Vacuum deposition is a critical process in nanotechnology used to create thin films and coatings at the nanoscale. It involves depositing materials onto a substrate in a vacuum environment, which minimizes contamination and allows for precise control over the deposition process. This technique is widely used in the production of semiconductors, optical coatings, and nanoscale devices. The process can be achieved through various methods, including physical vapor deposition (PVD) and chemical vapor deposition (CVD), each offering unique advantages depending on the desired material properties and applications. Vacuum deposition is essential for achieving high-quality, uniform, and defect-free thin films, making it indispensable in nanotechnology research and manufacturing.
Key Points Explained:
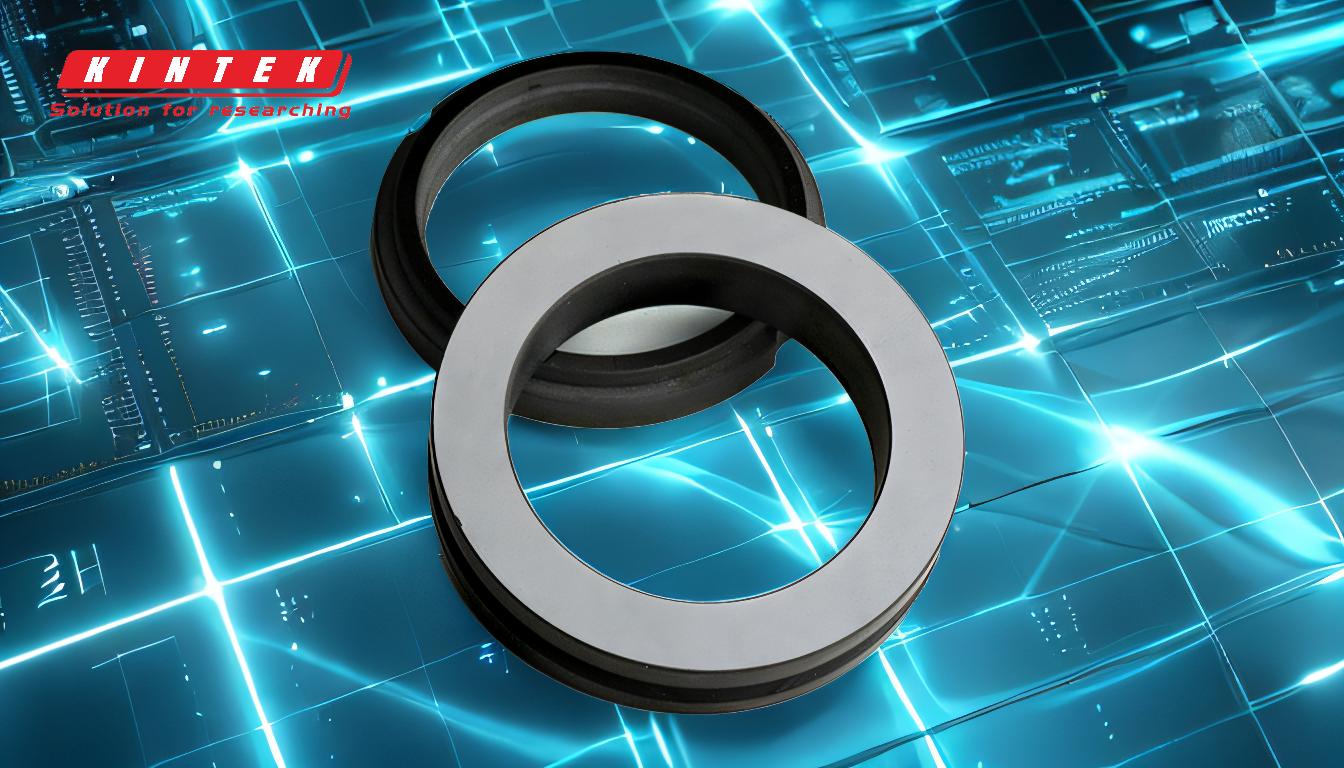
-
Definition and Purpose of Vacuum Deposition:
- Vacuum deposition is a process where materials are deposited onto a substrate in a vacuum environment. This method is crucial in nanotechnology for creating thin films and coatings with precise thickness and composition.
- The vacuum environment reduces the presence of contaminants, ensuring high-purity deposits and enabling the production of high-quality nanoscale materials.
-
Types of Vacuum Deposition Techniques:
- Physical Vapor Deposition (PVD): This method involves the physical transfer of material from a source to the substrate. Common PVD techniques include evaporation and sputtering. In evaporation, the material is heated until it vaporizes, and the vapor then condenses on the substrate. In sputtering, atoms are ejected from a target material due to bombardment by high-energy particles, and these atoms then deposit onto the substrate.
- Chemical Vapor Deposition (CVD): This technique involves the chemical reaction of gaseous precursors to form a solid material on the substrate. CVD is often used for depositing complex materials and can produce films with excellent uniformity and conformality.
-
Applications in Nanotechnology:
- Semiconductors: Vacuum deposition is used to create thin films of semiconductors, which are essential for the fabrication of integrated circuits and other electronic devices.
- Optical Coatings: The technique is employed to produce anti-reflective coatings, mirrors, and other optical components with precise optical properties.
- Nanoscale Devices: Vacuum deposition is crucial for the fabrication of nanoscale devices, such as sensors, transistors, and memory devices, where precise control over material properties is required.
-
Advantages of Vacuum Deposition:
- High Purity: The vacuum environment minimizes contamination, resulting in high-purity deposits.
- Precision: The process allows for precise control over the thickness, composition, and structure of the deposited films.
- Uniformity: Vacuum deposition can produce highly uniform and defect-free thin films, which are essential for many nanotechnology applications.
-
Challenges and Considerations:
- Cost: The equipment and maintenance required for vacuum deposition can be expensive, making it less accessible for some applications.
- Complexity: The process can be complex and requires careful control of parameters such as pressure, temperature, and deposition rate to achieve the desired results.
- Material Limitations: Not all materials are suitable for vacuum deposition, and some may require specialized techniques or conditions.
-
Future Trends in Vacuum Deposition:
- Advanced Materials: Research is ongoing to develop new materials and deposition techniques that can further enhance the properties of thin films, such as improved conductivity, durability, and optical performance.
- Scalability: Efforts are being made to scale up vacuum deposition processes for industrial applications, making it more cost-effective and accessible for large-scale production.
- Integration with Other Technologies: Vacuum deposition is increasingly being integrated with other nanofabrication techniques, such as lithography and self-assembly, to create more complex and functional nanoscale devices.
In summary, vacuum deposition is a versatile and essential technique in nanotechnology, enabling the creation of high-quality thin films and coatings with precise control over their properties. Its applications span a wide range of fields, from electronics to optics, and ongoing research continues to expand its capabilities and potential uses.
Summary Table:
Aspect | Details |
---|---|
Definition | Depositing materials onto a substrate in a vacuum environment. |
Purpose | Creates thin films with precise thickness and composition. |
Techniques | PVD (evaporation, sputtering) and CVD. |
Applications | Semiconductors, optical coatings, nanoscale devices. |
Advantages | High purity, precision, uniformity, and defect-free films. |
Challenges | High cost, complexity, and material limitations. |
Future Trends | Advanced materials, scalability, and integration with other technologies. |
Discover how vacuum deposition can revolutionize your nanotechnology projects—contact our experts today!