Thermal deposition, specifically thermal evaporation deposition, is a physical vapor deposition (PVD) technique used to create thin films on substrates. It involves heating a solid material in a high vacuum chamber until it evaporates, forming a vapor that deposits onto a substrate as a thin film. This method is widely used in industries such as electronics, optics, and coatings due to its simplicity, cost-effectiveness, and ability to produce high-purity films. The process relies on precise control of temperature, vacuum conditions, and material properties to achieve uniform and high-quality coatings.
Key Points Explained:
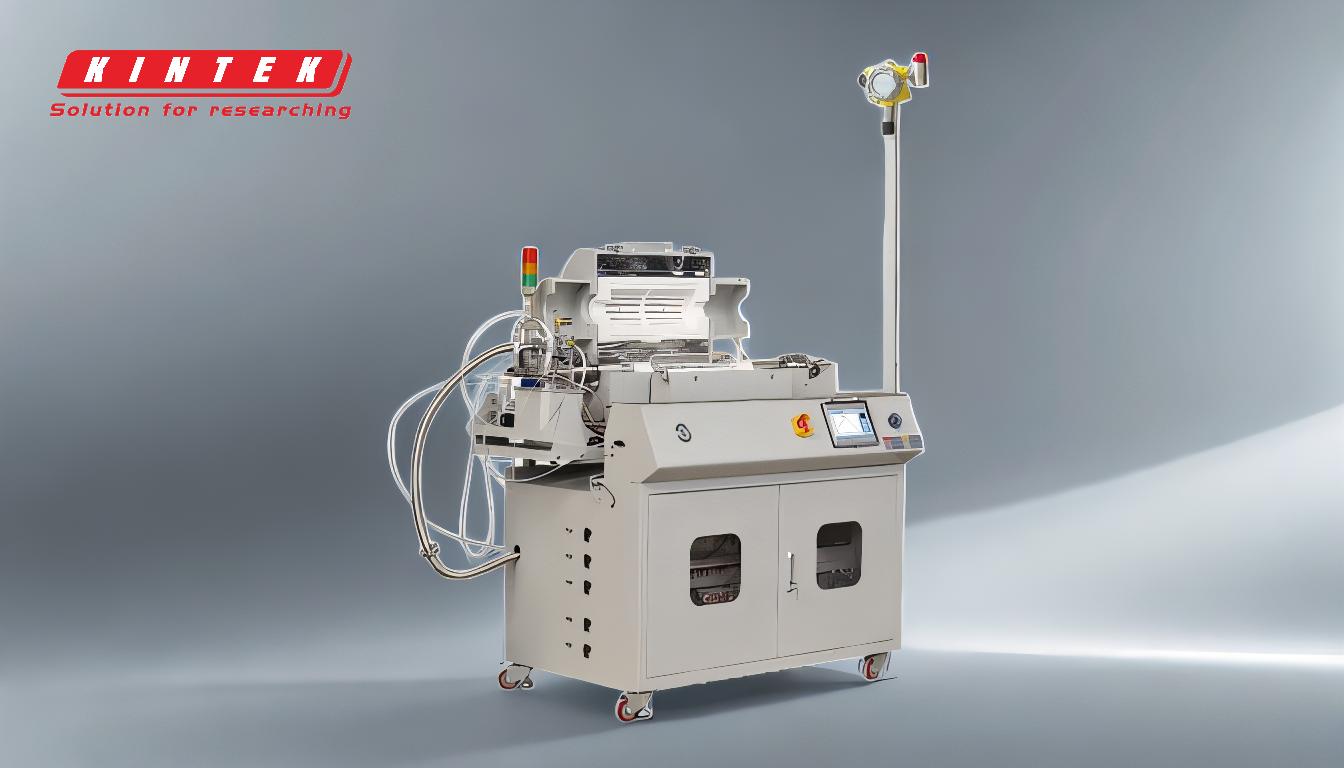
-
Definition and Process of Thermal Evaporation Deposition:
- Thermal evaporation deposition is a physical vapor deposition (PVD) method where a solid material is heated to its evaporation point in a high vacuum chamber.
- The material is typically heated using a resistive heating source, such as a tungsten boat or basket, which carries a high electric current to generate the required heat.
