Batch furnaces are specialized heating systems designed to process materials or components in discrete batches, making them ideal for applications requiring precise temperature control, flexibility, and adaptability to varying workloads. They are widely used in industries such as metallurgy, ceramics, research labs, and manufacturing for processes like annealing, sintering, tempering, curing, and heat treatment. Batch furnaces are particularly suited for low-volume production, large or complex parts, and processes requiring deep case carburizing or controlled atmospheres. Their ability to handle diverse materials and treatment requirements, combined with cost-effectiveness compared to continuous furnaces, makes them a versatile choice for industries requiring tailored heat treatment solutions.
Key Points Explained:
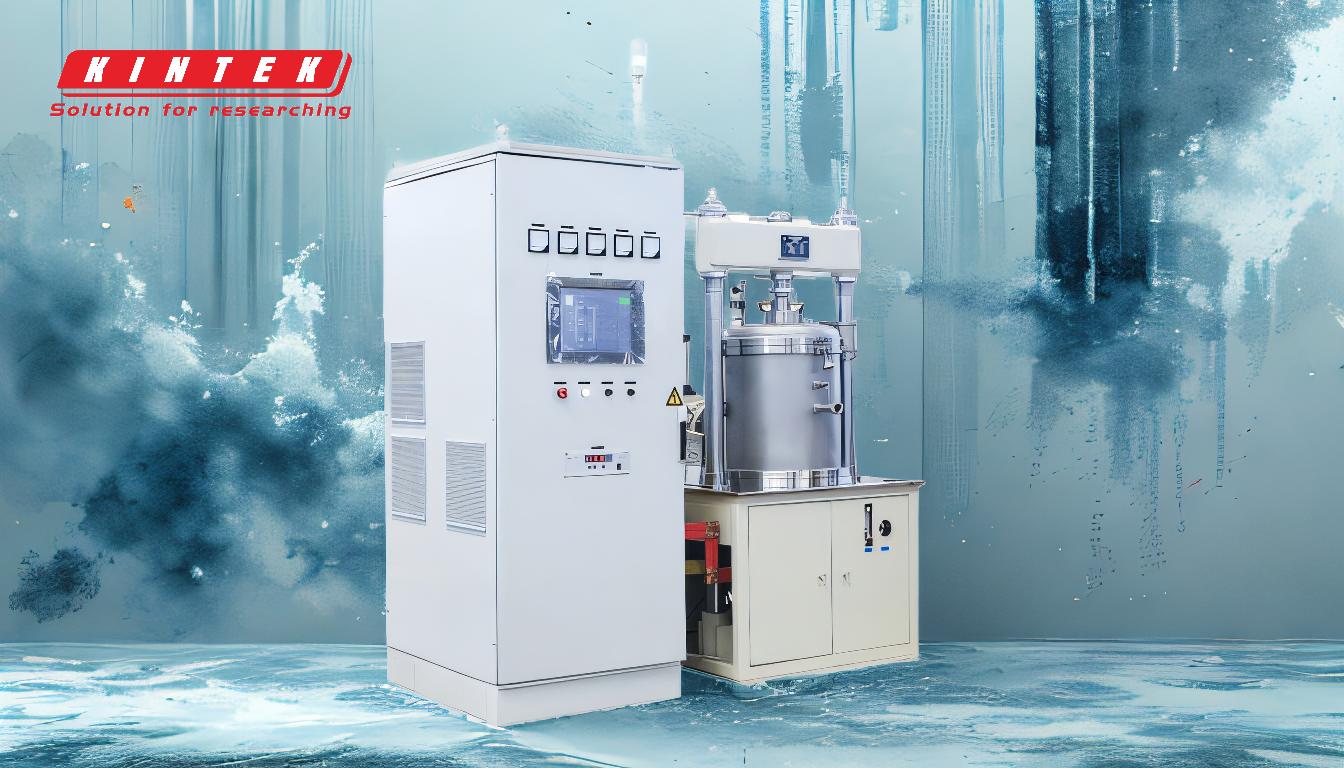
-
Definition and Operation of Batch Furnaces:
- Batch furnaces process materials or components in discrete batches, charging and discharging the workload as a single unit.
- They heat the batch from room temperature to a predetermined maximum temperature at a controlled rate, hold the temperature for a specified duration, and then cool the batch at a defined rate.
- This process allows for precise control over heating and cooling cycles, ensuring consistent results for each batch.
-
Key Applications of Batch Furnaces:
- Annealing: Softening metal components to improve ductility and reduce internal stresses, making them easier to machine or shape.
- Sintering: Bonding powdered materials into solid structures by heating them below their melting point, commonly used in powder metallurgy and ceramics.
- Tempering: Strengthening metal components by reheating and cooling them to achieve desired hardness and toughness.
- Curing and Baking: Polymer curing, polyimide baking, and solvent removal in materials like coatings, adhesives, and composites.
- Heat Treatment: Processes like hardening, case carburizing, and quenching to alter the mechanical properties of metals.
- Specialized Processes: Binder burnout, glass melting, high-temperature testing of ceramics, and metal joining.
-
Advantages of Batch Furnaces:
- Flexibility: Can handle a wide range of materials, part sizes, and heat treatment requirements, making them suitable for low-volume or custom production.
- Controlled Atmosphere: Can operate with or without controlled atmospheres (e.g., inert gases or vacuum) to prevent oxidation or achieve specific material properties.
- Cost-Effectiveness: Generally less expensive than continuous furnaces, making them ideal for small-scale or specialized operations.
- Adaptability: Suitable for large or complex parts that are difficult to process in continuous furnaces.
-
Industries and Use Cases:
- Metallurgy: Used for annealing, tempering, and heat treatment of steel and other alloys.
- Ceramics and Glass: Applied in sintering, firing, and glass melting processes.
- Research and Development: Ideal for laboratory work, including thermal testing, material research, and prototype development.
- Manufacturing: Used for curing coatings, drying components, and processing polymers or composites.
-
Comparison with Continuous Furnaces:
- Batch furnaces are better suited for low-volume production or specialized applications, while continuous furnaces are designed for high-volume, uniform processing.
- Batch furnaces offer greater flexibility in handling diverse workloads and complex geometries, whereas continuous furnaces are optimized for consistent, high-throughput operations.
-
Technical Considerations:
- Temperature Control: Precise temperature regulation is critical for achieving desired material properties and process outcomes.
- Atmosphere Control: Inert or controlled atmospheres may be required to prevent oxidation or contamination during heat treatment.
- Cooling Rates: Controlled cooling is essential for processes like quenching or tempering to achieve specific mechanical properties.
In summary, batch furnaces are indispensable tools in industries requiring precise, flexible, and cost-effective heat treatment solutions. Their ability to handle diverse materials, complex geometries, and specialized processes makes them a versatile choice for applications ranging from metallurgy to advanced material research.
Summary Table:
Aspect | Details |
---|---|
Definition | Specialized heating systems for processing materials in discrete batches. |
Key Applications | Annealing, sintering, tempering, curing, heat treatment, and more. |
Advantages | Flexibility, controlled atmosphere, cost-effectiveness, adaptability. |
Industries | Metallurgy, ceramics, research labs, manufacturing. |
Comparison | Better for low-volume or specialized tasks vs. continuous furnaces. |
Technical Considerations | Precise temperature control, atmosphere control, and cooling rates. |
Ready to enhance your heat treatment processes? Contact us today to find the perfect batch furnace for your needs!