The temperature of an annealing furnace depends on the material being processed and its recrystallization temperature. Annealing furnaces are designed to heat materials above their recrystallization temperature but below their melting point, typically ranging up to 1800°C. The furnace's temperature is controlled using advanced features like programmable PID controllers and high-quality heating elements, ensuring uniformity and precision. The process involves heating the material to the desired temperature, holding it for a specific duration, and then cooling it slowly to achieve the desired material properties.
Key Points Explained:
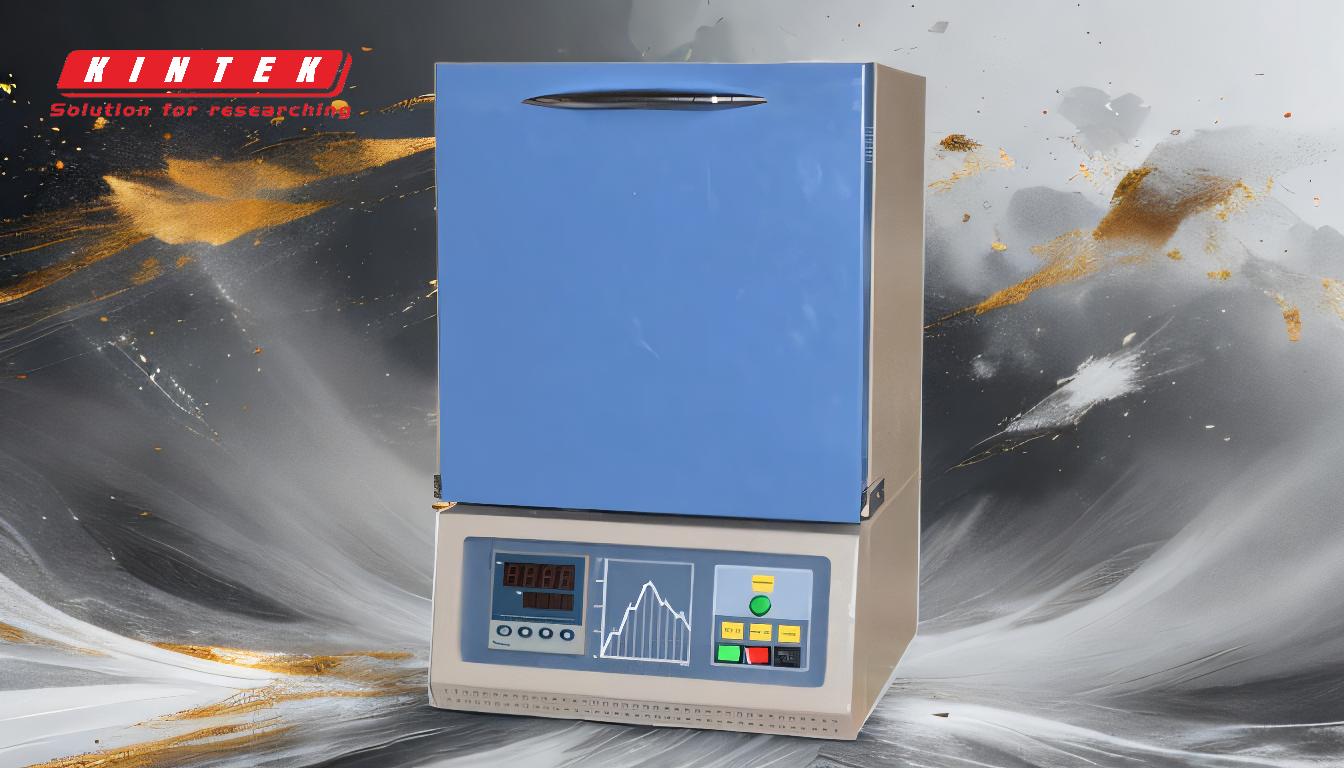
-
Purpose of Annealing Furnace Temperature:
- The primary function of an annealing furnace is to heat materials above their recrystallization temperature to improve ductility, relieve internal stresses, and modify strength and hardness. The temperature must be carefully controlled to avoid melting the material.
-
Temperature Range:
- Annealing furnaces can operate at temperatures up to 1800°C, depending on the material and its specific requirements. The furnace is designed to handle high temperatures while maintaining precision and uniformity.
-
Recrystallization Temperature:
- The recrystallization temperature varies for different materials. For example:
- Steel typically requires temperatures between 700°C to 900°C.
- Aluminum alloys may require lower temperatures, around 300°C to 500°C.
- The furnace must heat the material above this temperature but below its melting point to achieve the desired properties.
- The recrystallization temperature varies for different materials. For example:
-
Temperature Control and Uniformity:
- Modern annealing furnaces feature multisegment microprocessor-based programmable temperature controllers and PID controllers to ensure precise temperature regulation.
- Uniformity is maintained within +/-5°C, ensuring consistent results across the material.
-
Heating Elements:
- The furnace uses high-quality heating elements to achieve and maintain the required temperatures:
- Silicon carbide elements for temperatures up to 1400°C.
- Molybdenum disilicide elements for temperatures ranging from 1400°C to 1800°C.
- The furnace uses high-quality heating elements to achieve and maintain the required temperatures:
-
Cooling Process:
- After heating, the material is cooled slowly to room temperature. This controlled cooling process is crucial for forming ductile grains and achieving the desired material properties.
-
Additional Features:
- Over-temperature protection ensures safety and prevents damage to the furnace or material.
- Gas/vacuum purging options (using gases like Ar, N2, O2, H2, or CO2) allow for specialized annealing processes.
- Data logging software and communication interfaces (RS-232/RS485/Ethernet) enable monitoring and control of the annealing process.
-
Applications and Material-Specific Requirements:
- The temperature setting depends on the material being annealed. For instance:
- Copper: Typically annealed at 400°C to 700°C.
- Brass: Requires temperatures around 500°C to 700°C.
- Glass: May need temperatures up to 600°C to 800°C.
- The furnace must be adaptable to these varying requirements.
- The temperature setting depends on the material being annealed. For instance:
In summary, the temperature of an annealing furnace is tailored to the material being processed, with a focus on precision, uniformity, and safety. The advanced features of modern furnaces ensure optimal results for a wide range of materials and applications.
Summary Table:
Key Aspect | Details |
---|---|
Temperature Range | Up to 1800°C, depending on material requirements. |
Recrystallization Temp | Varies by material (e.g., Steel: 700°C–900°C, Aluminum: 300°C–500°C). |
Temperature Control | Multisegment PID controllers, uniformity within +/-5°C. |
Heating Elements | Silicon carbide (up to 1400°C), Molybdenum disilicide (1400°C–1800°C). |
Cooling Process | Slow cooling to room temperature for desired material properties. |
Additional Features | Over-temperature protection, gas/vacuum purging, data logging software. |
Applications | Copper (400°C–700°C), Brass (500°C–700°C), Glass (600°C–800°C). |
Optimize your annealing process with precision-controlled furnaces—contact us today!