RF sputtering is a specialized technique used primarily for depositing thin films of materials onto substrates, particularly in applications requiring high precision and quality. It is especially advantageous for insulating materials and is widely used in industries such as optics, electronics, and materials science. RF sputtering enables the creation of high-quality, homogeneous thin films at relatively low substrate temperatures, making it suitable for fabricating optical planar waveguides, photonic microcavities, and advanced coatings for semiconductors and other high-tech applications.
Key Points Explained:
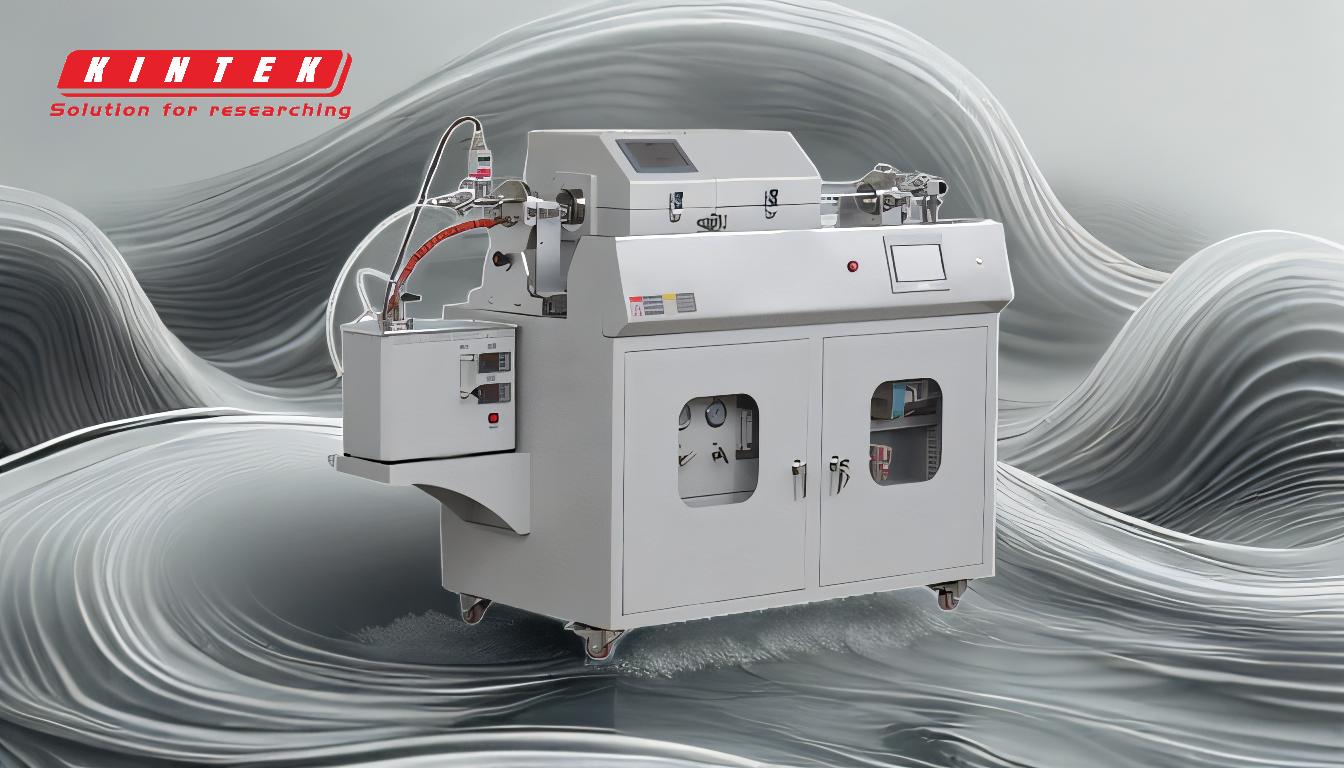
-
What is RF Sputtering?
