Thermal cracking is a process used in the petroleum industry to break down large hydrocarbon molecules into smaller, more useful ones by applying heat. The temperature range for thermal cracking typically falls between 450°C to 750°C (842°F to 1382°F), depending on the specific process and the feedstock being used. At these high temperatures, the chemical bonds in the hydrocarbons break, leading to the formation of smaller molecules such as olefins, paraffins, and other lighter hydrocarbons. The exact temperature depends on factors such as the type of feedstock, desired products, and the specific thermal cracking method employed (e.g., steam cracking, visbreaking, or coking).
Key Points Explained:
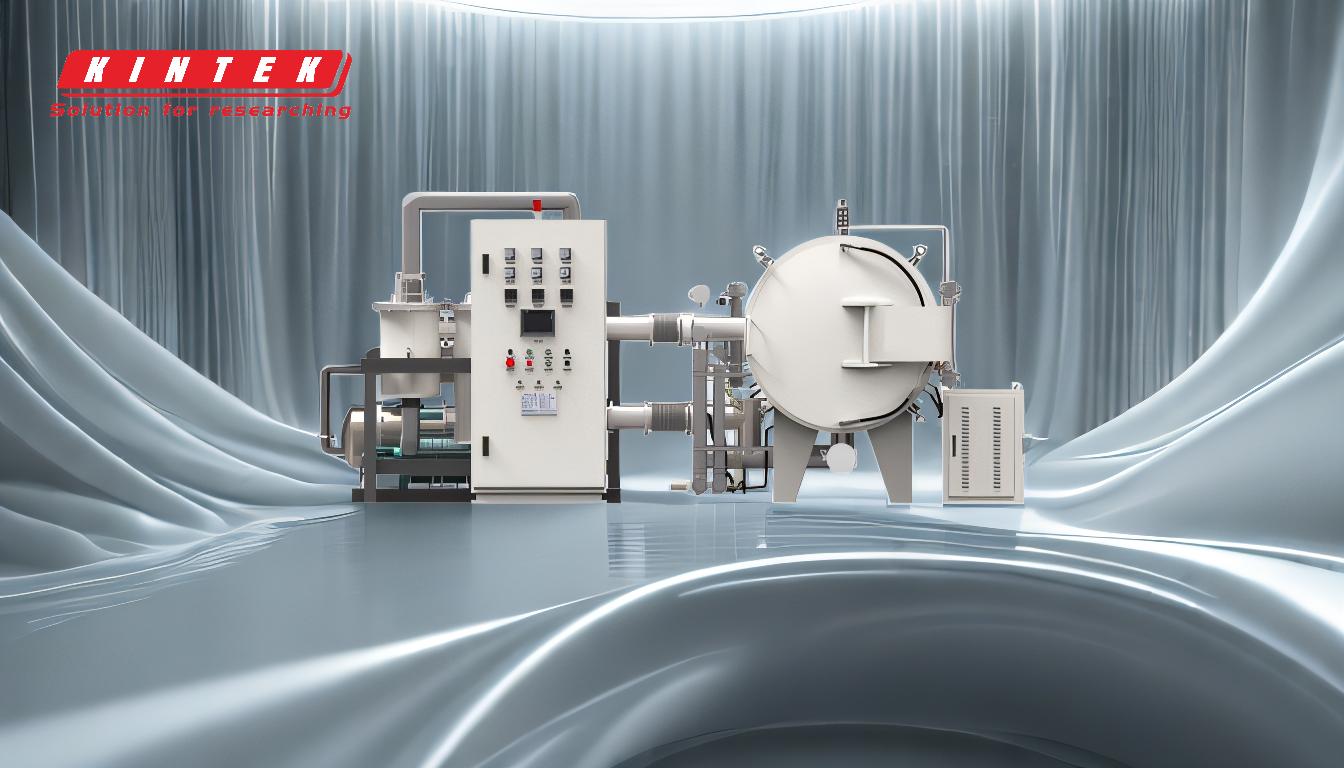
-
Definition of Thermal Cracking
- Thermal cracking is a chemical process that decomposes large hydrocarbon molecules into smaller ones by applying heat.
- It is widely used in the petroleum industry to produce lighter, more valuable products such as gasoline, diesel, and petrochemical feedstocks.
-
Temperature Range for Thermal Cracking
- The typical temperature range for thermal cracking is 450°C to 750°C (842°F to 1382°F).
- This range ensures that the chemical bonds in the hydrocarbon molecules break effectively without causing excessive degradation or unwanted side reactions.
-
Factors Influencing Temperature
- Feedstock Type: Heavier feedstocks (e.g., crude oil residues) require higher temperatures compared to lighter feedstocks (e.g., naphtha).
- Desired Products: The temperature is adjusted based on the target products. For example, producing ethylene and propylene (used in petrochemicals) often requires higher temperatures.
- Process Type: Different thermal cracking methods (e.g., steam cracking, visbreaking, coking) operate at varying temperature ranges.
-
Types of Thermal Cracking Processes
-
Steam Cracking:
- Used primarily to produce olefins (e.g., ethylene, propylene).
- Operates at temperatures of 750°C to 900°C (1382°F to 1652°F).
- Steam is added to the feedstock to reduce coke formation and improve yields.
-
Visbreaking:
- A mild thermal cracking process used to reduce the viscosity of heavy residues.
- Operates at lower temperatures, typically 450°C to 500°C (842°F to 932°F).
-
Coking:
- A severe thermal cracking process used to break down heavy residues into lighter fractions and solid coke.
- Operates at temperatures of 450°C to 550°C (842°F to 1022°F).
-
Steam Cracking:
-
Importance of Temperature Control
- Optimal Yields: Maintaining the correct temperature ensures maximum yield of desired products.
- Minimizing Side Reactions: Excessive temperatures can lead to unwanted side reactions, such as the formation of coke or gas.
- Energy Efficiency: Proper temperature control reduces energy consumption and operational costs.
-
Applications of Thermal Cracking
- Petroleum Refining: To convert heavy crude oil fractions into lighter, more valuable products.
- Petrochemical Production: To produce feedstocks for plastics, synthetic rubber, and other chemicals.
- Energy Production: To improve the quality of fuels and reduce waste.
-
Challenges and Considerations
- Coke Formation: High temperatures can lead to coke deposition, which can clog equipment and reduce efficiency.
- Material Selection: Equipment must be designed to withstand high temperatures and corrosive environments.
- Environmental Impact: Thermal cracking produces greenhouse gases and other pollutants, requiring effective mitigation strategies.
By understanding the temperature requirements and factors influencing thermal cracking, equipment and consumable purchasers can make informed decisions about the materials, technologies, and processes needed to optimize operations and achieve desired outcomes.
Summary Table:
Aspect | Details |
---|---|
Temperature Range | 450°C to 750°C (842°F to 1382°F) |
Key Factors | Feedstock type, desired products, process type |
Process Types | Steam cracking, visbreaking, coking |
Applications | Petroleum refining, petrochemical production, energy production |
Challenges | Coke formation, material selection, environmental impact |
Need thermal cracking solutions tailored to your needs? Contact our experts today for guidance!