Vapor deposition growth is a process used to create thin films or coatings on substrates by depositing material from a vapor phase. This technique is widely used in industries such as semiconductors, optics, and protective coatings. The process can be broadly categorized into two main types: Chemical Vapor Deposition (CVD) and Physical Vapor Deposition (PVD). CVD involves chemical reactions to produce the vapor phase, while PVD relies on physical processes such as evaporation or sputtering. Both methods have distinct steps and mechanisms, but they share the common goal of creating high-quality, uniform, and adherent thin films. The choice between CVD and PVD depends on the specific application, desired film properties, and the materials involved.
Key Points Explained:
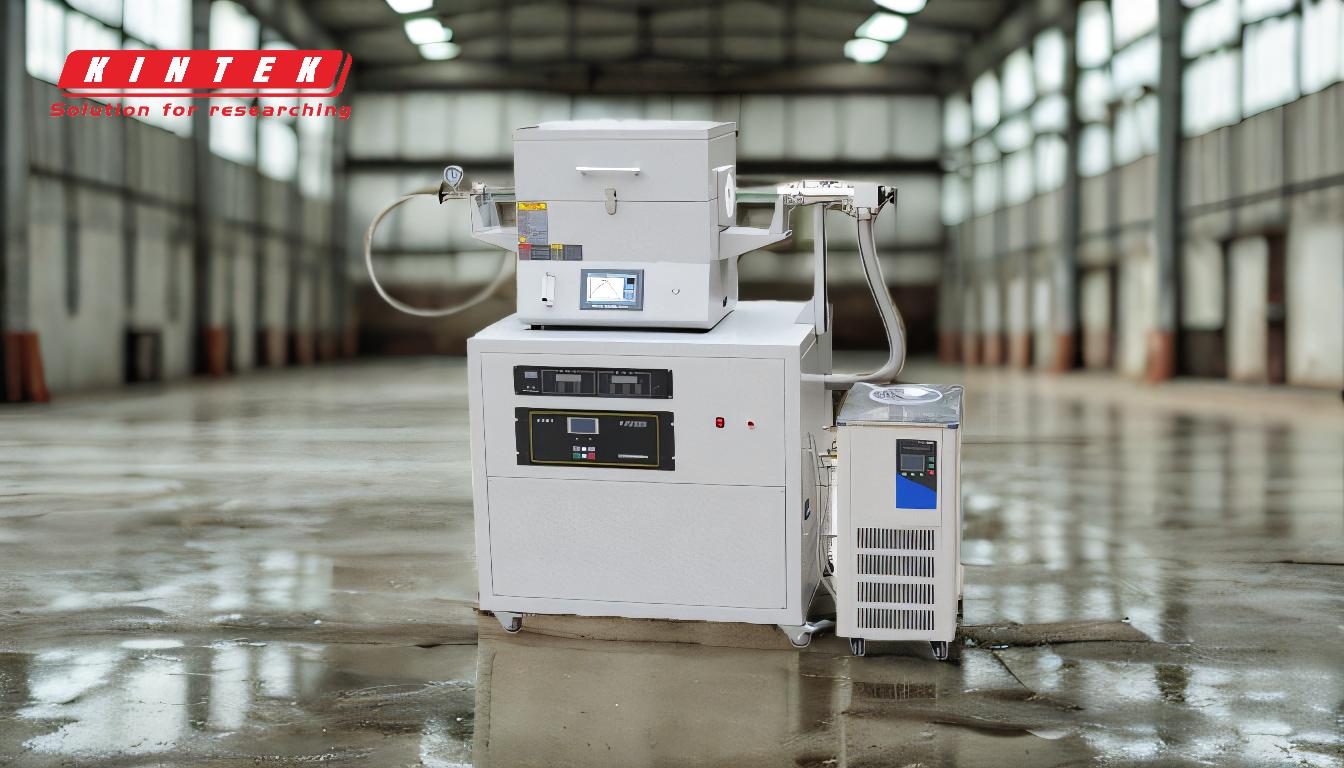
-
Chemical Vapor Deposition (CVD):
- Process Overview: CVD involves the use of volatile precursors that chemically react to form a solid material on the substrate. The process typically occurs in a controlled environment with elevated temperatures and pressures.
