Electric muffle furnaces are versatile tools widely used in industrial, laboratory, and research settings for high-temperature processes. They are designed to provide precise and controlled heating environments, making them essential for applications such as heat treatment of metals, glass melting, ceramics production, soldering, brazing, and environmental analysis. These furnaces can operate at extremely high temperatures, often up to 1,800°C, thanks to advanced materials like molybdenum disilicide. Their ability to maintain consistent temperatures in controlled atmospheres makes them indispensable for processes like annealing, calcination, sintering, and ash determination. Additionally, they are used in research for analyzing non-combustible and non-volatile components of samples, as well as for pre-treatment of medical and organic samples.
Key Points Explained:
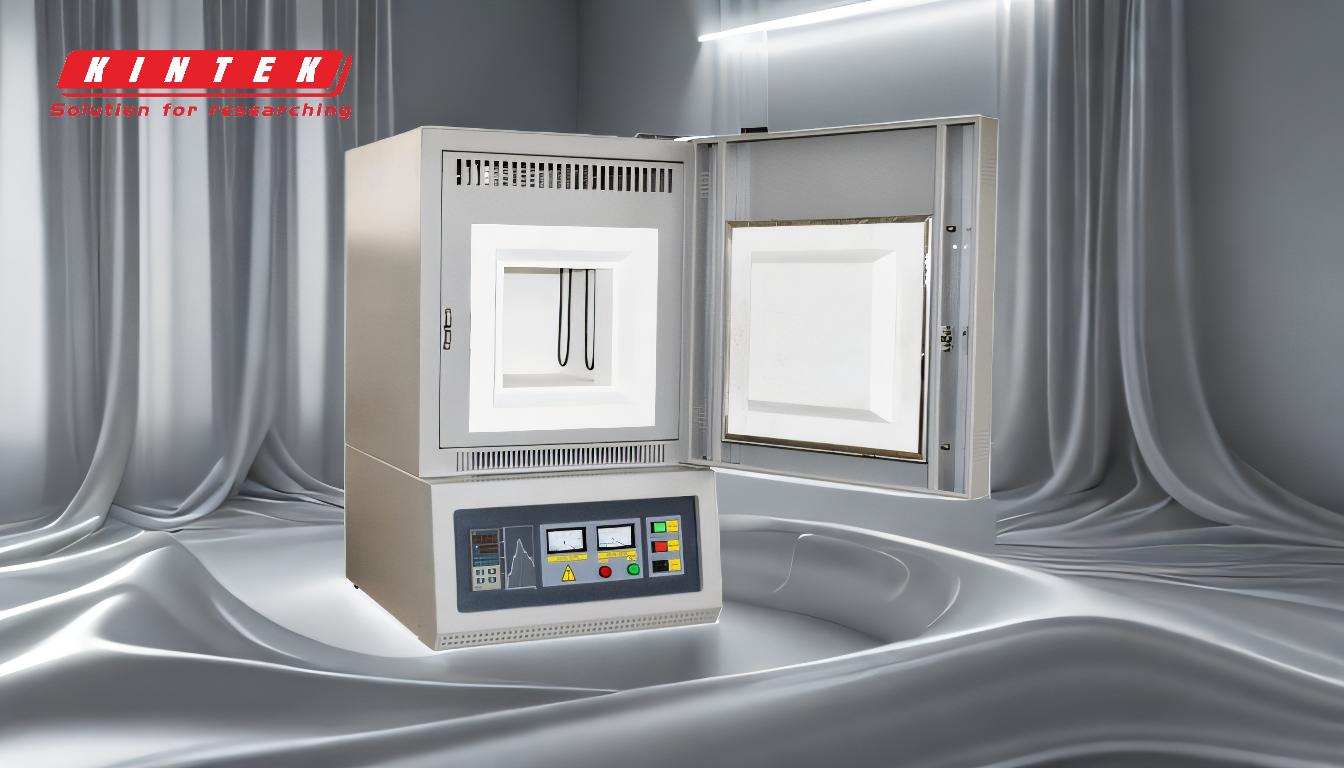
-
High-Temperature Applications:
- Electric muffle furnaces are capable of reaching temperatures as high as 1,800°C, making them suitable for processes that require extreme heat.
