Thermal shock refers to the stress and potential damage that occurs in materials when they are subjected to rapid temperature changes. In the context of a quartz tube, thermal shock is particularly relevant because quartz, while highly resistant to thermal stress, can still crack or fail if exposed to extreme or sudden temperature fluctuations. Quartz tubes are commonly used in high-temperature applications such as in quartz tube furnaces, where they must withstand rapid heating and cooling cycles. Understanding the thermal shock resistance of quartz tubes is critical for ensuring their longevity and performance in industrial and laboratory settings.
Key Points Explained:
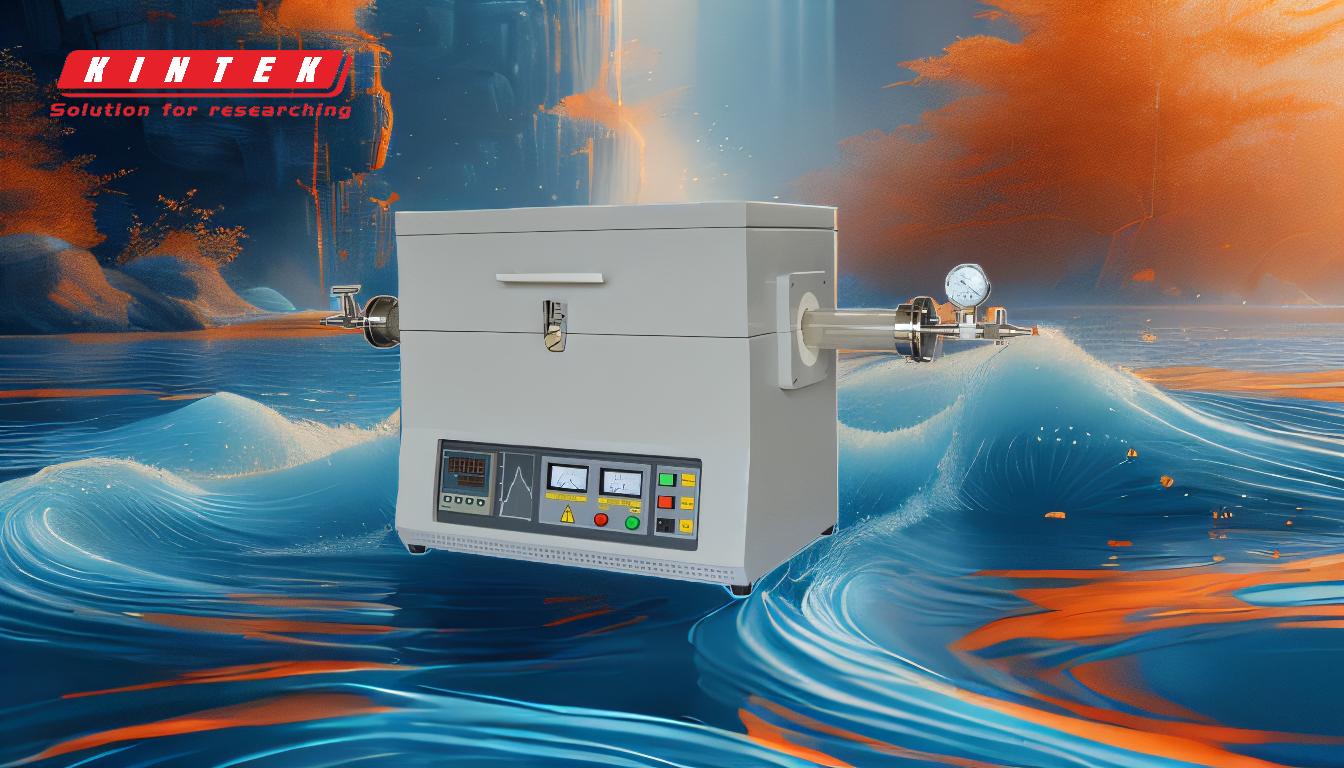
-
What is Thermal Shock?
- Thermal shock occurs when a material experiences a sudden change in temperature, leading to uneven expansion or contraction. This creates internal stresses that can cause cracking, warping, or complete failure of the material.
- For quartz tubes, thermal shock is a concern because they are often used in environments where they are rapidly heated or cooled, such as in furnaces or reactors.
-
Why Quartz Tubes are Susceptible to Thermal Shock
- Quartz has a low thermal expansion coefficient, which makes it more resistant to thermal stress compared to other materials like glass. However, it is not immune to thermal shock.
- Rapid temperature changes can cause localized stress concentrations, especially if the quartz tube has impurities, surface flaws, or uneven wall thickness. These imperfections act as stress points where cracks can initiate and propagate.
-
Factors Affecting Thermal Shock Resistance
- Material Purity: High-purity quartz tubes have better thermal shock resistance because impurities can weaken the material and create stress points.
- Wall Thickness: Thicker walls can help distribute thermal stress more evenly, reducing the risk of cracking. However, excessively thick walls may also retain heat unevenly, leading to stress.
- Heating and Cooling Rates: Gradual heating and cooling are less likely to cause thermal shock compared to rapid temperature changes.
- Surface Quality: Smooth, defect-free surfaces are less prone to cracking under thermal stress.
-
Applications in Quartz Tube Furnaces
- Quartz tubes are widely used in quartz tube furnaces for processes like annealing, sintering, and chemical vapor deposition. These applications often involve rapid temperature changes, making thermal shock resistance a critical factor.
- Proper design and operation of the furnace, including controlled heating and cooling rates, can minimize the risk of thermal shock.
-
Testing and Standards for Thermal Shock Resistance
- Thermal shock resistance is often tested by subjecting quartz tubes to rapid temperature changes and observing their performance. Standards such as ASTM C149 provide guidelines for testing thermal shock resistance in glass and ceramic materials.
- Manufacturers may also conduct in-house testing to ensure their quartz tubes meet specific application requirements.
-
Mitigating Thermal Shock in Quartz Tubes
- Gradual Temperature Changes: Avoid abrupt heating or cooling by using controlled ramp rates in furnace operations.
- Preheating: Preheating quartz tubes before exposing them to high temperatures can reduce thermal stress.
- Proper Handling: Handle quartz tubes carefully to avoid surface damage, which can exacerbate thermal shock.
- Quality Assurance: Use high-quality, defect-free quartz tubes from reputable suppliers.
-
Real-World Implications of Thermal Shock
- In industrial settings, thermal shock can lead to costly downtime and equipment damage if quartz tubes fail unexpectedly.
- Understanding and mitigating thermal shock is essential for optimizing the performance and lifespan of quartz tubes in high-temperature applications.
By considering these factors, users can make informed decisions when selecting and using quartz tubes, ensuring they are suitable for their specific thermal environments and applications.
Summary Table:
Key Factors | Details |
---|---|
Thermal Shock Definition | Stress caused by rapid temperature changes, leading to cracking or failure. |
Quartz Tube Susceptibility | Low thermal expansion but vulnerable to impurities and surface flaws. |
Resistance Factors | Material purity, wall thickness, heating/cooling rates, and surface quality. |
Applications | Used in quartz tube furnaces for annealing, sintering, and CVD processes. |
Mitigation Strategies | Gradual temperature changes, preheating, proper handling, and quality assurance. |
Ensure your quartz tubes withstand thermal shock—contact our experts today for tailored solutions!