-
Steps Involved:
- Transport of Reacting Gases: The gaseous species are transported to the substrate surface.
- Adsorption: The gases adsorb onto the substrate surface.
- Surface Reactions: Chemical reactions occur on the surface, facilitated by heat or plasma, leading to the formation of the desired film.
- Nucleation and Growth: The film nucleates and grows as the reaction products accumulate on the substrate.
- Desorption and Removal: By-products of the reaction are desorbed and removed from the chamber.
- Advantages: CVD produces films that are stoichiometric, dense, and of high quality. The film thickness can be precisely controlled by adjusting the deposition time and power.
-
Physical Vapor Deposition (PVD):
- Process Overview: PVD involves the physical transfer of material from a source to the substrate. This is achieved through processes like evaporation or sputtering.
-
Steps Involved:
- Evaporation: The source material is heated or bombarded with high-energy ions, causing it to vaporize.
- Transportation: The vaporized atoms travel through the vacuum chamber to the substrate.
- Reaction: In reactive PVD, the vaporized atoms may react with gases introduced into the chamber to form compounds like oxides, nitrides, or carbides.
- Deposition: The atoms or compounds deposit onto the substrate, forming a thin film.
- Advantages: PVD allows for the deposition of a wide range of materials, including metals, alloys, and ceramics. The process is performed under vacuum, which minimizes contamination and results in high-purity films.
-
Thermal Vapor Deposition:
- Process Overview: This is a subset of PVD where the source material is heated to produce vapor, which then condenses on the substrate.
- Temperature Range: Typically, the source material is heated to temperatures between 250 to 350 degrees Celsius.
- Application: This method is particularly useful for materials that can be easily vaporized at relatively low temperatures.
-
Aerosol Deposition:
- Process Overview: In this method, fine ceramic particles are accelerated to high speeds and collide with the substrate, forming a dense coating layer.
- Advantages: The process does not require additional heat treatment, making it energy-efficient and suitable for temperature-sensitive substrates.
-
Sputtering:
- Process Overview: Sputtering involves bombarding a target material with high-energy ions, causing atoms to be ejected and deposited onto the substrate.
- Advantages: This method is highly versatile and can be used to deposit a wide range of materials, including metals, semiconductors, and insulators.
-
Comparison Between CVD and PVD:
- CVD: Better for producing high-quality, stoichiometric films with precise control over thickness. However, it often requires higher temperatures and more complex equipment.
- PVD: More versatile in terms of the materials that can be deposited and typically operates at lower temperatures. It is also more suitable for depositing pure metals and alloys.
In conclusion, the vapor deposition growth process is a critical technology in modern manufacturing and materials science. Whether using CVD or PVD, the ability to create thin, uniform, and high-quality films is essential for a wide range of applications, from electronics to protective coatings. Understanding the specific steps and advantages of each method allows for the selection of the most appropriate technique for a given application.
Summary Table:
Method | Process Overview | Advantages |
---|---|---|
Chemical Vapor Deposition (CVD) | Uses chemical reactions to form solid films on substrates. Requires high temperatures and pressures. | Produces stoichiometric, dense, and high-quality films with precise thickness control. |
Physical Vapor Deposition (PVD) | Relies on physical processes like evaporation or sputtering to transfer material to the substrate. | Versatile; deposits metals, alloys, and ceramics with minimal contamination under vacuum. |
Thermal Vapor Deposition | Subset of PVD; heats source material to produce vapor, which condenses on the substrate. | Ideal for materials vaporized at low temperatures (250–350°C). |
Aerosol Deposition | Accelerates fine ceramic particles to form dense coatings without heat treatment. | Energy-efficient and suitable for temperature-sensitive substrates. |
Sputtering | Bombards target material with high-energy ions to eject atoms for deposition. | Highly versatile; deposits metals, semiconductors, and insulators. |
Discover the best vapor deposition method for your application—contact our experts today!