumption, equipment wear, and safety concerns |
Interested in arc melting solutions? Contact our experts today for tailored advice!