The vacuum arc melting process is a specialized technique used to melt and refine metals, particularly those that are reactive or require high purity. It involves creating an electric arc in a vacuum environment to melt the metal, ensuring minimal contamination and precise control over the melting process. This method is widely used in industries requiring high-quality alloys, such as aerospace and medical applications. The process is characterized by its ability to produce uniform, gas-free, and impurity-free metal ingots, making it ideal for advanced material production.
Key Points Explained:
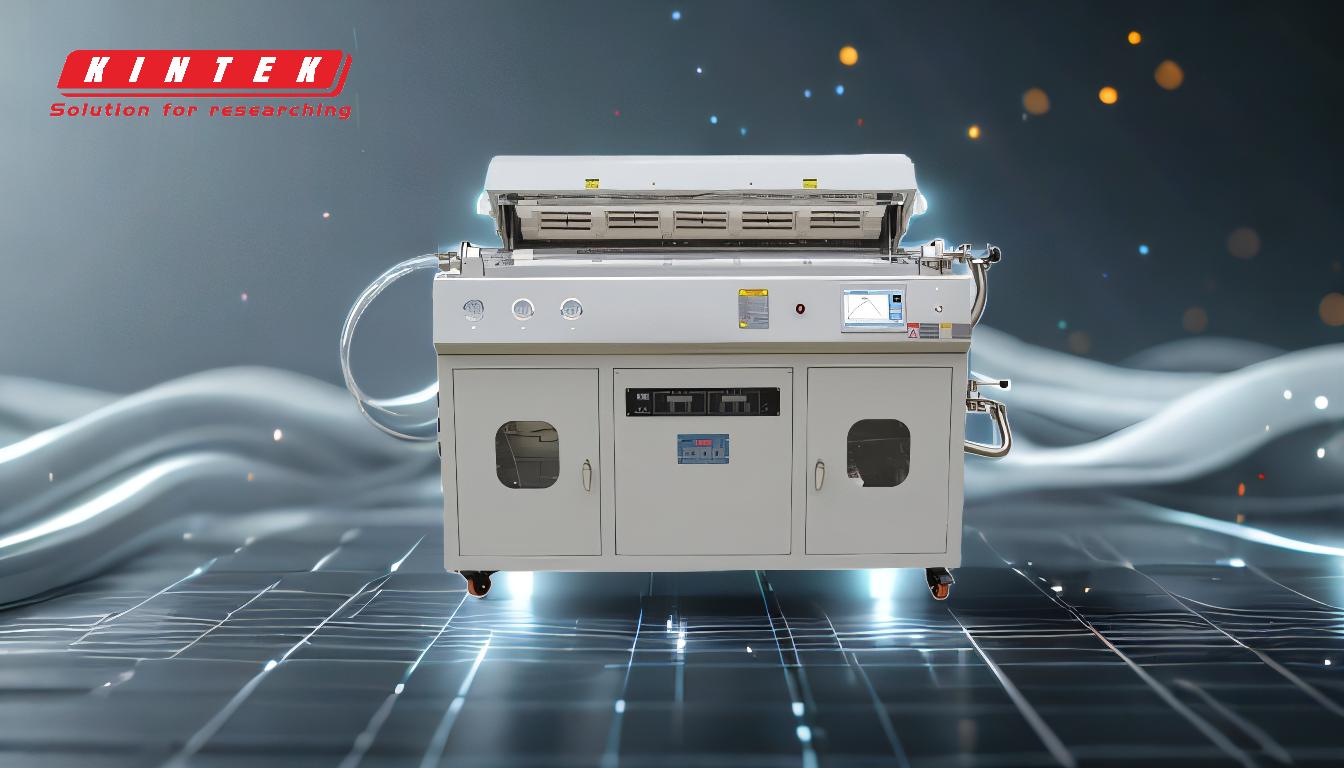
-
Principle of Vacuum Arc Melting:
- The vacuum arc melting process relies on an electric arc generated between an electrode and the metal to be melted. The arc is a self-sustaining discharge phenomenon that produces extremely high temperatures, sufficient to melt even refractory metals.
- The process occurs in a vacuum chamber to prevent oxidation and contamination from atmospheric gases like oxygen and nitrogen. This ensures the production of high-purity metals and alloys.
-
Components of the Vacuum Arc Melting Furnace:
- The main components include the vacuum chamber, electrodes (consumable or non-consumable), and a crucible or mold to hold the molten metal.
- The furnace uses a power supply that converts standard voltage (220V or 380V) into a low-voltage, high-current output to sustain the arc.
-
Stages of the Vacuum Arc Melting Process:
- Preparation Stage: The metal charge is prepared and loaded into the furnace. The vacuum chamber is sealed, and the system is evacuated to create the required vacuum environment.
- Vacuum Stage: The chamber is pumped down to remove air and other gases, ensuring a clean environment for melting.
- Melting Stage: The arc is initiated by creating a short circuit between the electrode and the metal charge. Once the arc is established, the metal begins to melt. The process is repeated multiple times to ensure uniform melting and refining.
- Casting Stage: The molten metal is poured into a mold or crucible to solidify into the desired shape, such as an ingot or casting specimen.
- End Stage: The furnace is cooled, and the final product is removed for further processing or analysis.
-
Advantages of Vacuum Arc Melting:
- High Purity: The vacuum environment prevents contamination, resulting in metals with minimal impurities.
- Uniform Composition: The electromagnetic forces generated during the process promote stirring, ensuring a homogeneous melt.
- Versatility: Suitable for melting reactive and refractory metals that cannot be processed in air or conventional furnaces.
- Precision: The process allows for precise control over melting parameters, such as temperature and cooling rates.
-
Applications of Vacuum Arc Melting:
- This process is widely used in the production of high-performance alloys for aerospace, medical, and nuclear industries.
- It is particularly valuable for melting titanium, zirconium, and other reactive metals that require high purity and precise control over material properties.
-
Comparison with Other Melting Processes:
- Unlike vacuum induction melting, which uses electromagnetic induction to heat the metal, vacuum arc melting relies on the direct heat generated by the electric arc.
- The vacuum arc melting process is more suitable for materials that are difficult to melt using induction heating, such as those with high melting points or low electrical conductivity.
By understanding these key points, a purchaser of equipment or consumables can make informed decisions about the suitability of vacuum arc melting for their specific needs, ensuring optimal results in material production.
Summary Table:
Aspect | Details |
---|---|
Principle | Electric arc in a vacuum melts metals, ensuring high purity and uniformity. |
Components | Vacuum chamber, electrodes, crucible, and power supply. |
Stages | Preparation, vacuum, melting, casting, and end stage. |
Advantages | High purity, uniform composition, versatility, and precision. |
Applications | Aerospace, medical, and nuclear industries; reactive metals like titanium. |
Comparison | More suitable for high-melting-point or low-conductivity materials. |
Interested in high-purity metal production? Contact us today to learn more about vacuum arc melting solutions!