The temperature for HVAC brazing typically ranges between 1100°F (593°C) and 1500°F (816°C), depending on the type of brazing alloy used and the specific application. Brazing is a process that joins metal parts by melting and flowing a filler metal into the joint, which has a lower melting point than the base metals. In HVAC systems, brazing is commonly used to join copper tubing and other components, ensuring strong, leak-free connections. The choice of temperature depends on the filler metal (e.g., silver-based or phosphorus-copper alloys) and the materials being joined. Proper temperature control is critical to avoid overheating, which can weaken the joint or damage the components.
Key Points Explained:
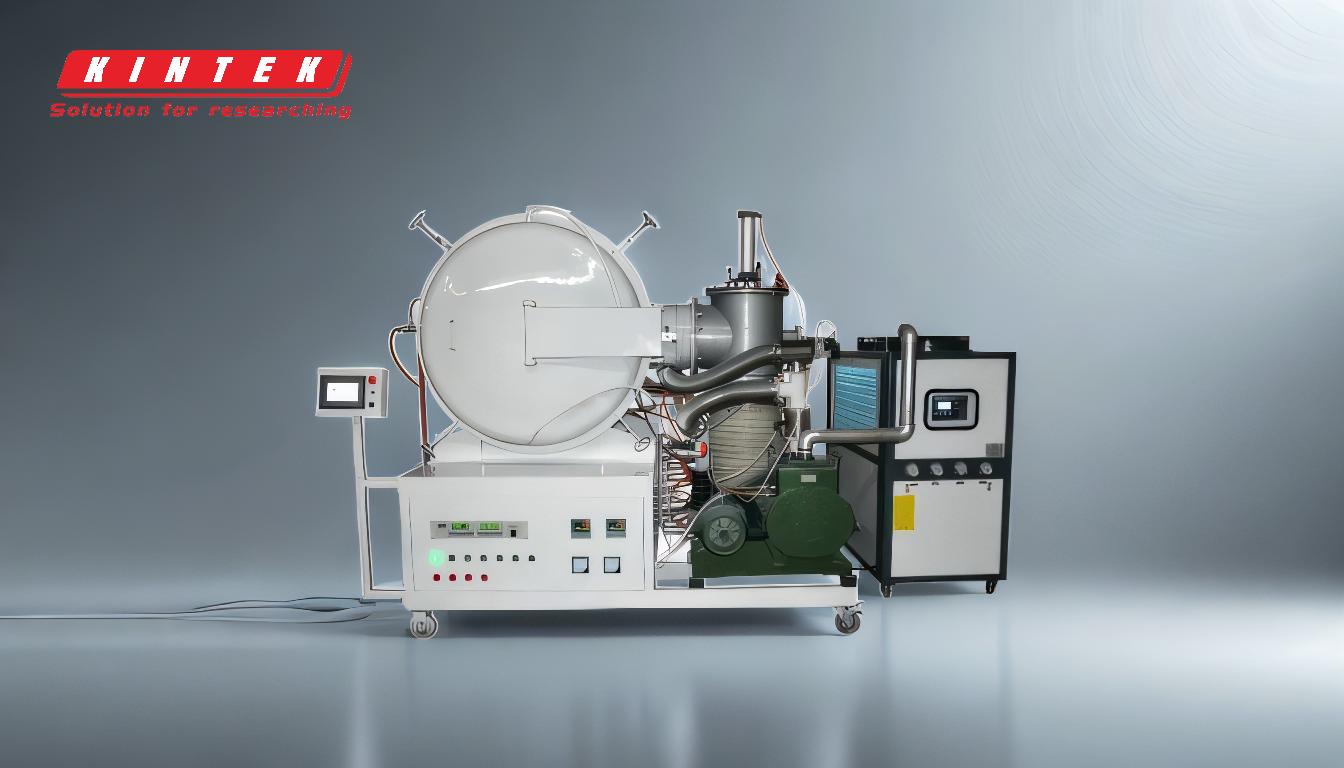
-
Typical Temperature Range for HVAC Brazing:
- The temperature for HVAC brazing generally falls between 1100°F (593°C) and 1500°F (816°C).
- This range ensures the filler metal melts and flows properly without damaging the base materials, such as copper tubing.
-
Factors Influencing Brazing Temperature:
-
Filler Metal Type: Different brazing alloys have varying melting points. For example:
- Silver-based alloys melt at around 1100°F to 1400°F (593°C to 760°C).
- Phosphorus-copper alloys melt at approximately 1300°F to 1500°F (704°C to 816°C).
- Base Material: Copper, commonly used in HVAC systems, requires precise temperature control to avoid oxidation or warping.
- Joint Design: The size and complexity of the joint can influence the required temperature and heating time.
-
Filler Metal Type: Different brazing alloys have varying melting points. For example:
-
Importance of Temperature Control:
- Overheating can lead to:
- Oxidation of the metal surfaces.
- Weakening of the joint due to excessive melting of the base metal.
- Damage to nearby components or insulation.
- Underheating can result in:
- Incomplete melting of the filler metal, leading to weak or leaky joints.
- Poor adhesion between the filler metal and the base materials.
- Overheating can lead to:
-
Common Brazing Alloys Used in HVAC:
- Silver-Based Alloys: These are popular due to their lower melting points and excellent flow characteristics. They are often used for joining copper tubing in HVAC systems.
- Phosphorus-Copper Alloys: These are self-fluxing when used with copper, eliminating the need for additional flux. They are suitable for high-strength joints.
-
Brazing Process in HVAC Systems:
- Preparation: Clean the surfaces to be joined to remove any contaminants, such as oil or oxidation.
- Application of Flux: Apply flux (if required) to prevent oxidation during heating.
- Heating: Use a torch or furnace to heat the joint evenly to the desired temperature.
- Filler Metal Application: Introduce the filler metal into the joint, allowing it to flow and fill the gap.
- Cooling: Allow the joint to cool naturally to ensure a strong, durable connection.
-
Safety Considerations:
- Proper ventilation is essential to avoid inhaling fumes from the flux or filler metal.
- Use appropriate personal protective equipment (PPE), such as gloves and safety glasses, to protect against burns and UV radiation from the torch.
-
Applications in HVAC Systems:
- Brazing is widely used for:
- Joining copper refrigerant lines.
- Connecting evaporator and condenser coils.
- Repairing or replacing damaged tubing in HVAC systems.
- Brazing is widely used for:
By understanding the temperature requirements and factors influencing HVAC brazing, technicians can ensure strong, reliable joints that are essential for the efficient operation of HVAC systems.
Summary Table:
Aspect | Details |
---|---|
Temperature Range | 1100°F to 1500°F (593°C to 816°C) |
Filler Metal Types | Silver-based alloys: 1100°F–1400°F; Phosphorus-copper alloys: 1300°F–1500°F |
Base Material | Copper (requires precise temperature control) |
Key Considerations | Avoid overheating or underheating to ensure strong, leak-free joints |
Common Applications | Joining copper refrigerant lines, evaporator/condenser coils, and repairs |
Need expert advice on HVAC brazing? Contact us today for tailored solutions!