Magnetron sputtering is a highly versatile and efficient physical vapor deposition (PVD) technique used to create thin films on various substrates. It involves the ejection of atoms from a solid target material through bombardment by energetic ions, typically in a vacuum environment. This process is driven by a magnetic field, which enhances the efficiency of ion bombardment and allows for precise control over the deposition process. Magnetron sputtering is advantageous for its ability to work with a wide range of materials, including those with high melting points, and its capacity to produce uniform, high-quality films with excellent adhesion. The technique has evolved significantly since its early observations in the 1850s, becoming commercially viable in the 1970s with the introduction of magnetron sputtering, which addressed limitations of earlier methods like diode sputtering.
Key Points Explained:
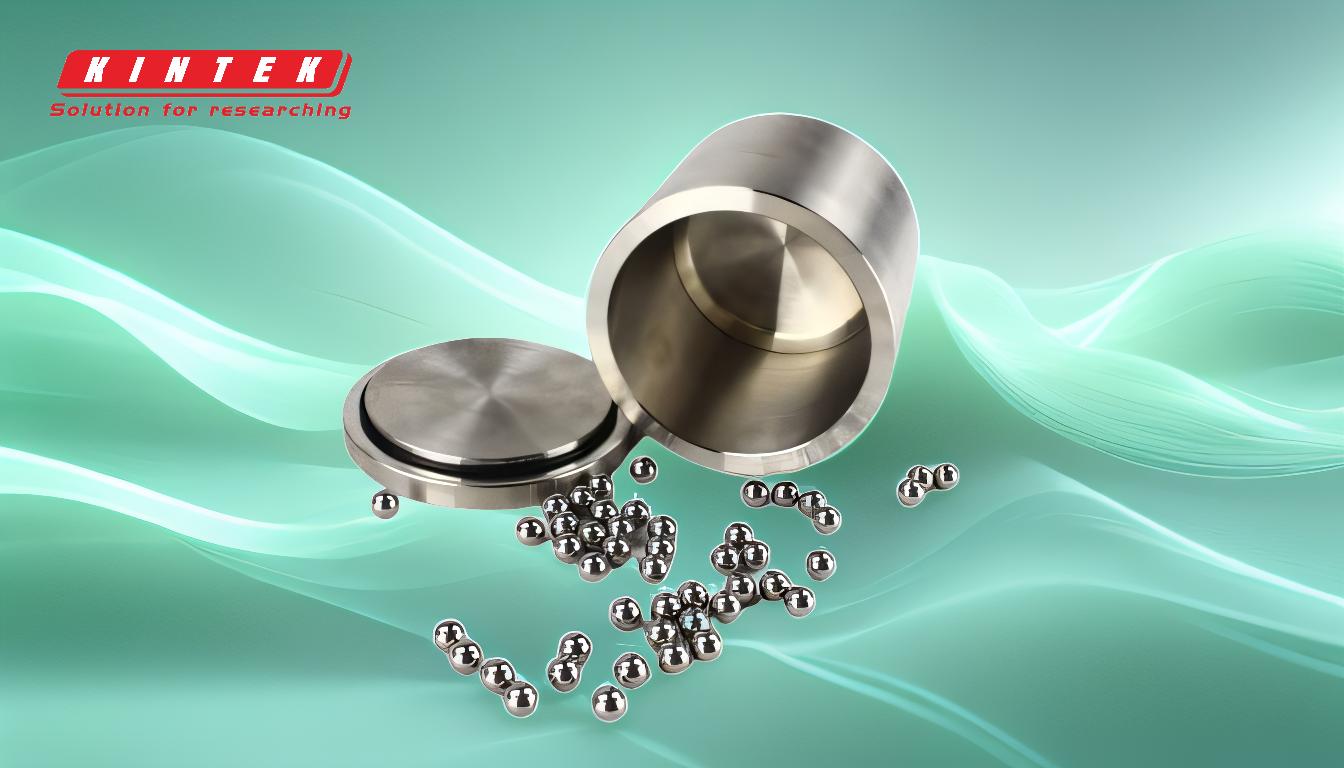
-
Basic Principle of Magnetron Sputtering:
- Magnetron sputtering involves the removal of atoms from a target material through bombardment by high-energy ions.
- A negative voltage (typically -300V or more) is applied to the target, attracting positively charged ions from the plasma.
- When these ions collide with the target surface, they transfer energy to the target atoms, causing them to be ejected (sputtered) from the surface.
-
Energy Transfer and Sputtering Mechanism:
- The energy transferred during ion bombardment must exceed the binding energy of the target atoms to cause sputtering.
- Primary recoil atoms are created when the energy transferred to a lattice site is greater than the binding energy.
- These recoil atoms can collide with other atoms, creating collision cascades that further distribute energy.
- A surface atom is sputtered if the energy transferred to it normal to the surface is greater than about three times the surface binding energy.
-
Materials Used in Magnetron Sputtering:
- Common target materials include magnetic materials like nickel and iron, as well as a variety of other metals, alloys, and compounds.
- The technique is particularly useful for materials with high melting points that are difficult to process using traditional thermal deposition methods.
-
Advantages of Magnetron Sputtering:
- Versatility: Can be used to deposit a wide range of materials, including exotic and high-melting-point materials.
- Precision: Offers excellent control over the deposition process, enabling the creation of thin films with precise thickness and composition.
- Adhesion: Produces films with excellent adhesion to the substrate.
- Uniformity: Capable of producing large-area, uniform, and dense films.
-
Historical Development:
- Sputtering was first observed in the 1850s but became commercially relevant in the 1940s with the development of diode sputtering.
- Diode sputtering had limitations such as low deposition rates and high costs.
- Magnetron sputtering was introduced in 1974 as an improved alternative, offering higher deposition rates and broader applications.
-
Applications and Industrial Relevance:
- Magnetron sputtering is widely used in industrial coating processes due to its low deposition temperature, fast deposition speed, and ability to produce high-quality films.
- It is employed in various industries, including electronics, optics, and materials science, for applications such as thin-film transistors, solar cells, and protective coatings.
-
Comparison with Other PVD Techniques:
- Unlike thermal evaporation, magnetron sputtering does not require the source material to be melted or evaporated, making it suitable for materials that are difficult to process using traditional methods.
- It offers better control over film properties and can produce films with superior adhesion and uniformity compared to other PVD techniques.
-
Challenges and Limitations:
- While magnetron sputtering offers many advantages, it can be challenging to achieve precise control over material placement, especially for complex geometries.
- The process requires a vacuum environment, which can increase equipment costs and complexity.
In summary, magnetron sputtering is a powerful and versatile technique for thin-film deposition, offering precise control, excellent film quality, and the ability to work with a wide range of materials. Its development has significantly advanced the field of surface engineering and thin-film technology, making it a cornerstone of modern industrial coating processes.
Summary Table:
Key Aspect | Details |
---|---|
Basic Principle | Ejection of atoms from a target via ion bombardment in a vacuum environment. |
Energy Transfer | Energy must exceed binding energy to sputter atoms, creating collision cascades. |
Materials Used | Magnetic materials (e.g., nickel, iron), metals, alloys, and high-melting-point compounds. |
Advantages | Versatility, precision, excellent adhesion, and uniform film production. |
Historical Development | Evolved from 1850s observations to commercial viability in the 1970s. |
Applications | Used in electronics, optics, and materials science for thin-film transistors, solar cells, and coatings. |
Challenges | Requires vacuum environment; complex geometries can be difficult to control. |
Unlock the potential of magnetron sputtering for your projects—contact our experts today!