Vacuum hardening heat treatment is a specialized process used to enhance the mechanical and chemical properties of metal components by heating them in a vacuum environment. This method eliminates air and other gases from the treatment chamber, ensuring a controlled atmosphere that prevents oxidation, scaling, and contamination. It is particularly beneficial for materials like special alloys, tools, molds, and precision parts, as it minimizes deformation, improves surface quality, and enhances durability. The process also offers environmental and operational advantages, such as reduced pollution, safer working conditions, and improved repeatability. Vacuum hardening is widely used in industries requiring high precision and reliability.
Key Points Explained:
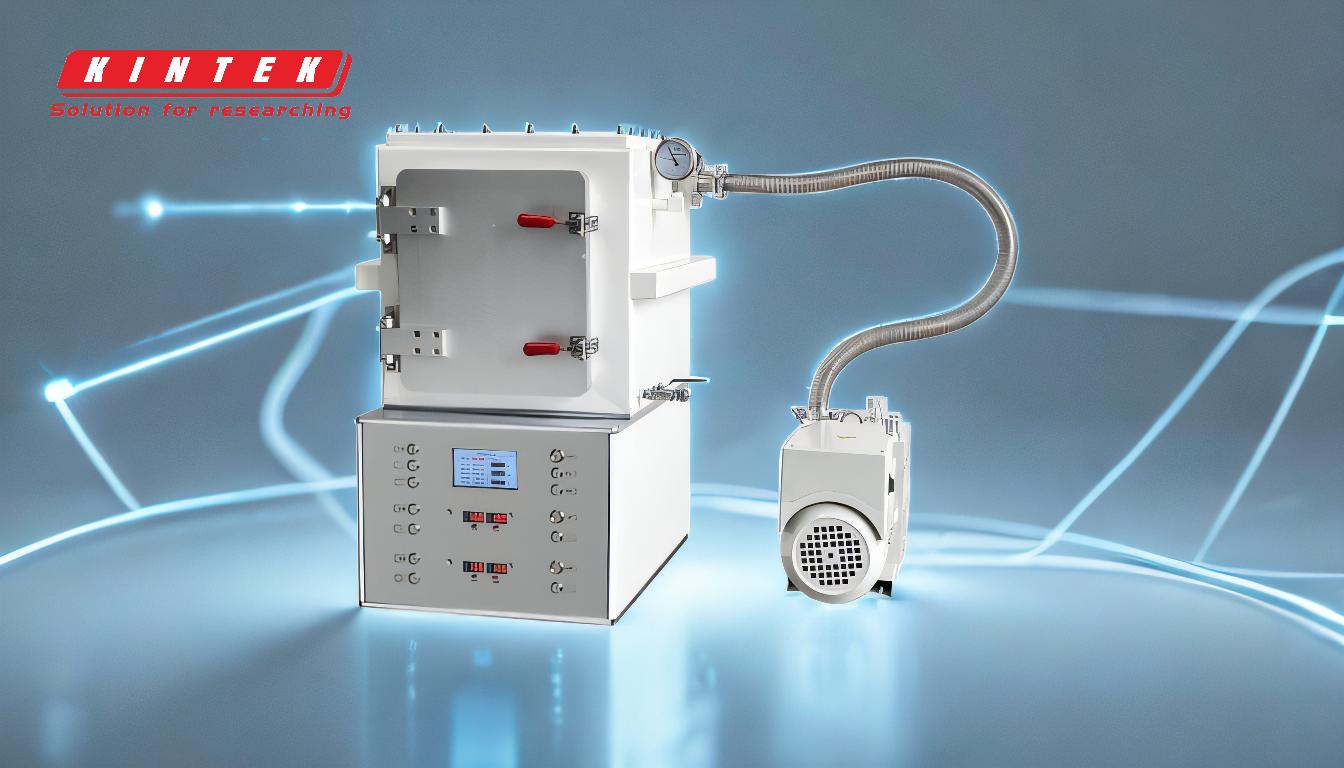
-
Definition and Process:
- Vacuum hardening heat treatment involves heating metal components in a vacuum environment where air and other gases are removed using a vacuum pump. This ensures a controlled atmosphere, preventing oxidation and contamination during the process.
- The workpiece is heated slowly in the furnace, which minimizes internal thermal stress and deformation, resulting in high-quality products with consistent properties.
-
Benefits of Vacuum Hardening:
- Minimal Deformation: The slow heating process reduces thermal stress, leading to small deformation and high precision in the final product.
- Improved Surface Quality: The absence of oxygen prevents scaling and discoloration, ensuring a clean and smooth surface finish.
- Enhanced Mechanical Properties: Vacuum hardening improves hardness, elasticity, and shear strength, making the treated parts more durable and resistant to wear and stress.
- Environmental and Safety Advantages: The process is free from flammable gases and harmful oxygen, making it safer and pollution-free. It also avoids risks like hydrogen embrittlement.
-
Applications:
- Vacuum hardening is suitable for a wide range of materials, including special alloys, general engineering steel, tools, molds, and precision parts. Its ability to maintain dimensional stability and surface quality makes it ideal for industries requiring high precision, such as aerospace, automotive, and tool manufacturing.
-
Operational Flexibility and Repeatability:
- The process offers good invariability and repeatability, ensuring consistent results across batches. This makes it a reliable choice for mass production and high-precision applications.
- The controlled environment allows for flexible operation, as specific gaseous mediums can be introduced if needed to achieve desired surface finishes or other properties.
-
Technical Aspects:
- Vacuum levels are expressed inversely to pressure levels, with high vacuum indicating low pressure. This precise control over the vacuum environment is crucial for achieving the desired material properties.
- The use of vacuum pumping systems ensures that the chamber remains sealed and free from air leaks, which is essential for maintaining the integrity of the heat treatment process.
For more detailed information on vacuum heat treatment, you can explore its principles, equipment, and applications in various industries. This method is a cornerstone of modern metallurgical processes, offering unmatched precision and quality in heat treatment.
Summary Table:
Aspect | Details |
---|---|
Process | Heating metal components in a vacuum to prevent oxidation and contamination. |
Benefits | Minimal deformation, improved surface quality, enhanced mechanical properties, and environmental safety. |
Applications | Special alloys, tools, molds, precision parts, aerospace, and automotive. |
Operational Advantages | High repeatability, flexibility, and consistent results. |
Technical Details | Controlled vacuum environment ensures precise material properties. |
Discover how vacuum hardening can improve your metal components—contact us today for expert advice!