Induction heating is a versatile and efficient method of heating conductive materials, with applications ranging from industrial processes like metal melting and heat treatment to everyday uses such as induction cooktops. The temperature range for induction heating varies widely depending on the application, material properties, and equipment used. It can achieve temperatures from a few hundred degrees Celsius for processes like brazing and soldering to over 2000°C for melting refractory metals. The precise control of temperature is achieved by adjusting the strength of the applied current, making induction heating suitable for both localized and bulk heating.
Key Points Explained:
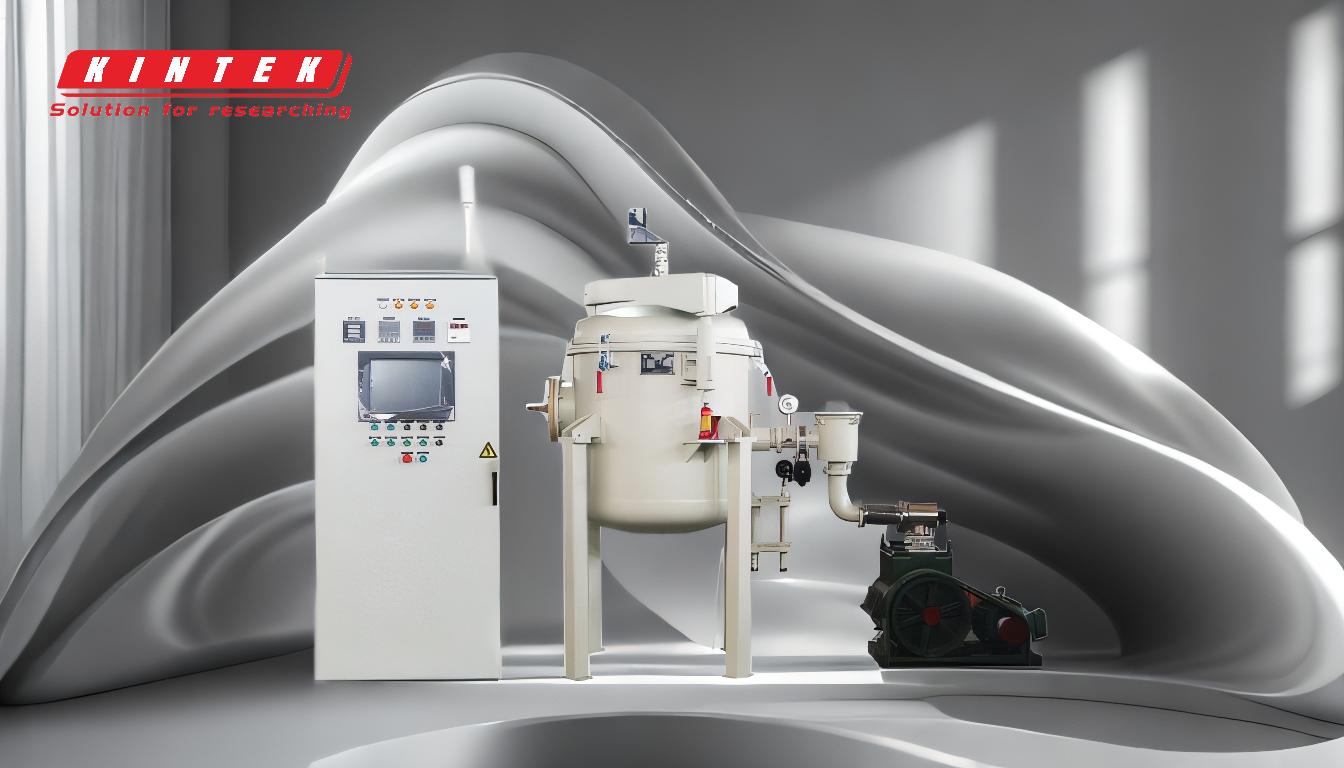
-
Temperature Range Based on Applications:
-
Low-Temperature Applications (100°C to 500°C):
- Used for processes like soldering, brazing, and plastic injection molding.
- Suitable for materials that require moderate heating without reaching melting points.
-
Medium-Temperature Applications (500°C to 1200°C):
- Common in heat treatment processes, such as hardening and tempering of metals.
- Used for applications like welding and surface heating.
-
High-Temperature Applications (1200°C to 2000°C+):
- Essential for melting metals, including refractory metals like tungsten and molybdenum.
- Used in specialized processes like Czochralski crystal growth and zone refining in the semiconductor industry.
-
Low-Temperature Applications (100°C to 500°C):
-
Factors Influencing Temperature Range:
-
Material Properties:
- The electrical resistivity and magnetic permeability of the material determine how efficiently it can be heated.
- Magnetic materials generate additional heat through hysteresis losses.
-
Induction Coil Design:
- The shape, size, and power of the induction coil influence the heating efficiency and temperature uniformity.
-
Frequency of Alternating Current:
- Higher frequencies are suitable for surface heating, while lower frequencies are better for deep heating of bulk materials.
-
Material Properties:
-
Control Mechanisms:
-
Current Adjustment:
- The strength of the applied current directly affects the temperature achieved.
- Precise control allows for localized heating and avoids overheating.
-
Cooling Systems:
- Water or air cooling is often used to manage the temperature of the induction coil and prevent damage.
-
Current Adjustment:
-
Specialized Applications:
-
Low-Resistivity Materials:
- Induction heating can be adapted for materials like aluminum and copper, which have low resistivity, by optimizing process parameters.
-
Medical Applications:
- Emerging uses include heating biological tissues for therapeutic purposes, requiring precise temperature control.
-
Low-Resistivity Materials:
-
Future Trends:
-
Advanced Materials and Energy Applications:
- Induction heating is expected to play a key role in developing engineered materials and alternative energy technologies.
-
Global Impact:
- Its efficiency and precision make it a valuable tool for empowering developing countries in industrial and technological advancements.
-
Advanced Materials and Energy Applications:
In summary, the temperature range for induction heating is highly adaptable, spanning from moderate to extremely high temperatures, depending on the application and material. Its ability to provide precise, localized, and efficient heating makes it indispensable across a wide range of industries.
Summary Table:
Temperature Range | Applications | Key Features |
---|---|---|
100°C to 500°C | Soldering, brazing, plastic molding | Moderate heating, avoids melting |
500°C to 1200°C | Heat treatment, welding, surface heating | Hardening, tempering metals |
1200°C to 2000°C+ | Melting refractory metals, semiconductor processes | High precision, extreme temperatures |
Factors Influencing Range | Material properties, coil design, current frequency | Efficient and uniform heating |
Discover how induction heating can revolutionize your processes—contact our experts today!