Vacuum quenching is a specialized heat treatment process conducted in a vacuum environment to harden metal workpieces. By removing air from the chamber using a vacuum pump, this method eliminates oxidation and decarburization, ensuring high-quality results with minimal deformation. The process involves heating the workpiece slowly to reduce thermal stress, followed by rapid cooling using mediums like oil or inert gases. Vacuum quenching is ideal for producing bright, clean surfaces with excellent mechanical properties, making it suitable for industries requiring precision and durability, such as aerospace and tool manufacturing.
Key Points Explained:
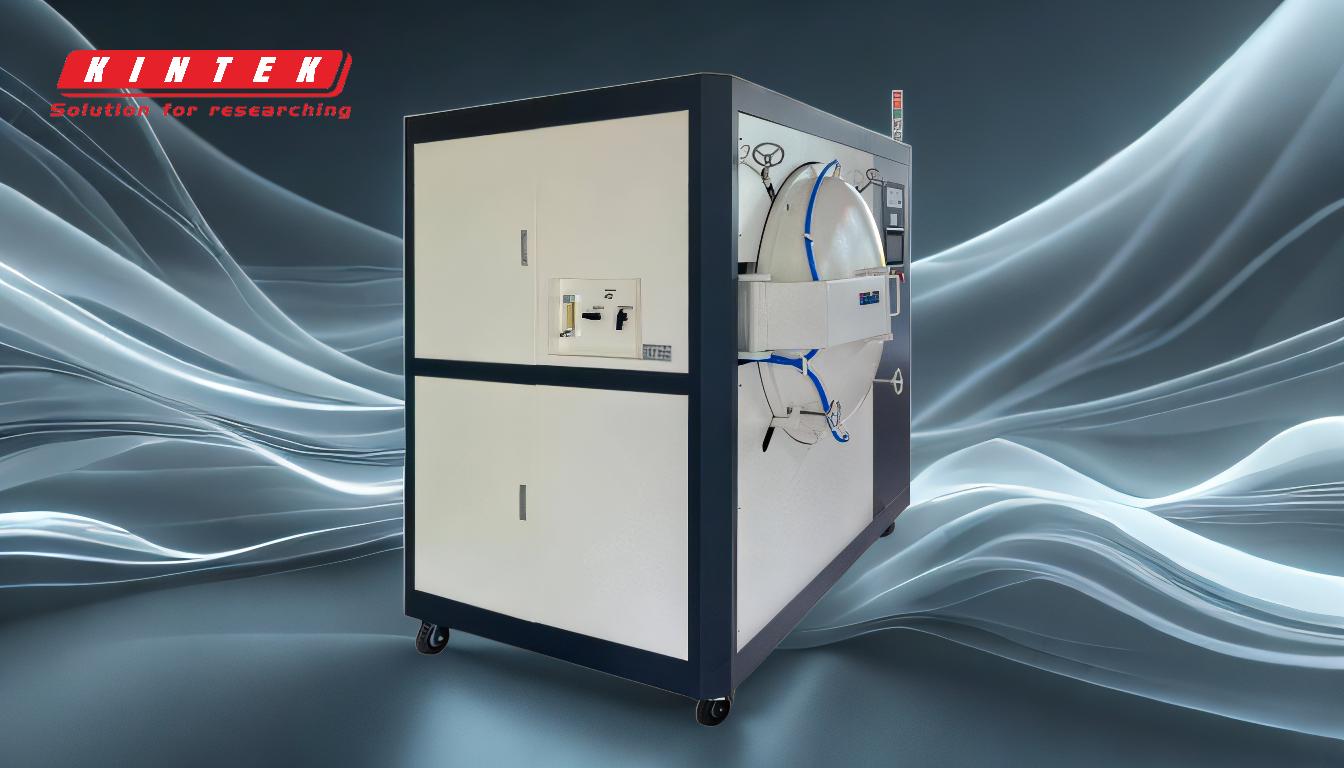
-
Definition and Process of Vacuum Quenching:
- Vacuum quenching is a heat treatment method performed in a vacuum environment to harden metal workpieces.
- The process involves removing air from a sealed chamber using a vacuum pump, ensuring no oxidation or contamination occurs during heating and cooling.
- This method is particularly effective for achieving predictable and high-quality results.
-
Advantages of Vacuum Quenching:
- Surface Quality: The absence of air prevents oxidation and decarburization, resulting in bright, clean surfaces.
- Minimal Deformation: Slow heating in the vacuum furnace reduces internal thermal stress, leading to small deformation and high precision.
- Versatility: Suitable for a wide range of materials, including those prone to deformation, such as long rods, shafts, and plates.
-
Cooling Methods in Vacuum Quenching:
- Vacuum Oil Quenching: Uses oil as the cooling medium, providing faster cooling rates and producing workpieces with good organizational properties and no surface oxidation.
- Vacuum Gas Quenching: Utilizes high-purity inert gases (Ar/He) or non-reactive gases (N2) for cooling. This method leaves the workpiece with a smooth surface and eliminates the need for post-quenching cleaning.
-
Applications and Suitability:
- Vacuum quenching is ideal for industries requiring high precision and durability, such as aerospace, tool manufacturing, and automotive.
- The vertical type vacuum gas quenching furnace is particularly suitable for large or complex workpieces, ensuring minimal deformation and maintaining brightness after treatment.
-
Comparison with Other Heat Treatment Methods:
- Unlike traditional heat treatment methods, vacuum quenching eliminates the risk of surface contamination and oxidation.
- The controlled environment allows for precise management of partial gas pressure, enabling advanced processes like carburizing or carbonitriding at low pressure and higher temperatures, which reduces cycle time.
-
Role of Vacuum Heat Treatment:
- Vacuum heat treatment, including vacuum quenching, ensures superior surface protection and mechanical properties.
- The process is enhanced by vacuum pumping systems that maintain consistent vacuum levels, further improving the quality and consistency of the treated workpieces.
For more detailed information on the broader process, refer to vacuum heat treatment.
Summary Table:
Aspect | Details |
---|---|
Definition | Heat treatment in a vacuum to harden metal workpieces. |
Key Advantages | Bright surfaces, minimal deformation, versatile for various materials. |
Cooling Methods | Oil or inert gases for rapid cooling. |
Applications | Aerospace, tool manufacturing, automotive. |
Comparison | Eliminates oxidation and contamination compared to traditional methods. |
Discover how vacuum quenching can enhance your metalwork—contact us today for expert guidance!