- RF sputtering is a thin-film deposition technique that uses radio frequency (RF) energy to generate plasma in a vacuum chamber. This plasma dislodges atoms from a target material, which then deposit onto a substrate to form a thin film.
- It is particularly effective for depositing insulating materials, as the alternating electric field prevents charge buildup on the target surface, which can occur in DC sputtering.
-
Primary Applications of RF Sputtering
-
Optical and Photonic Devices:
- RF sputtering is widely used to fabricate optical planar waveguides and photonic microcavities, which are essential components in devices operating in the visible and near-infrared (NIR) regions.
- It is ideal for creating dielectric microcavities and depositing alternating layers of materials with controlled refractive indices and thicknesses, enabling the fabrication of high-quality 1-D photonic crystals.
-
Semiconductor and Electronics Industry:
- RF sputtering is used to deposit thin films of semiconductors, resistors, and dielectrics, which are critical for integrated circuit processing and the production of advanced electronic components.
- It is also employed in creating thin-film resistors, such as those made from reactive tantalum nitride, and modifying the properties of metallic nanofilms.
-
Optical Coatings:
- The technique is used to deposit anti-reflective or high-emissivity coatings on glass, which are essential for applications like energy-efficient windows and optical lenses.
-
Data Storage:
- RF sputtering plays a role in the production of computer hard disks, CDs, and DVDs, where precise thin-film coatings are required for data storage and retrieval.
-
Optical and Photonic Devices:
-
Advantages of RF Sputtering
-
Low Substrate Temperature:
- RF sputtering allows for the deposition of high-quality films at relatively low substrate temperatures, making it suitable for temperature-sensitive materials and applications.
-
High-Quality Films:
- The technique produces homogeneous and defect-free thin films with precise control over thickness and composition.
-
Versatility:
- RF sputtering can be used with a wide range of materials, including insulators, semiconductors, and metals, making it a versatile tool in materials science and engineering.
-
Precision and Control:
- It enables the deposition of alternating layers of different materials with controlled properties, such as refractive index and thickness, which is critical for advanced optical and electronic devices.
-
Low Substrate Temperature:
-
Industrial and Research Applications
-
Advanced Materials Development:
- RF sputtering is a key technique for developing advanced materials and coatings, enabling the creation of smaller, lighter, and more durable products.
-
Surface Physics and Analysis:
- In surface physics, RF sputtering is used as a cleaning method to prepare high-purity surfaces and as a tool for analyzing the chemical composition of surfaces.
-
Alloy Deposition:
- The technique can deposit thin layers of alloys in a single run, simplifying the fabrication process for complex materials.
-
Advanced Materials Development:
-
Historical and Technical Significance
- RF sputtering was first demonstrated in 1966 for depositing SiO2 films on silicon substrates, showcasing its potential for insulating materials.
- Its ability to handle insulating targets without charge buildup has made it a cornerstone technique in thin-film deposition for both industrial and research applications.
-
Comparison with Other Sputtering Techniques
- Unlike DC sputtering, which is limited to conductive materials, RF sputtering can effectively deposit insulating materials due to its use of an alternating electric field.
- RF sputtering offers better control over film properties compared to other deposition methods, such as evaporation or chemical vapor deposition (CVD), especially for applications requiring high precision and uniformity.
In summary, RF sputtering is a critical technique in modern materials science and engineering, offering unmatched precision, versatility, and quality in thin-film deposition. Its applications span from advanced optical and photonic devices to semiconductor manufacturing and data storage, making it an indispensable tool for researchers and engineers across various industries.
Summary Table:
Aspect | Details |
---|---|
Definition | Thin-film deposition technique using RF energy to generate plasma. |
Key Applications | Optical waveguides, photonic devices, semiconductors, optical coatings. |
Advantages | Low substrate temperature, high-quality films, versatility, precision. |
Industries | Optics, electronics, materials science, data storage. |
Comparison | Superior to DC sputtering for insulating materials; better precision than CVD. |
Unlock the potential of RF sputtering for your projects—contact our experts today!