A vacuum coating machine is a specialized piece of equipment used to apply thin films or coatings onto various substrates, such as glass, metal, or plastics, in a vacuum environment. This process is widely used across industries like aerospace, automotive, medical, and industrial manufacturing to enhance properties such as wear resistance, hardness, corrosion protection, and aesthetic appeal. Vacuum coating techniques, such as Physical Vapor Deposition (PVD), involve vaporizing a target material and depositing it onto a substrate, creating thin, uniform layers. These coatings are critical in applications ranging from reflective surfaces and optical films to energy-efficient glass and durable automotive components. The vacuum environment ensures a clean, controlled process, free from contaminants, which is essential for achieving high-quality, consistent results.
Key Points Explained:
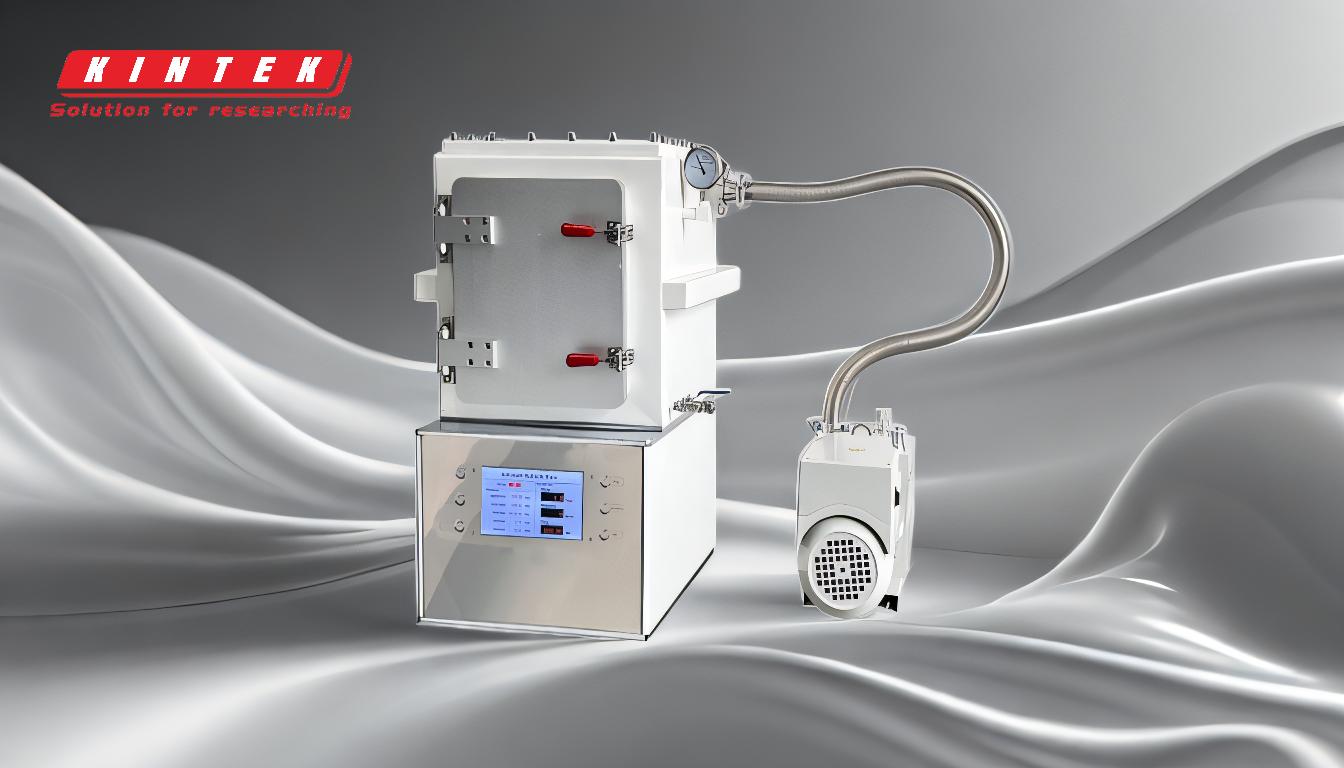
-
Definition and Purpose of Vacuum Coating Machines:
- A vacuum coating machine is designed to deposit thin films or coatings onto substrates in a vacuum environment. This process is used to enhance the properties of materials, such as improving wear resistance, increasing hardness, and providing corrosion protection. The vacuum environment ensures that the coating process is free from contaminants, resulting in high-quality, uniform coatings.
-
Applications of Vacuum Coating:
- Vacuum coating is widely used in industries such as aerospace, automotive, medical, and industrial manufacturing. Specific applications include:
- Aerospace: Protective coatings for components exposed to extreme conditions.
- Automotive: Hard coatings for engine components and decorative finishes.
- Medical: Biocompatible coatings for implants and surgical tools.
- Industrial: Corrosion-resistant coatings for machinery and tools.
- Vacuum coating is widely used in industries such as aerospace, automotive, medical, and industrial manufacturing. Specific applications include:
-
Physical Vapor Deposition (PVD):
- PVD is a common vacuum coating technique where a target material is heated until it vaporizes, and the vapor is then deposited onto a substrate. This process creates thin films that are only a few nanometers to micrometers thick but provide significant benefits, such as improved wear resistance, increased hardness, and enhanced aesthetic appearance.
-
Benefits of Vacuum Coating:
- Durability: Coatings improve the wear resistance and hardness of materials.
- Corrosion Protection: Coatings protect substrates from environmental damage.
- Aesthetic Enhancement: Coatings can provide decorative finishes and improve the appearance of products.
- Energy Efficiency: Coatings such as low-emissivity glass help in energy conservation.
-
Types of Coatings and Their Uses:
- Low-Emissivity Glass: Used in energy-efficient windows to reduce heat transfer.
- Hard Coatings: Applied to engine components to enhance durability.
- Ophthalmic Coatings: Used on lenses to improve scratch resistance and optical properties.
- Reflective Coatings: Used in mirrors and optical films for enhanced reflectivity.
-
Vacuum Environment Advantages:
- The vacuum environment in coating machines prevents contamination from gases and particles, ensuring a clean and controlled process. This is crucial for achieving consistent, high-quality coatings, especially in industries where precision and reliability are paramount.
-
Comparison with Other Vacuum Processes:
- While vacuum coating is focused on applying thin films, other vacuum processes, such as vacuum drying and vacuum brazing, serve different purposes. For example, vacuum drying removes moisture from substances under low pressure, while vacuum brazing joins metals using a filler metal in a vacuum furnace. Each process leverages the benefits of a vacuum environment but for distinct applications.
-
Industrial Scale and Versatility:
- Vacuum coating is used on an industrial scale for film preparation of inorganic materials. It is versatile and can be applied to various substrates, including glass, metal, and plastics, making it suitable for a wide range of products and industries.
By understanding these key points, a purchaser can better evaluate the suitability of a vacuum coating machine for their specific needs, ensuring they select the right equipment to achieve desired results in their applications.
Summary Table:
Aspect | Details |
---|---|
Definition | Applies thin films/coatings in a vacuum environment for enhanced properties. |
Applications | Aerospace, automotive, medical, industrial manufacturing. |
Techniques | Physical Vapor Deposition (PVD). |
Benefits | Durability, corrosion protection, aesthetic enhancement, energy efficiency. |
Types of Coatings | Low-emissivity glass, hard coatings, ophthalmic coatings, reflective films. |
Vacuum Advantages | Clean, controlled process free from contaminants. |
Industrial Versatility | Suitable for glass, metal, plastics, and more. |
Discover how a vacuum coating machine can transform your materials—contact us today for expert guidance!