The deposition rate is a critical parameter in processes like thin-film deposition, coating, and material synthesis, as it quantifies how quickly a material is deposited onto a substrate. The unit of deposition rate depends on the specific process and the method of measurement. Commonly, it is expressed in units such as nanometers per second (nm/s), micrometers per minute (µm/min), or angstroms per second (Å/s). These units indicate the thickness of the deposited material over time. Understanding the deposition rate is essential for controlling the quality, uniformity, and properties of the deposited layer, making it a key consideration in industries like semiconductor manufacturing, optics, and surface engineering.
Key Points Explained:
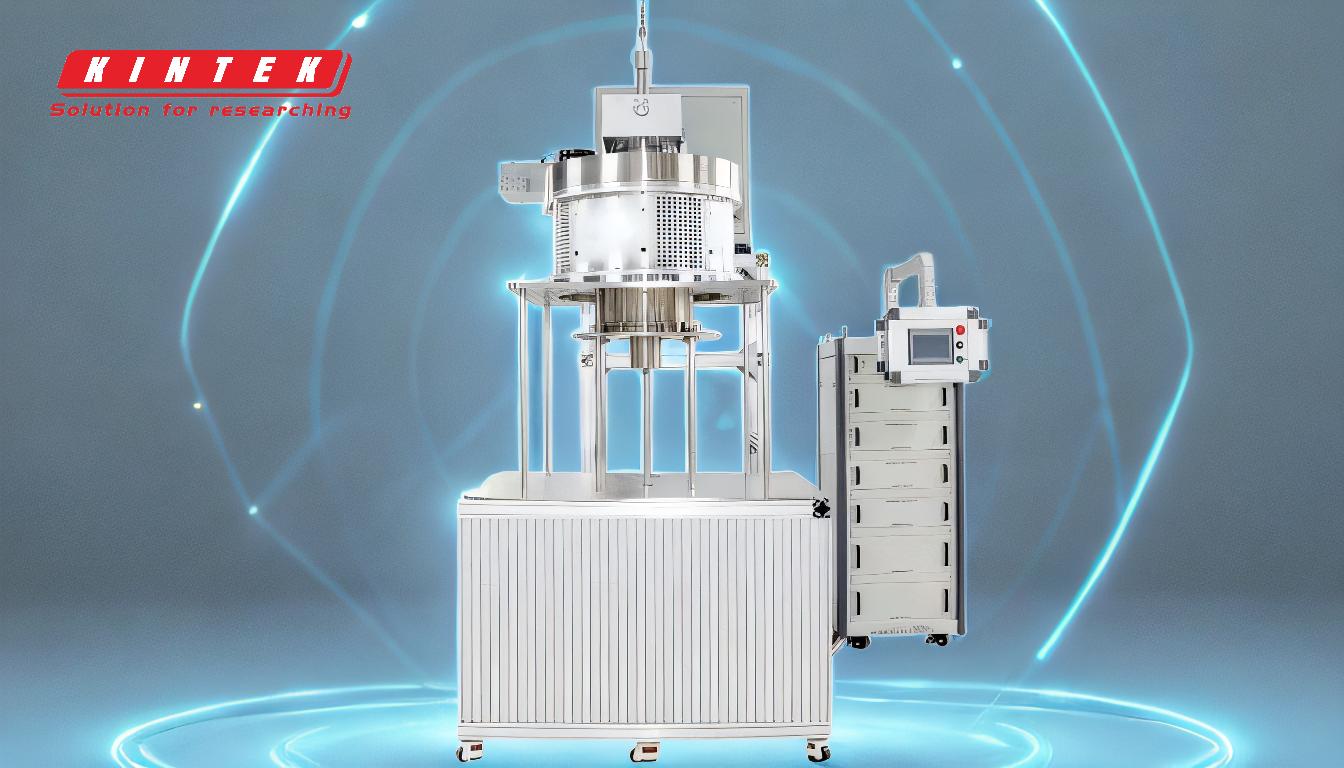
-
Definition of Deposition Rate:
- The deposition rate refers to the speed at which a material is deposited onto a substrate during processes like physical vapor deposition (PVD), chemical vapor deposition (CVD), or sputtering. It is a measure of how much material is added to the substrate per unit of time.
-
Common Units of Deposition Rate:
- The deposition rate is typically expressed in units of thickness over time. The most common units include:
- Nanometers per second (nm/s): Widely used in thin-film deposition processes, especially in semiconductor and optics industries.
- Micrometers per minute (µm/min): Often used in thicker coating applications or when the deposition process is slower.
- Angstroms per second (Å/s): Commonly used in high-precision applications, such as atomic layer deposition (ALD).
- The deposition rate is typically expressed in units of thickness over time. The most common units include:
-
Factors Influencing Deposition Rate:
- The deposition rate depends on several factors, including:
- Process parameters: Such as temperature, pressure, and power input in the deposition system.
- Material properties: The type of material being deposited and its vapor pressure or reactivity.
- Substrate conditions: Surface roughness, temperature, and preparation methods can affect the rate.
- Deposition technique: Different methods (e.g., sputtering, evaporation, CVD) have varying rates due to their unique mechanisms.
- The deposition rate depends on several factors, including:
-
Importance of Deposition Rate in Applications:
- Controlling the deposition rate is crucial for achieving desired material properties, such as:
- Thickness uniformity: Ensures consistent coating across the substrate.
- Material quality: Affects the microstructure, density, and adhesion of the deposited layer.
- Process efficiency: Optimizes production time and resource usage.
- Controlling the deposition rate is crucial for achieving desired material properties, such as:
-
Measurement Techniques:
- The deposition rate can be measured using various methods, such as:
- Quartz crystal microbalance (QCM): Measures mass changes to calculate the rate.
- Ellipsometry: Determines thickness optically.
- Profilometry: Measures step height changes after deposition.
- In-situ monitoring: Uses sensors to track deposition in real-time.
- The deposition rate can be measured using various methods, such as:
-
Practical Considerations for Equipment and Consumable Purchasers:
- When selecting deposition equipment or consumables, consider:
- Compatibility with desired deposition rate: Ensure the system can achieve the required rate for your application.
- Precision and control: Look for systems with accurate rate control and monitoring capabilities.
- Scalability: Choose equipment that can handle varying deposition rates for different production needs.
- When selecting deposition equipment or consumables, consider:
By understanding the unit of deposition rate and its implications, purchasers can make informed decisions when selecting equipment and consumables for their specific applications.
Summary Table:
Unit | Common Applications | Key Features |
---|---|---|
nm/s (nanometers per second) | Semiconductor and optics industries | High precision, ideal for thin-film deposition |
µm/min (micrometers per minute) | Thicker coatings, slower deposition processes | Suitable for applications requiring thicker layers |
Å/s (angstroms per second) | High-precision applications like atomic layer deposition (ALD) | Ultra-fine control, used in nanoscale material synthesis |
Need help selecting the right deposition equipment for your application? Contact our experts today!