Vacuum nitriding is a specialized heat treatment process used to enhance the surface properties of metal components, particularly steel. It involves exposing the workpiece to a nitrogen-rich environment under vacuum conditions, which allows for precise control over the nitrogen diffusion into the metal surface. This process results in the formation of a hard, wear-resistant nitride layer while maintaining the core properties of the material. Vacuum nitriding is widely used in industries such as automotive, aerospace, and tool manufacturing to improve the durability, corrosion resistance, and fatigue strength of critical components.
Key Points Explained:
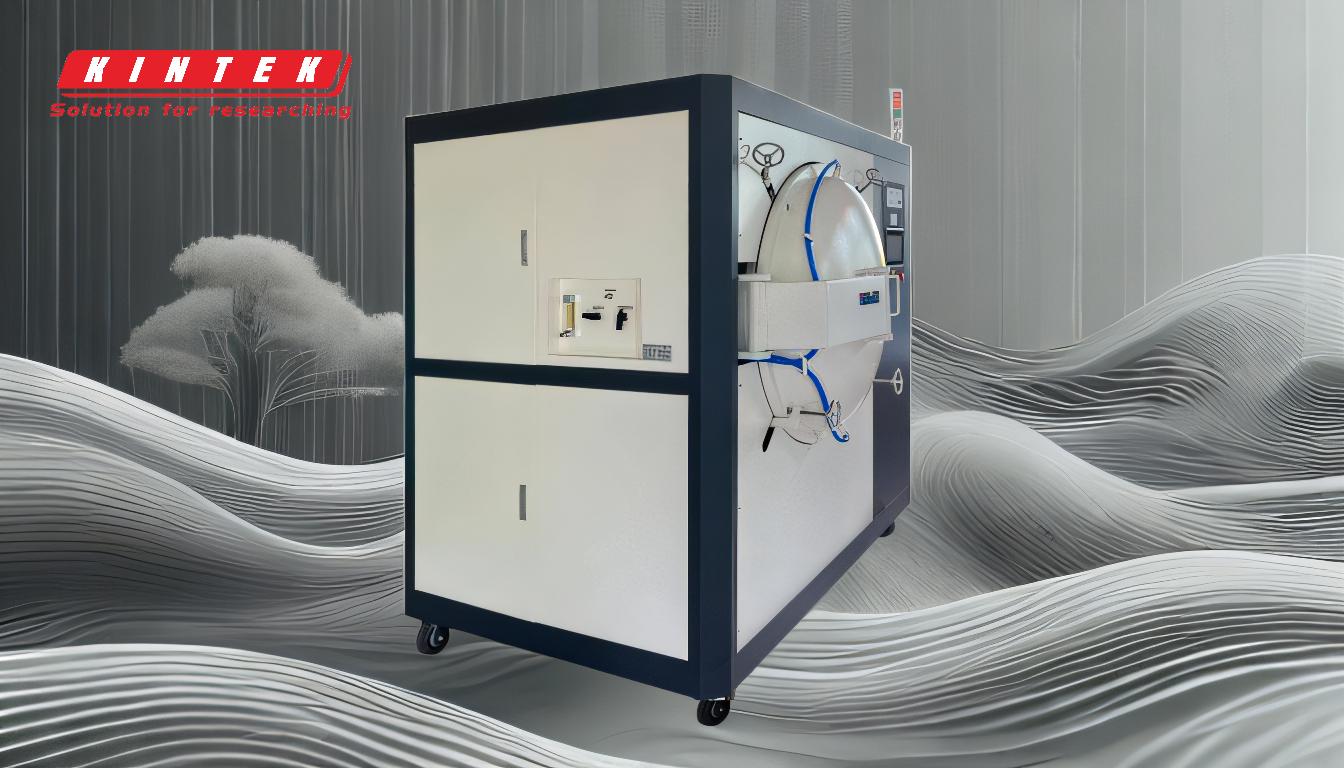
-
Definition of Vacuum Nitriding:
- Vacuum nitriding is a thermochemical process where nitrogen is introduced into the surface of a metal, typically steel, under controlled vacuum conditions. The vacuum environment ensures minimal oxidation and contamination, leading to a high-quality nitride layer.
-
Process Mechanism:
- The workpiece is placed in a vacuum chamber and heated to a specific temperature, usually between 500°C and 600°C.
- Nitrogen gas or ammonia is introduced into the chamber, where it dissociates into active nitrogen atoms.
- These nitrogen atoms diffuse into the metal surface, forming hard nitrides such as iron nitrides (Fe2N, Fe3N, Fe4N) and alloy nitrides (e.g., chromium nitride, vanadium nitride).
-
Advantages of Vacuum Nitriding:
- Enhanced Surface Hardness: The nitride layer significantly increases surface hardness, improving wear resistance.
- Improved Corrosion Resistance: The nitride layer acts as a barrier against corrosive environments.
- Dimensional Stability: The process minimizes distortion, making it ideal for precision components.
- Uniform Treatment: The vacuum environment ensures uniform nitrogen diffusion, even in complex geometries.
-
Applications:
- Automotive Industry: Used for gears, crankshafts, and camshafts to enhance durability and performance.
- Aerospace: Applied to turbine blades and other high-stress components to improve fatigue resistance.
- Tool Manufacturing: Enhances the lifespan of cutting tools, dies, and molds.
-
Comparison with Other Processes:
- Unlike traditional gas nitriding, vacuum nitriding offers better control over the nitrogen concentration and depth of the nitride layer.
- It produces a cleaner surface finish compared to salt bath nitriding, which can leave residues.
-
Equipment Used:
- Vacuum nitriding is typically performed in specialized vacuum furnaces equipped with gas injection systems and precise temperature controls. These furnaces ensure consistent results and high repeatability.
-
Material Compatibility:
- While primarily used for steel, vacuum nitriding can also be applied to other materials such as titanium and certain alloys, provided they can form stable nitrides.
-
Environmental and Safety Considerations:
- The vacuum environment reduces the risk of harmful emissions, making it a more environmentally friendly option compared to some other nitriding methods.
- Proper handling of gases and adherence to safety protocols are essential to prevent accidents.
By understanding the principles and benefits of vacuum nitriding, manufacturers can make informed decisions about its application in their processes, ensuring optimal performance and longevity of their components.
Summary Table:
Aspect | Details |
---|---|
Definition | A thermochemical process introducing nitrogen into metal surfaces under vacuum. |
Process Temperature | 500°C to 600°C. |
Key Benefits | Enhanced surface hardness, improved corrosion resistance, minimal distortion. |
Applications | Automotive, aerospace, and tool manufacturing. |
Equipment | Specialized vacuum furnaces with gas injection and precise temperature control. |
Material Compatibility | Primarily steel, but also titanium and certain alloys. |
Environmental Impact | Reduced harmful emissions compared to other nitriding methods. |
Discover how vacuum nitriding can optimize your components—contact our experts today!