Mold tooling refers to the process and components involved in creating a mold, which is used in manufacturing processes like injection molding. The tooling includes machining the mold from a block of metal, creating a core and cavity that form the negative shape of the part to be produced. The mold is then used in injection molding machines, where it is held together and injected with molten plastic at high pressure to form the final product. The tooling process is critical for ensuring the mold's precision, durability, and functionality in producing high-quality parts.
Key Points Explained:
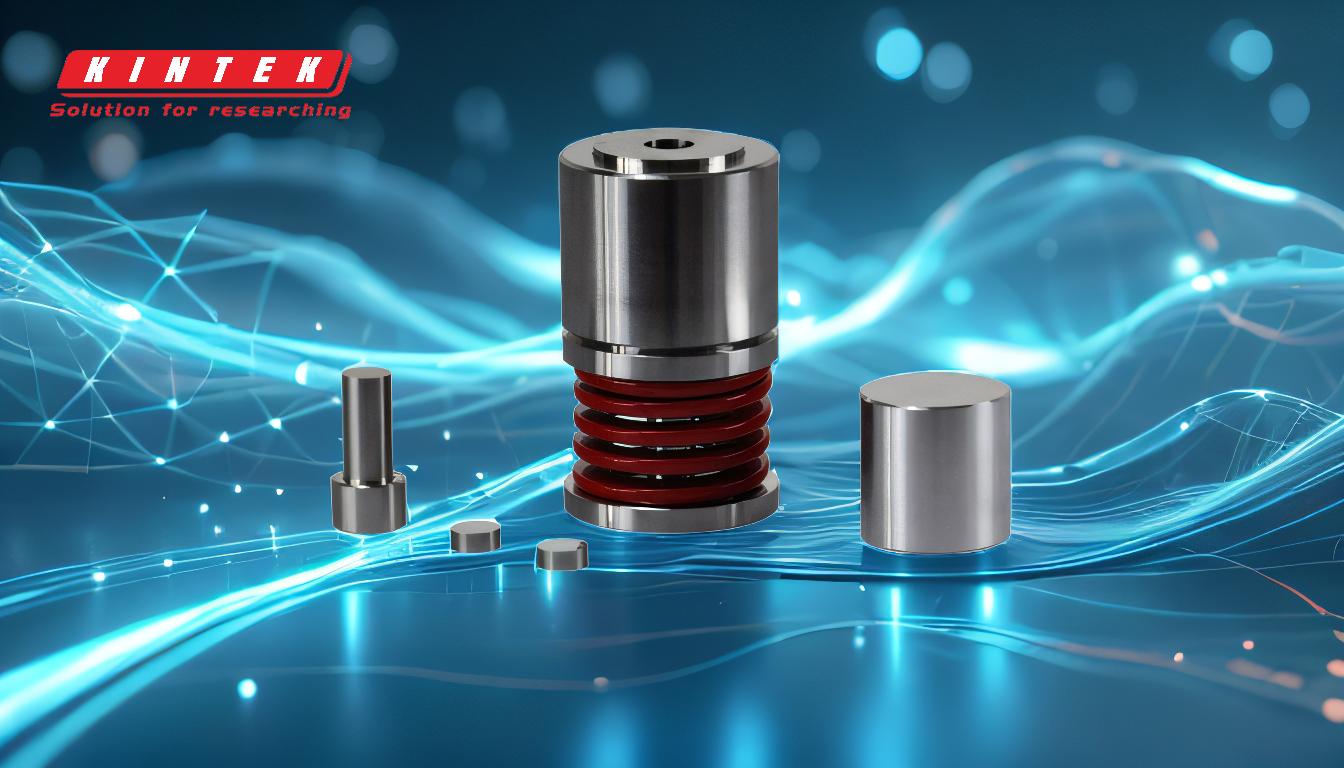
-
Definition of Mold Tooling
- Mold tooling refers to the process of designing, machining, and assembling the components of a mold.
- It involves creating the core and cavity, which are the negative shapes of the part to be manufactured.
- The tooling process ensures the mold is precise and capable of producing consistent, high-quality parts.
-
Machining the Mold
- The mold is typically machined from a block of metal, such as steel or aluminum, depending on the requirements of the production process.
- CNC (Computer Numerical Control) machining is often used to achieve high precision in creating the core and cavity.
- The machining process must account for factors like part geometry, material shrinkage, and ejection mechanisms.
-
Core and Cavity
- The core and cavity are the two main components of the mold that define the shape of the final product.
- The cavity forms the external surface of the part, while the core shapes the internal features.
- These components must be precisely aligned to ensure the part is formed correctly.
-
Injection Molding Process
- Once the mold is created, it is used in an injection molding machine.
- The mold is clamped together, and molten plastic is injected into the cavity at high pressure.
- The plastic cools and solidifies, taking the shape of the mold, after which the part is ejected.
-
Importance of Mold Tooling
- Proper mold tooling is essential for achieving consistent part quality, reducing defects, and minimizing production downtime.
- The durability of the mold depends on the quality of the tooling, as it must withstand high pressures and temperatures during the injection molding process.
- Tooling also impacts the cost and efficiency of production, as a well-designed mold can reduce cycle times and material waste.
-
Considerations for Mold Tooling
- Material selection: The choice of metal for the mold depends on factors like production volume, part complexity, and material being molded.
- Design for manufacturability: The mold design must account for factors like draft angles, wall thickness, and ejection mechanisms to ensure the part can be easily removed.
- Maintenance: Regular maintenance of the mold is necessary to extend its lifespan and ensure consistent part quality.
By understanding the intricacies of mold tooling, manufacturers can optimize their production processes, reduce costs, and improve the quality of their products.
Summary Table:
Key Aspect | Details |
---|---|
Definition | Process of designing, machining, and assembling mold components. |
Machining | CNC machining used for precision creation of core and cavity. |
Core and Cavity | Core shapes internal features; cavity forms external surfaces. |
Injection Molding | Molten plastic injected into mold at high pressure to form the final part. |
Importance | Ensures precision, durability, and consistent part quality. |
Considerations | Material selection, design for manufacturability, and regular maintenance. |
Optimize your production with expert mold tooling—contact us today!