A hydrogen furnace, specifically a hydrogen atmosphere furnace, is a specialized piece of equipment designed for high-temperature processes in controlled environments. It is widely used in industries such as ceramics, metallurgy, electronics, and semiconductors for applications like sintering, annealing, brazing, and purification. The furnace's ability to operate in a hydrogen-rich atmosphere makes it ideal for processes requiring reducing conditions, preventing oxidation, and ensuring material purity. Its versatility extends to research and industrial settings, where it supports advanced material development and high-temperature experiments.
Key Points Explained:
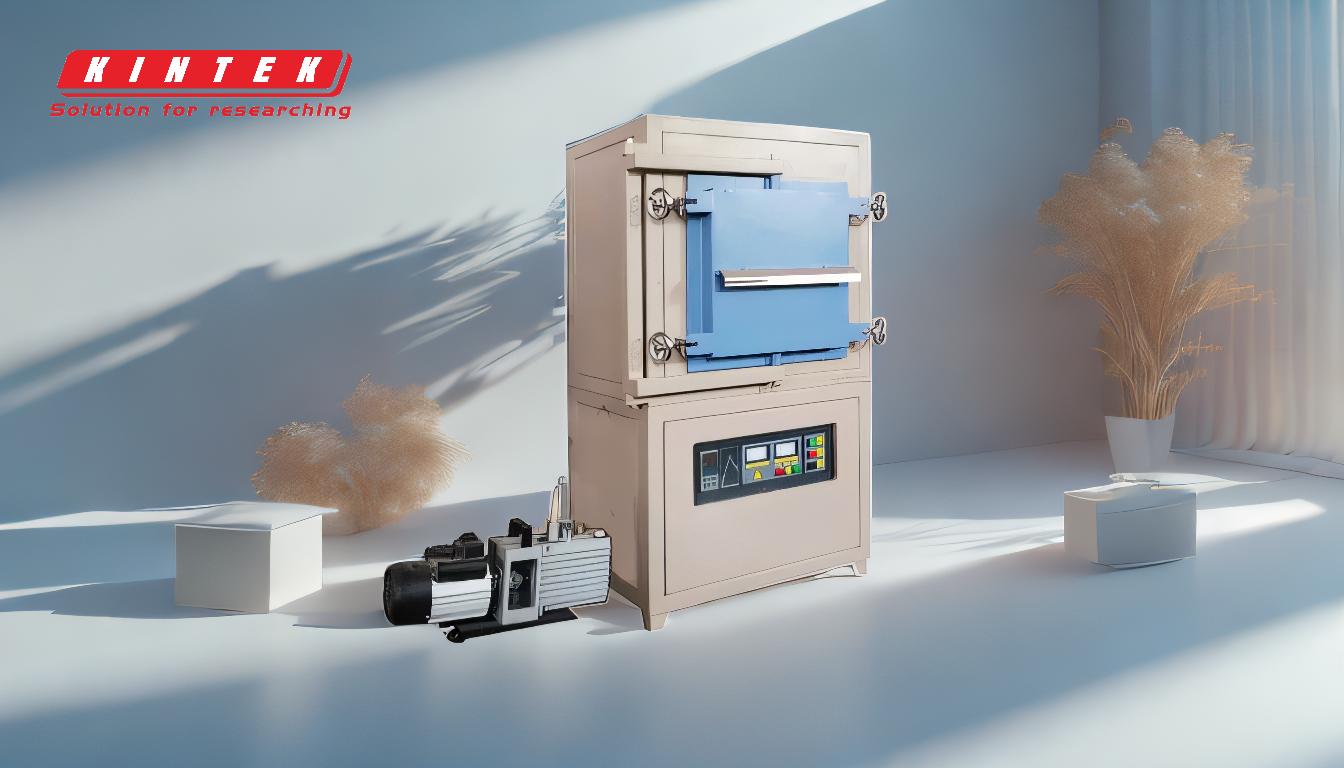
-
Primary Applications of a Hydrogen Furnace:
- Ceramic Sintering: The furnace is used to sinter ceramic materials, ensuring they achieve the desired density and strength. The hydrogen atmosphere prevents oxidation, which is critical for maintaining the material's properties.
- Metallization: Hydrogen furnaces are employed in metallization processes, where metal coatings are applied to ceramics or other substrates. The reducing environment ensures proper bonding and surface quality.
- Brazing: In brazing, the furnace creates a controlled atmosphere to join metals without oxidation, resulting in strong, clean joints.
- Annealing of Glass and Metal Parts: The furnace is used for annealing glass parts, particularly for sealing applications with metal components. The hydrogen atmosphere prevents contamination and ensures a clean seal.
- Purification: Hydrogen furnaces are ideal for purifying materials, as the reducing environment removes oxides and other impurities.
- Sintering Powder Metallurgy: The furnace is used to sinter powdered metals into solid components, ensuring high density and mechanical strength.
- Semiconductor Alloy Processing: In the semiconductor industry, the furnace is used for alloying and heat treatment processes, where precise control of the atmosphere is critical.
-
Industries and Fields of Use:
- Ceramics: For sintering and firing ceramic components.
- Metallurgy: For sintering, annealing, and brazing of metal parts.
- Electronics: For semiconductor processing and metallization.
- Glass: For annealing and sealing applications.
- Chemical Industry: For material purification and high-temperature reactions.
- Research and Academia: Universities and research institutes use hydrogen furnaces for high-temperature experiments and material development.
- Industrial and Mining Enterprises: For processing refractory materials, special alloys, and advanced ceramics.
-
Advantages of a Hydrogen Atmosphere:
- Oxidation Prevention: Hydrogen acts as a reducing agent, preventing oxidation of materials during high-temperature processes.
- Material Purity: The reducing environment ensures that materials remain free from contaminants, which is critical for high-performance applications.
- Versatility: The furnace can handle a wide range of materials and processes, making it a valuable tool in multiple industries.
-
Specific Processes Enabled by Hydrogen Furnaces:
- Powder Roasting: Used for processing powdered materials into dense, high-strength components.
- High-Temperature Experiments: Supports advanced research in material science and engineering.
- Ceramic Glue Discharge: Ensures proper curing and bonding of ceramic adhesives.
- Flue Gas Treatment: Used in environmental applications to process and neutralize harmful gases.
-
Key Features of Hydrogen Furnaces:
- Temperature Control: Precise temperature regulation ensures consistent results across various processes.
- Atmosphere Control: The ability to maintain a pure hydrogen environment is critical for achieving desired material properties.
- Durability and Reliability: Designed to withstand high temperatures and harsh conditions, hydrogen furnaces are built for long-term industrial use.
In summary, a hydrogen atmosphere furnace is a versatile and essential tool for high-temperature processes in numerous industries. Its ability to operate in a reducing environment makes it indispensable for applications requiring material purity, oxidation prevention, and precise control over thermal processes. Whether in industrial settings or research laboratories, hydrogen furnaces play a critical role in advancing material science and manufacturing technologies.
Summary Table:
Applications | Industries | Advantages |
---|---|---|
Ceramic Sintering | Ceramics, Metallurgy | Oxidation Prevention |
Metallization | Electronics, Semiconductors | Material Purity |
Brazing | Glass, Chemical Industry | Versatility |
Annealing | Research & Academia | Precise Temperature Control |
Purification | Industrial & Mining | Durability and Reliability |
Interested in how a hydrogen furnace can enhance your processes? Contact us today to learn more!