Vacuum hardening is a specialized heat treatment process used to enhance the mechanical properties of metals, particularly steel, by heating them in a vacuum environment to high temperatures and then rapidly cooling (quenching) them. This process is carried out in a vacuum hardening furnace, which ensures a contamination-free environment, prevents oxidation, and allows for precise temperature control. The vacuum environment eliminates the need for protective atmospheres, making it ideal for producing high-quality, ultra-clean components with improved hardness, strength, and wear resistance.
Key Points Explained:
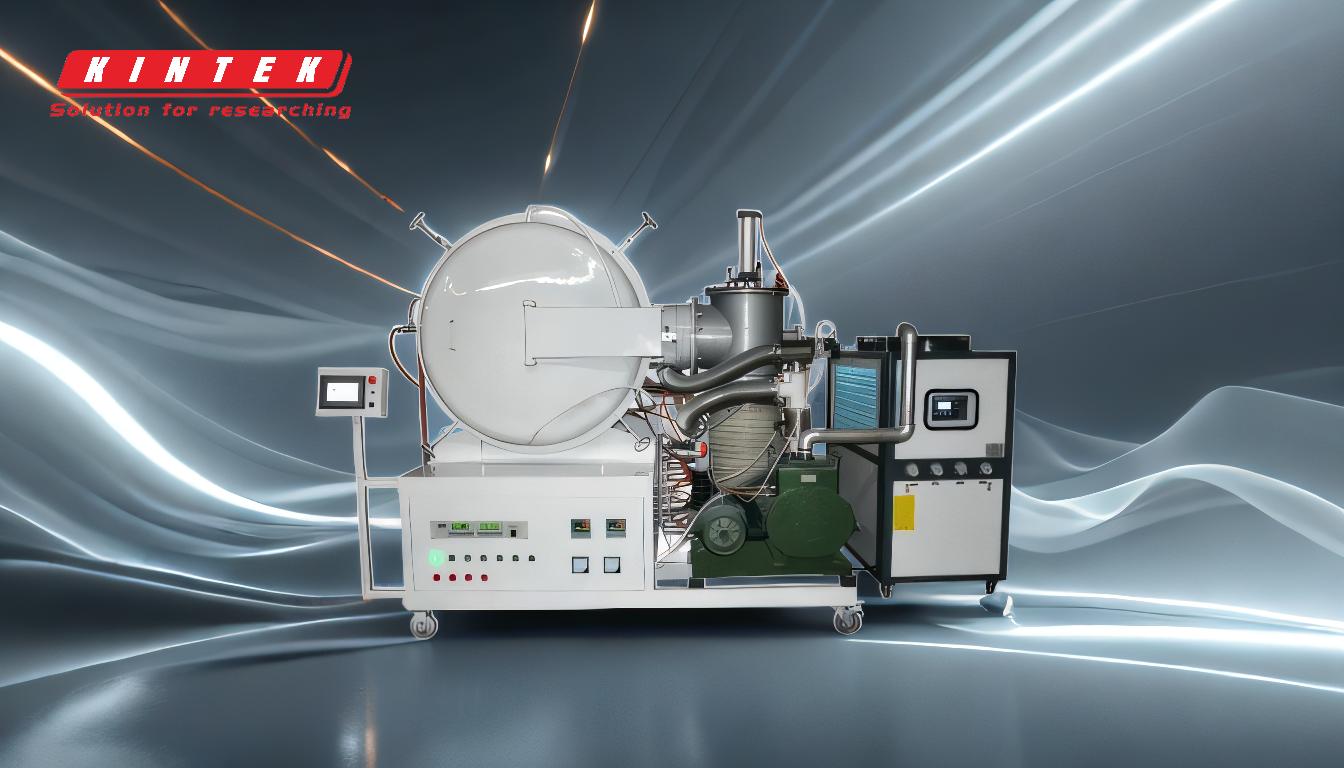
-
Vacuum Environment and Its Benefits:
- A vacuum environment is created by evacuating air from the furnace chamber, which eliminates oxygen and other reactive gases. This prevents oxidation, decarburization, and contamination of the metal surface.
- The absence of impurities ensures that the material retains its integrity, resulting in a clean and defect-free surface finish.
- This environment is particularly beneficial for materials that are sensitive to oxidation or require high-purity conditions, such as tool steels, stainless steels, and superalloys.
-
Heating and Temperature Control:
- The workpiece is heated to a specific temperature, typically between 800°C and 1300°C, depending on the material and desired properties.
- Precise temperature control is achieved through advanced heating elements and computer-controlled systems, ensuring uniform heating and consistent results.
- Uniform temperature distribution is critical to avoid thermal stress and ensure even hardening throughout the material.
-
Quenching Process:
- After reaching the desired temperature, the workpiece is rapidly cooled (quenched) using inert gases like nitrogen or argon. This rapid cooling transforms the microstructure of the metal, increasing its hardness and strength.
- The quenching process in a vacuum furnace is highly controlled, minimizing distortion and cracking compared to traditional quenching methods.
-
Applications of Vacuum Hardening:
- Vacuum hardening is widely used in industries that require high-performance components, such as aerospace, automotive, tool and die manufacturing, and medical device production.
- It is particularly suitable for complex geometries and thin-walled parts, where traditional hardening methods might cause distortion or uneven hardening.
-
Advantages of Vacuum Hardening:
- Improved Mechanical Properties: The process enhances hardness, wear resistance, and fatigue strength while maintaining dimensional stability.
- Clean and Oxidation-Free Surface: The vacuum environment ensures a pristine surface finish, eliminating the need for additional cleaning or post-treatment.
- Energy Efficiency: Advanced insulation and control systems reduce energy consumption and heat loss, making the process more sustainable.
- Versatility: A vacuum hardening furnace can also be used for other heat treatment processes like annealing, tempering, and brazing, making it a versatile investment for manufacturers.
-
Comparison with Other Hardening Methods:
- Unlike induction hardening, which only hardens the surface layer, vacuum hardening can be applied to the entire workpiece, providing uniform properties throughout.
- Compared to traditional furnace hardening, vacuum hardening offers better control over the process, resulting in higher-quality components with fewer defects.
In summary, vacuum hardening is a highly effective and precise heat treatment process that leverages the benefits of a vacuum environment to produce superior-quality metal components. Its ability to prevent contamination, ensure uniform hardening, and improve mechanical properties makes it an essential process for industries demanding high-performance materials. The use of a vacuum hardening furnace is key to achieving these results, offering advanced temperature control, energy efficiency, and versatility for a wide range of applications.
Summary Table:
Aspect | Details |
---|---|
Process | Heating metals in a vacuum environment followed by rapid quenching. |
Key Benefits | Prevents oxidation, ensures contamination-free surfaces, and improves hardness. |
Temperature Range | 800°C to 1300°C, depending on material and desired properties. |
Applications | Aerospace, automotive, tool and die manufacturing, medical devices. |
Advantages | Clean surface finish, energy efficiency, versatility, and uniform hardening. |
Comparison | Superior to traditional methods like induction hardening and furnace hardening. |
Unlock the full potential of vacuum hardening for your materials—contact our experts today!