The sintering temperature varies depending on the material and application, but it generally occurs at elevated temperatures, often above 1800°F (982°C). For specific materials like zirconia, optimal sintering occurs around 1500°C–1550°C, with deviations leading to reduced strength. The sintering process is influenced by factors such as heating rate, cooling rate, and temperature consistency during the hold time. High temperatures promote particle bonding, grain growth, and densification, but excessive temperatures can cause issues like uneven sintering or reduced material strength. Shielding gases or controlled atmospheres are often used to prevent contamination during sintering.
Key Points Explained:
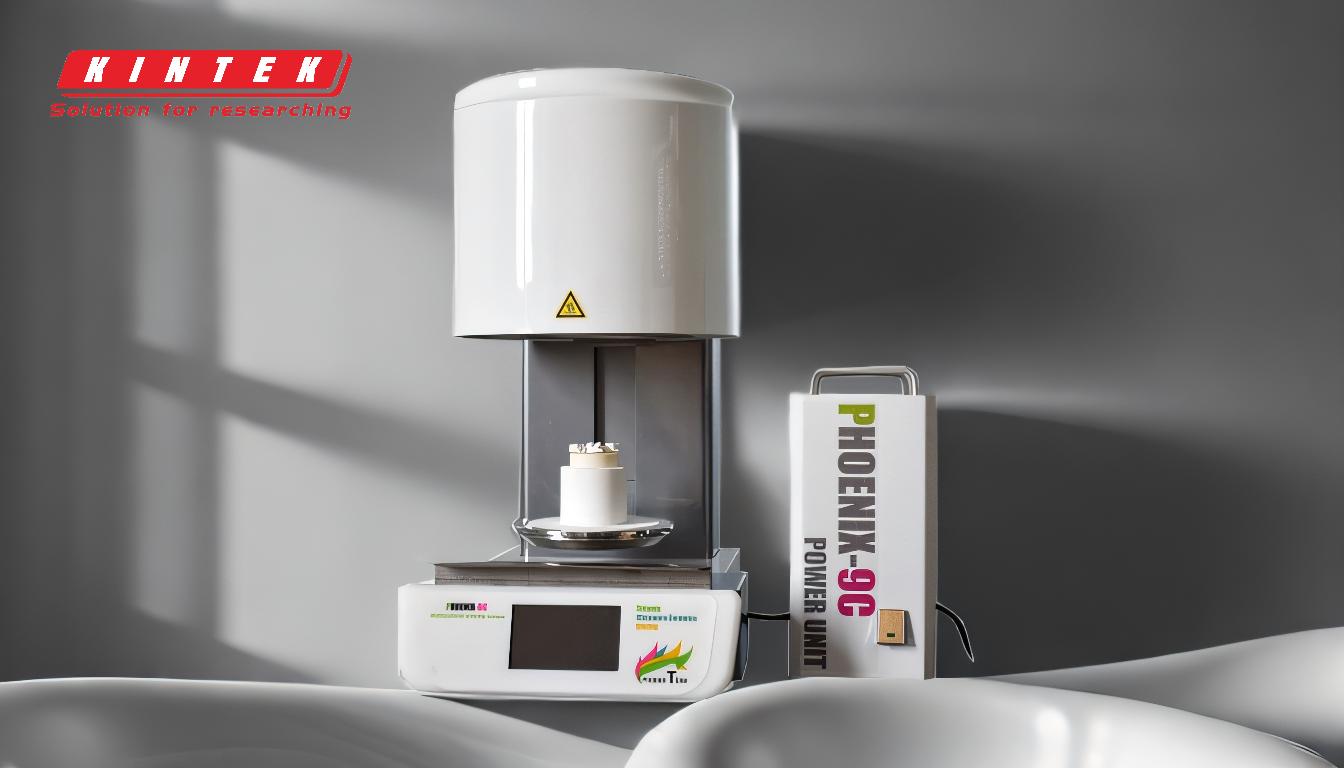
-
General Sintering Temperature Range:
- Sintering typically occurs at elevated temperatures, often above 1800°F (982°C).
- The exact temperature depends on the material and application, with some processes requiring temperatures as high as 1800°C or more.
-
Material-Specific Sintering Temperatures:
- For zirconia, the optimal sintering temperature is around 1500°C–1550°C. Deviations of just 150°C can significantly reduce material strength.
- At 1500°C, zirconia achieves a strength of about 1280 MPa.
- At 1600°C, strength drops to about 980 MPa.
- At 1700°C, strength further decreases to about 600 MPa.
- This highlights the importance of precise temperature control for specific materials.
- For zirconia, the optimal sintering temperature is around 1500°C–1550°C. Deviations of just 150°C can significantly reduce material strength.
-
Critical Temperature Phases:
- From room temperature to 900°C, there is little effect on the material.
- The ramp rate from 900°C to the top temperature, the consistency of temperature during the hold time, and the cooling rate back to about 900°C are critical for achieving optimal results.
-
Heating Rate Considerations:
- If the heating rate is too high, it can lead to uneven sintering, with insufficient sintering inside the blank and significant differences in sintering degree across different areas.
- This can result in high-temperature melting peaks and high crystallinity, which may negatively impact material properties.
-
Atmosphere and Contamination Control:
- Sintering often requires a controlled atmosphere, such as inert, reducing, or oxidizing gases, to prevent surface contamination.
- For metals, especially those sintered at atmospheric pressure, shielding gases like endothermic gas are commonly used.
-
High-Temperature Effects:
- High temperatures promote bonding and diffusion between powder particles, leading to grain growth and densification.
- However, excessively high temperatures can cause issues like grain overgrowth, which reduces material strength.
-
Practical Implications for Equipment and Consumables Purchasers:
- When selecting sintering equipment, ensure it offers precise temperature control, especially for materials like zirconia that require narrow temperature ranges.
- Consider furnaces with reliable shielding gas systems to maintain material integrity during sintering.
- Evaluate the heating and cooling rates of the equipment to ensure uniform sintering and avoid defects.
By understanding these key points, purchasers can make informed decisions about sintering equipment and consumables, ensuring optimal results for their specific applications.
Summary Table:
Key Factor | Details |
---|---|
General Sintering Range | Above 1800°F (982°C), up to 1800°C or more for specific materials. |
Zirconia Sintering Range | 1500°C–1550°C; deviations of 150°C can reduce strength significantly. |
Critical Phases | Ramp rate, hold time, and cooling rate between 900°C and top temperature. |
Heating Rate Impact | High rates cause uneven sintering, leading to defects. |
Atmosphere Control | Inert or shielding gases prevent contamination during sintering. |
High-Temperature Effects | Promotes bonding but excessive heat reduces strength due to grain overgrowth. |
Need precise sintering equipment for your materials? Contact our experts today to find the perfect solution!