- Common high-temperature applications include:
- Melting glass: Used in glass manufacturing and art.
- Creating enamel coatings: Applied in metal finishing and decorative arts.
- Soldering and brazing: Essential in metallurgical joining processes.
- Technical ceramics: Used in the production of advanced ceramic materials.
-
Heat Treatment of Materials:
- Muffle furnaces are widely used for heat treatment processes such as:
- Annealing: Softening materials to improve ductility and reduce internal stresses.
- Hardening: Increasing the hardness and strength of metals.
- Stress relief: Reducing residual stresses in materials after fabrication.
- Quenching: Rapid cooling of materials to achieve specific mechanical properties.
- Muffle furnaces are widely used for heat treatment processes such as:
-
Laboratory and Research Applications:
- In laboratories, muffle furnaces are used for:
- Ash determination: Measuring the non-combustible content of samples.
- Thermogravimetric analysis: Studying the thermal stability of materials.
- Pre-treatment of medical and organic samples: Preparing samples for further analysis.
- Environmental analysis: Testing materials for compliance with environmental standards.
- In laboratories, muffle furnaces are used for:
-
Controlled Atmosphere Processing:
- Muffle furnaces can operate in both air and controlled atmospheres, which is crucial for processes like:
- Sintering: Bonding particles together at high temperatures without melting.
- Calcination: Heating materials to drive off volatile components.
- Brazing: Joining metals using a filler material in a controlled environment.
- Muffle furnaces can operate in both air and controlled atmospheres, which is crucial for processes like:
-
Versatility in Industrial Applications:
- Electric muffle furnaces are used across various industries, including:
- Chemical industry: For synthesis and analysis of chemical compounds.
- Metallurgical industry: For heat treatment and joining of metals.
- Ceramics industry: For firing and sintering ceramic materials.
- Pharmaceutical industry: For drug testing and sample preparation.
- Electric muffle furnaces are used across various industries, including:
-
Advanced Materials and Technology:
- The use of advanced materials like molybdenum disilicide allows muffle furnaces to achieve higher temperatures and improved performance.
- These materials enhance the furnace's durability and efficiency, enabling more sophisticated applications in metallurgy and materials science.
-
Environmental and Quality Control:
- Muffle furnaces play a critical role in environmental testing and quality control by:
- Analyzing the non-combustible and non-volatile content of materials.
- Ensuring compliance with environmental regulations.
- Providing precise and repeatable results for research and industrial processes.
- Muffle furnaces play a critical role in environmental testing and quality control by:
-
Customization and Flexibility:
- Muffle furnaces can be customized to meet specific application requirements, such as:
- Different chamber sizes and shapes.
- Various temperature ranges and heating rates.
- Integration with automation systems for enhanced control and efficiency.
- Muffle furnaces can be customized to meet specific application requirements, such as:
In summary, electric muffle furnaces are indispensable tools in both industrial and laboratory settings due to their ability to provide precise, high-temperature environments for a wide range of applications. Their versatility, advanced materials, and controlled atmosphere capabilities make them essential for processes ranging from heat treatment and material synthesis to environmental analysis and quality control.
Summary Table:
Application | Details |
---|---|
High-Temperature Processes | Glass melting, enamel coatings, soldering, brazing, technical ceramics. |
Heat Treatment | Annealing, hardening, stress relief, quenching. |
Laboratory Research | Ash determination, thermogravimetric analysis, sample pre-treatment. |
Controlled Atmosphere | Sintering, calcination, brazing in controlled environments. |
Industrial Uses | Chemical, metallurgical, ceramics, and pharmaceutical industries. |
Advanced Materials | Molybdenum disilicide for high temperatures and durability. |
Environmental Testing | Compliance analysis, non-combustible content measurement. |
Customization | Chamber sizes, temperature ranges, automation integration. |
Ready to enhance your industrial or lab processes with a muffle furnace? Contact us today for expert guidance!