- As the material reaches its melting point, it evaporates and forms a vapor cloud within the chamber.
- The vapor stream travels through the vacuum and deposits onto a substrate, forming a thin film.
-
Key Components of the Thermal Evaporation System:
- Vacuum Chamber: A high vacuum environment is essential to minimize contamination and ensure the vapor stream travels unimpeded to the substrate.
- Heating Source: Resistive heating elements (e.g., tungsten boats or baskets) are commonly used to heat the material to its evaporation temperature.
- Substrate Holder: The substrate is placed on a holder within the chamber, positioned to receive the vapor stream evenly.
- Material Source: The solid material to be evaporated is placed in the heating source. Common materials include metals, alloys, and some organic compounds.
-
Advantages of Thermal Evaporation Deposition:
- High Purity Films: The vacuum environment and controlled heating process result in films with minimal impurities.
- Cost-Effectiveness: The equipment and process are relatively simple and inexpensive compared to other deposition methods.
- Versatility: Suitable for a wide range of materials, including metals, semiconductors, and dielectrics.
- Uniform Coatings: The process can produce highly uniform thin films, especially for flat or simple geometries.
-
Applications of Thermal Evaporation Deposition:
- Optical Coatings: Used to create anti-reflective, reflective, and protective coatings for lenses, mirrors, and other optical components.
- Electronics: Applied in the fabrication of thin-film transistors, solar cells, and sensors.
- Decorative Coatings: Utilized for creating metallic finishes on consumer products.
- Barrier Layers: Deposited as protective layers to prevent corrosion or oxidation in sensitive materials.
-
Limitations and Challenges:
- Material Compatibility: Not all materials can be evaporated without decomposition or damage, limiting the range of usable materials.
- Substrate Geometry: Achieving uniform coatings on complex or three-dimensional substrates can be challenging.
- Temperature Sensitivity: Some substrates may be sensitive to the heat generated during the process, requiring careful control.
- Deposition Rate: The rate of deposition can be slower compared to other PVD methods like sputtering.
-
Comparison with Other Deposition Methods:
- Sputtering: Unlike thermal evaporation, sputtering uses plasma or gaseous atoms to dislodge atoms from a target material, offering better control over film composition and adhesion.
- Chemical Vapor Deposition (CVD): CVD involves chemical reactions to deposit films, enabling the creation of more complex materials but requiring higher temperatures and more complex equipment.
- Electron Beam Evaporation: Similar to thermal evaporation but uses an electron beam to heat the material, allowing for higher evaporation temperatures and better control over the deposition process.
-
Operational Parameters:
- Vacuum Pressure: Typically maintained at 10^-5 to 10^-7 Torr to ensure a clean environment and efficient vapor transport.
- Temperature Range: The material is heated to temperatures between 250°C and 350°C, depending on its evaporation point.
- Deposition Rate: Controlled by adjusting the heating current and material properties, typically ranging from a few nanometers to micrometers per minute.
-
Future Trends and Innovations:
- Enhanced Control Systems: Advances in automation and real-time monitoring are improving the precision and reproducibility of thermal evaporation processes.
- Hybrid Techniques: Combining thermal evaporation with other methods, such as sputtering or CVD, to achieve multi-layered or composite films with enhanced properties.
- Nanostructured Films: Research is ongoing to use thermal evaporation for creating nanostructured films with unique optical, electrical, and mechanical properties.
In summary, thermal evaporation deposition is a versatile and widely used method for creating thin films with high purity and uniformity. While it has some limitations, its simplicity and cost-effectiveness make it a popular choice for various industrial and research applications.
Summary Table:
Aspect | Details |
---|---|
Process | Heating solid material in a vacuum chamber to create a thin film on a substrate. |
Key Components | Vacuum chamber, heating source, substrate holder, material source. |
Advantages | High purity, cost-effective, versatile, uniform coatings. |
Applications | Optical coatings, electronics, decorative coatings, barrier layers. |
Limitations | Material compatibility, substrate geometry, temperature sensitivity. |
Comparison with Methods | Sputtering, CVD, electron beam evaporation. |
Operational Parameters | Vacuum pressure: 10^-5 to 10^-7 Torr, temperature: 250°C–350°C. |
Discover how thermal evaporation deposition can enhance your projects—contact our experts today!