The sintering temperature varies significantly depending on the material, application, and desired characteristics. Generally, sintering occurs at elevated temperatures, typically ranging from 750°C to 1800°C. For some materials, such as metals, sintering temperatures can exceed 1800°C, especially in specialized applications. The process involves heating powdered materials to a temperature below their melting point, allowing particles to bond and densify. The temperature ramp rate, hold time, and cooling rate are critical factors that influence the final properties of the sintered product. Additionally, the sintering atmosphere (inert, reducing, or oxidizing) plays a crucial role in preventing oxidation and ensuring successful sintering.
Key Points Explained:
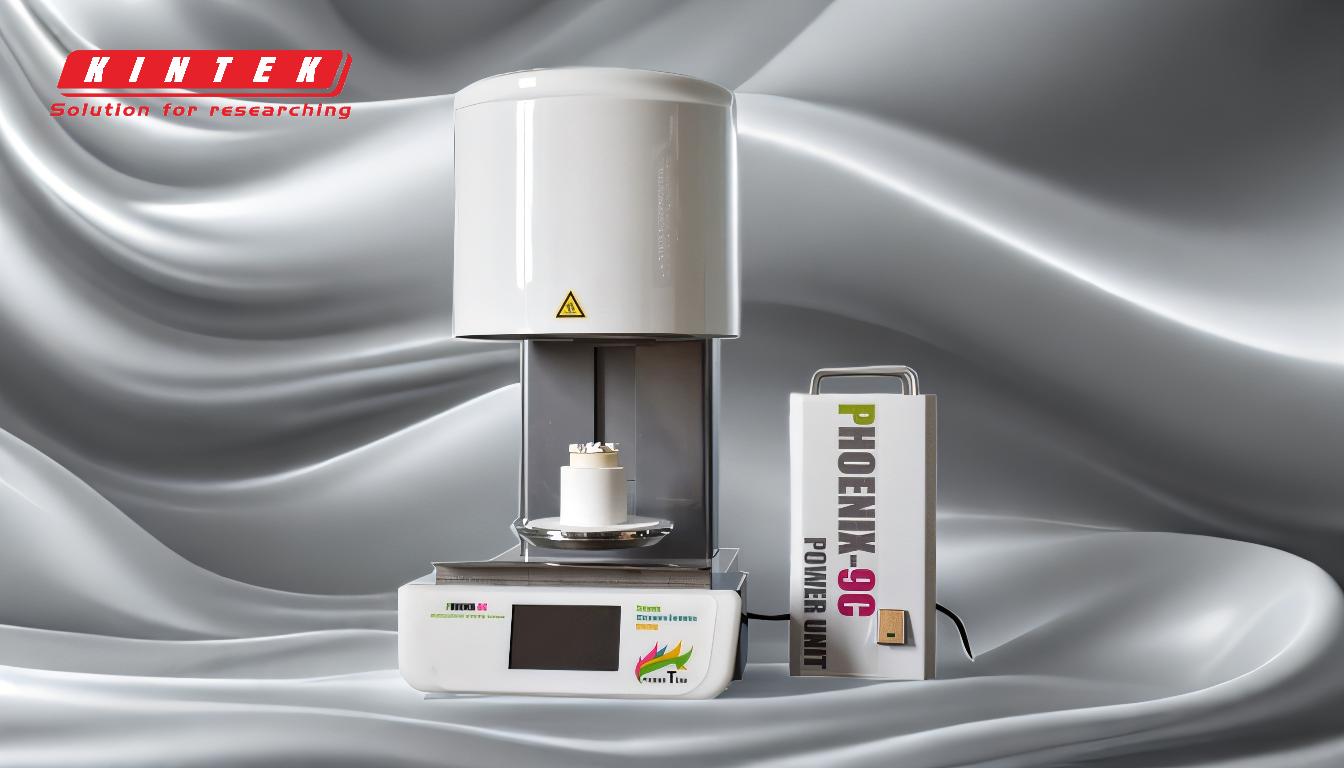
-
General Sintering Temperature Range:
- Sintering typically occurs at temperatures between 750°C and 1800°C.
- The exact temperature depends on the material being sintered and the desired properties of the final product.
- For example, metals like copper, bronze, and steel often require higher temperatures, sometimes exceeding 1800°C.
-
Critical Temperature Zones:
- Room Temperature to 900°C: This range has minimal impact on the material, but it is essential for preheating and preparing the material for sintering.
- 900°C to Top Temperature: The ramp rate during this phase is critical. A controlled and consistent increase in temperature ensures uniform bonding and avoids defects.
- Hold Time at Top Temperature: Maintaining a consistent temperature during the hold time is crucial for achieving optimal densification and material properties.
- Cooling Phase: The rate of cooling back to around 900°C must be carefully controlled to prevent thermal stresses and ensure the desired microstructure.
-
Material-Specific Sintering Temperatures:
- Metals: Pure metals, especially those sintered in a vacuum, can withstand higher temperatures without surface contamination. For example, sintering temperatures for metals can reach 1800°C or higher.
- Ceramics and Other Materials: These materials often sinter at lower temperatures, typically between 750°C and 1300°C, depending on their composition and application.
-
Atmosphere Control:
- Inert Atmospheres: Used to prevent oxidation, especially for metals. Common gases include argon or nitrogen.
- Reducing Atmospheres: Help reduce oxides on the surface of the material, improving bonding.
- Oxidizing Atmospheres: Used in specific applications where oxidation is desired or not detrimental.
-
Supporting the Shape and Preventing Oxidation:
- Refractory Ballast: Materials like Al2O3 (for copper and bronze) or Steel Blend (for steels) are used to support the shape of the printed part during sintering.
- Sintering Carbon: Used to manage oxygen exposure, ensuring that the part does not oxidize during the sintering process.
-
Industrial Sintering Practices:
- Continuous Furnaces: Often used in industrial settings, these furnaces operate under controlled speed and atmosphere, ensuring consistent sintering conditions.
- Shielding Gases: In atmospheric pressure sintering, shielding gases like endothermic gas are used to protect the material from oxidation.
-
Experimental Sintering Temperatures:
- In some experiments, sintering temperatures as high as 1800°C have been used, particularly for advanced materials or specialized applications.
-
Importance of Temperature Control:
- Precise control of the sintering temperature, ramp rate, and cooling rate is essential for achieving the desired material properties, such as density, strength, and microstructure.
By understanding these key points, a purchaser can make informed decisions about the sintering process, ensuring that the chosen temperature and conditions align with the material and application requirements.
Summary Table:
Key Aspect | Details |
---|---|
General Temperature Range | 750°C–1800°C, depending on material and desired properties. |
Critical Temperature Zones | - Room Temp to 900°C: Preheating |
- 900°C to Top Temp: Ramp rate matters
- Hold Time: Ensures densification
- Cooling: Controlled to prevent stress | | Material-Specific Temps | - Metals: Up to 1800°C+
- Ceramics: 750°C–1300°C | | Atmosphere Control | - Inert (Argon/N2)
- Reducing (reduce oxides)
- Oxidizing (specific uses) | | Industrial Practices | - Continuous furnaces
- Shielding gases (e.g., endothermic gas) |
Need help optimizing your sintering process? Contact our experts today for tailored solutions!