Isostatic pressing and uniaxial pressing are two widely used powder compaction techniques in various industries. Isostatic pressing involves applying uniform pressure from all directions to consolidate powders or heal defects in castings, while uniaxial pressing applies pressure in a single direction. Isostatic pressing is versatile, suitable for ceramics, metals, composites, plastics, and carbon, and offers benefits like uniform green density and the ability to handle complex shapes. It is used in industries ranging from aerospace and automotive to medical devices and energy storage. Uniaxial pressing, on the other hand, is simpler and more cost-effective for certain applications but lacks the uniformity and versatility of isostatic pressing.
Key Points Explained:
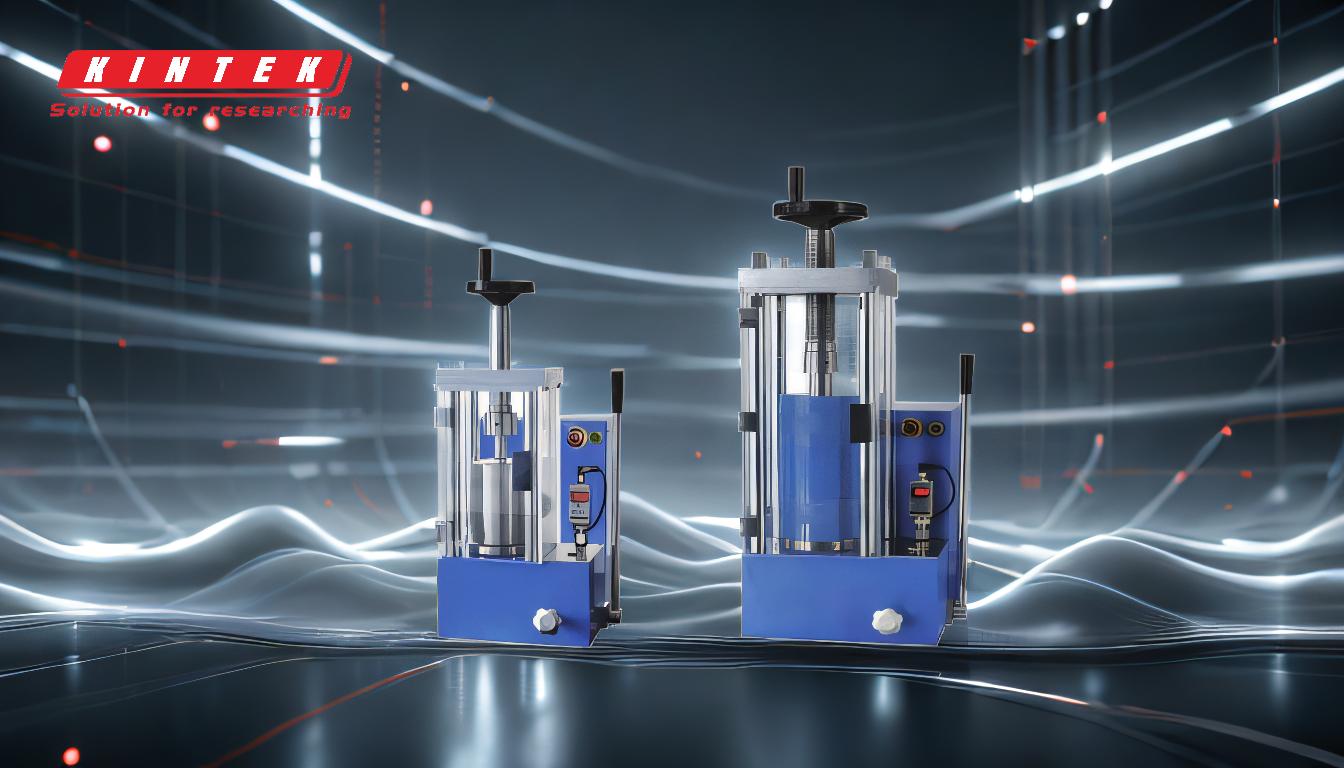
-
Definition of Uniaxial Pressing:
- Uniaxial pressing involves applying pressure in a single direction to compact powder into a desired shape. It is typically used for simpler geometries and is cost-effective for mass production.
- This method relies on rigid dies and punches, which limits its ability to produce complex shapes or achieve uniform density distribution.
-
Definition of Isostatic Pressing:
- Isostatic pressing applies uniform pressure from all directions using a liquid medium, ensuring consistent density throughout the compacted material. This method is ideal for complex shapes and high-performance applications.
- It is divided into Cold Isostatic Pressing (CIP), Warm Isostatic Pressing, and Hot Isostatic Pressing (HIP), each suited for specific temperature and pressure requirements.
-
Key Differences Between Uniaxial and Isostatic Pressing:
- Pressure Application: Uniaxial pressing applies pressure in one direction, while isostatic pressing applies pressure uniformly from all directions.
- Density Uniformity: Isostatic pressing achieves more uniform green density, leading to even shrinkage during sintering, whereas uniaxial pressing may result in density gradients.
- Shape Complexity: Isostatic pressing can handle complex shapes and large parts, while uniaxial pressing is better suited for simpler geometries.
- Binder Requirements: Isostatic pressing does not require wax binders, eliminating the need for dewaxing, which is often necessary in uniaxial pressing.
-
Applications of Isostatic Pressing:
- Isostatic pressing is used in industries such as aerospace, automotive, medical devices, and energy storage. It is particularly valuable for producing high-performance ceramics, advanced alloys, and components for lithium-ion batteries and fuel cells.
- Common applications include pharmaceuticals, explosives, chemicals, and nuclear fuel ferrites.
-
Advantages of Isostatic Pressing:
- Uniform Density: Ensures consistent material properties and reduces defects during sintering.
- Versatility: Suitable for a wide range of materials, including ceramics, metals, and composites.
- Complex Shapes: Capable of producing intricate and large parts that are difficult to achieve with uniaxial pressing.
- No Binder Required: Eliminates the need for wax binders and dewaxing steps, simplifying the process.
-
Isostatic Pressing Process:
- The general steps include loading powder into a flexible mold, sealing the mold, applying pressure via a liquid medium in a pressure vessel, and then releasing the pressure to remove the compacted part.
- This process is highly adaptable, with variations like CIP, Warm Isostatic Pressing, and HIP catering to different material and application needs.
-
Role of Isostatic Pressing in Advanced Manufacturing:
- Isostatic pressing is critical for producing new alloy products and high-performance ceramics like zirconia and alumina, which are difficult to manufacture using traditional casting methods.
- It is also gaining momentum in engineered ceramics for applications requiring near-net-shape and fully dense components.
For more detailed information on isostatic pressing, visit isostatic press.
Summary Table:
Aspect | Uniaxial Pressing | Isostatic Pressing |
---|---|---|
Pressure Application | Single direction | Uniform pressure from all directions |
Density Uniformity | May result in density gradients | Uniform green density |
Shape Complexity | Limited to simpler geometries | Handles complex shapes and large parts |
Binder Requirements | Requires wax binders and dewaxing | No binder required |
Applications | Mass production of simple parts | Aerospace, automotive, medical devices, energy storage |
Discover which pressing method is best for your needs—contact our experts today!