Vacuum heat treatment is a specialized process used to harden and improve the properties of metal workpieces by heating them in a vacuum or protective gas environment. This method prevents oxidation and contamination, ensuring superior results compared to traditional heat treatment methods. The process involves heating the workpiece to a precise temperature, maintaining it at that temperature for a specific duration (soak time), and then cooling it at controlled rates using various media like oil, polymer, or air. The vacuum environment eliminates the need for post-treatment cleaning and reduces the risk of cracking, making it ideal for high-alloy tool steels and other materials requiring precise control over microstructure and mechanical properties.
Key Points Explained:
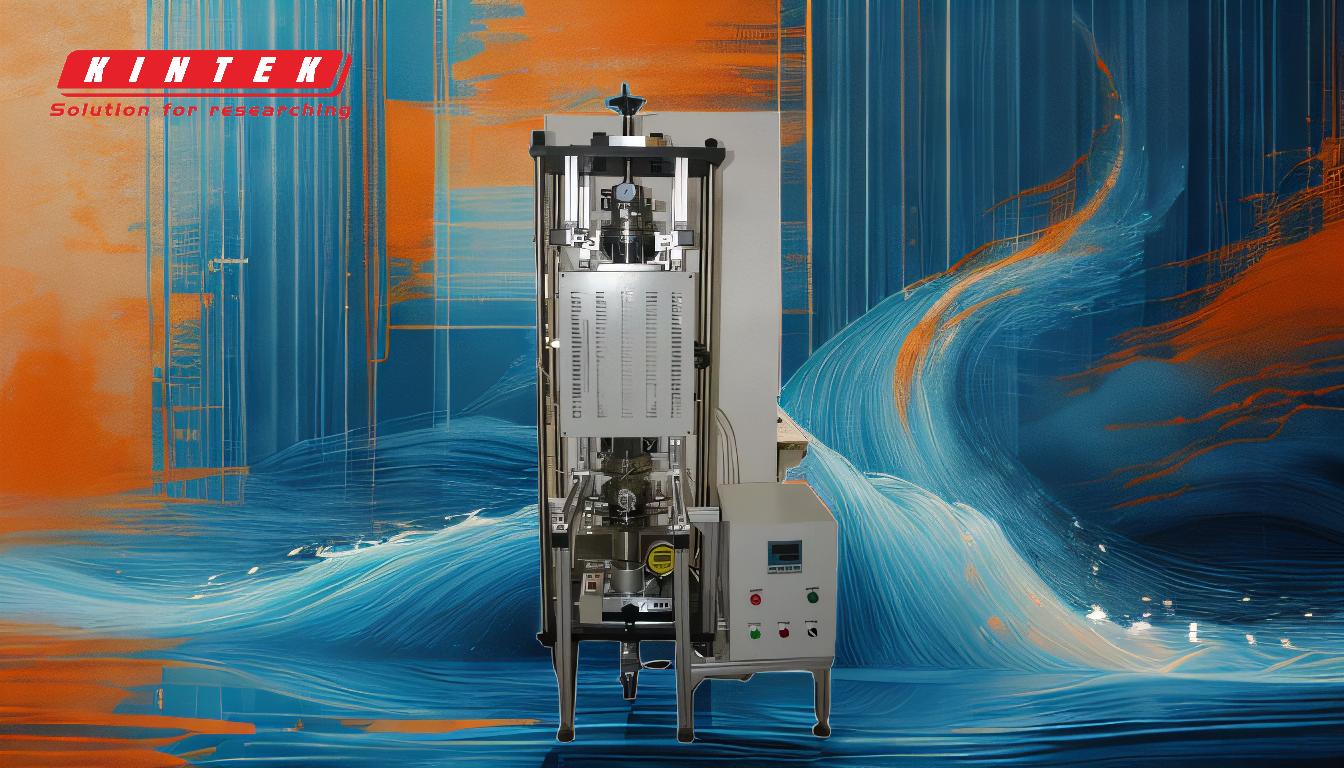
-
Vacuum Environment:
- A vacuum chamber is used to create an environment with minimal air or oxygen, preventing oxidation and contamination of the workpiece.
- A vacuum pumping system removes air from the sealed chamber, ensuring no air leaks during the process.
- This unreactive environment is critical for achieving consistent and high-quality results.
-
Heating Process:
- The workpiece is heated to a suitable temperature, typically ranging from 1,316°C (2,400°F) or higher, depending on the material and desired outcome.
- Heating is achieved using resistance or induction methods, ensuring uniform temperature distribution.
- The temperature is controlled and monitored using computer systems to ensure repeatability and precision.
-
Soak Time:
- After reaching the target temperature, the workpiece is held at that temperature for a specific duration, known as the soak time.
- The soak time varies depending on the material, workpiece size, and desired microstructure changes.
- This step ensures that the material's internal structure is uniformly transformed.
-
Cooling Process:
- After the soak time, the workpiece is cooled at controlled rates using different cooling media, such as oil, polymer, or air.
- The cooling rate is critical for achieving the desired mechanical properties, such as hardness, toughness, and durability.
- The vacuum environment minimizes thermal stress, reducing the risk of cracking or distortion during cooling.
-
Benefits of Vacuum Heat Treatment:
- Oxidation Prevention: The vacuum environment eliminates oxidation, preserving the workpiece's surface quality.
- Contamination-Free: No exposure to external gases or impurities ensures a clean and uniform finish.
- Reduced Cracking: Controlled heating and cooling rates minimize thermal stress, reducing the likelihood of cracking.
- No Post-Treatment Cleaning: The absence of oxidation and contamination eliminates the need for additional cleaning steps.
- Enhanced Performance: The process improves the material's microstructure, leading to better mechanical properties and longer service life.
-
Applications:
- Vacuum heat treatment is commonly used for high-alloy tool steels, aerospace components, and precision engineering parts.
- It is suitable for processes like annealing, brazing, sintering, and hardening, where precise control over material properties is essential.
-
Computer Control:
- The entire process is computer-controlled, ensuring precise temperature regulation, uniform heating, and repeatable results.
- This automation enhances process reliability and reduces the risk of human error.
By following this structured approach, vacuum heat treatment delivers consistent, high-quality results, making it a preferred method for industries requiring superior material performance and durability.
Summary Table:
Key Aspect | Details |
---|---|
Vacuum Environment | Prevents oxidation and contamination for clean, high-quality results. |
Heating Process | Controlled heating up to 1,316°C (2,400°F) for uniform temperature. |
Soak Time | Ensures uniform transformation of the material's internal structure. |
Cooling Process | Controlled cooling rates using oil, polymer, or air to minimize cracking. |
Benefits | Oxidation prevention, contamination-free, reduced cracking, no cleaning. |
Applications | High-alloy tool steels, aerospace components, precision engineering parts. |
Computer Control | Ensures precise temperature regulation and repeatable results. |
Optimize your metal components with vacuum heat treatment—contact us today to learn more!