Spark Plasma Sintering (SPS) typically operates at a DC voltage range of 5–10 V. This voltage is applied in pulsed or continuous form to generate a high-energy spark plasma between particles, facilitating rapid heating and sintering. The process relies on Joule heating and electric spark discharge, which create localized high temperatures (up to 10,000°C) to melt and bond particle surfaces. The voltage is critical for activating mechanisms like surface oxide removal, electromigration, and electroplasticity, which enhance densification and bonding. The SPS system includes a pulse DC power supply, which ensures precise control over the sintering process, enabling the production of high-density materials with near-theoretical density.
Key Points Explained:
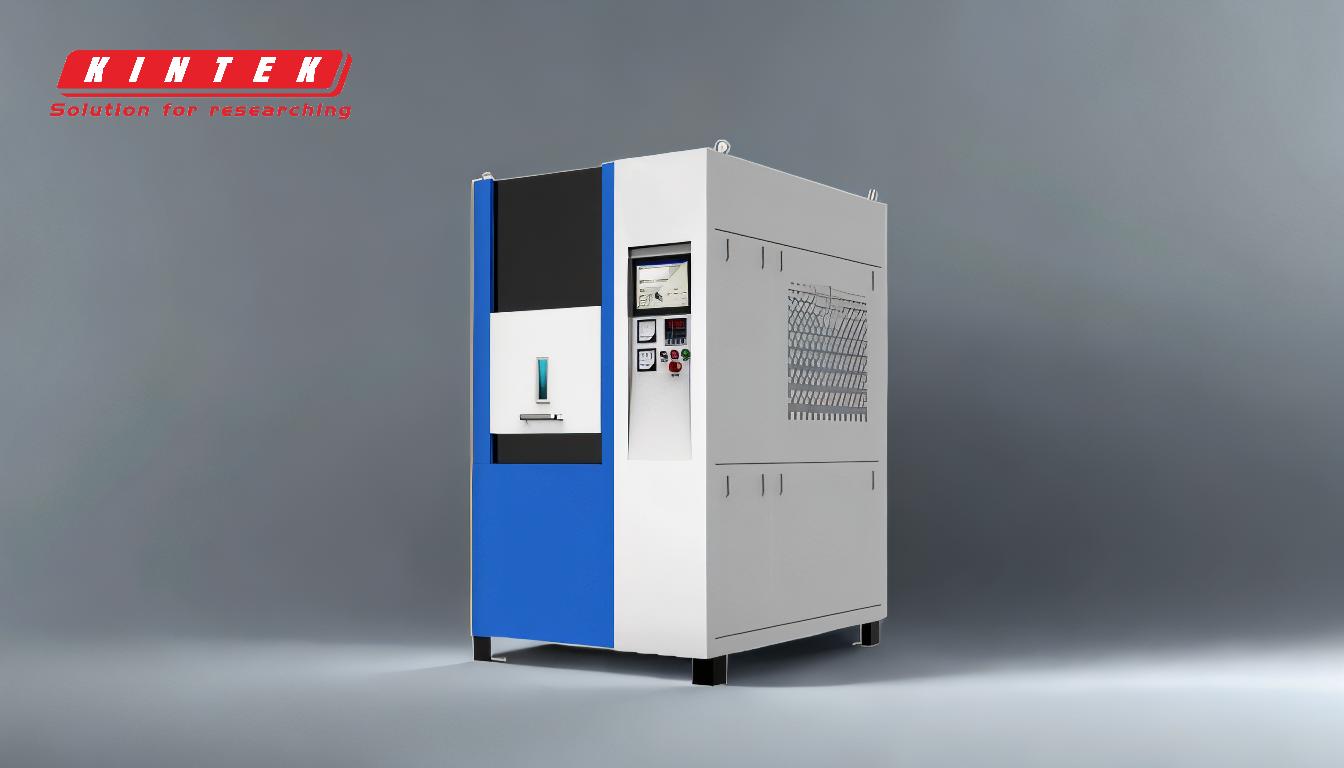
-
Voltage Range in SPS:
- The DC voltage used in Spark Plasma Sintering typically ranges from 5–10 V.
- This voltage is applied either in pulsed or continuous form, depending on the specific requirements of the sintering process.
-
Role of Voltage in SPS:
- The voltage generates a high-energy pulsed current, which produces electric spark discharge between particles.
- This discharge creates a localized high-temperature state (up to 10,000°C), which is essential for melting and bonding particle surfaces.
-
Mechanisms Activated by Voltage:
- Surface Oxide Removal: The high temperature caused by the voltage removes surface oxides, improving particle bonding.
- Electromigration: The electric field drives the movement of atoms, enhancing densification.
- Electroplasticity: The electric current softens the material, making it easier to deform and bond.
-
Joule Heating and Densification:
- The voltage facilitates Joule heating, where electrical energy is converted into heat within the material.
- This heating mechanism plays a dominant role in achieving near-theoretical density at lower sintering temperatures compared to conventional methods.
-
Equipment and Power Supply:
- SPS systems are equipped with a pulse DC power supply, which provides the necessary voltage and current for the process.
- The power supply allows for precise control over sintering parameters, such as temperature, pressure, and current, ensuring consistent and high-quality results.
-
Impact on Sintering Efficiency:
- The use of a specific voltage range ensures rapid heating rates (600–650 K/min) and uniform heating, which are critical for achieving dense sintered bodies.
- The process can achieve over 99% solid density in some cases, making it highly efficient for producing high-strength, high-density parts.
-
Safety and Control Features:
- SPS systems include automated program control for sintering parameters, a safety shutdown function, and a data acquisition system.
- These features ensure safe and reliable operation while maintaining precise control over the sintering process.
-
Comparison with Conventional Methods:
- SPS offers advantages over conventional sintering methods, such as lower sintering temperatures and shorter sintering times (e.g., 5 minutes).
- The ability to achieve high densities at lower temperatures reduces energy consumption and minimizes material degradation.
By understanding the voltage requirements and its role in Spark Plasma Sintering, equipment and consumable purchasers can make informed decisions about selecting the appropriate SPS systems for their specific applications. The precise control over voltage and other parameters ensures the production of high-quality, dense materials with superior mechanical properties.
Summary Table:
Key Aspect | Details |
---|---|
Voltage Range | 5–10 V DC, applied in pulsed or continuous form |
Heating Mechanism | Joule heating and electric spark discharge, creating localized high temperatures (up to 10,000°C) |
Key Mechanisms Activated | Surface oxide removal, electromigration, and electroplasticity |
Densification | Achieves near-theoretical density with rapid heating rates (600–650 K/min) |
Equipment Features | Pulse DC power supply, automated program control, safety shutdown function |
Advantages Over Conventional Methods | Lower sintering temperatures, shorter sintering times, and reduced energy consumption |
Ready to enhance your material sintering process? Contact us today to find the perfect SPS system for your needs!