Vacuum thermal evaporation is a sophisticated process used in various industries to deposit thin films of materials onto substrates. This method involves heating a material in a vacuum chamber until it vaporizes, allowing the vapor to condense on a substrate, forming a thin film. The vacuum environment is crucial as it minimizes contamination and ensures that the evaporated atoms travel without collisions to the substrate. This technique is widely used in the production of electronic and optical devices, such as solar cells, OLED displays, and microelectromechanical systems (MEMS). Understanding the principles and applications of vacuum thermal evaporation is essential for anyone involved in the procurement of equipment or materials for thin-film deposition processes.
Key Points Explained:
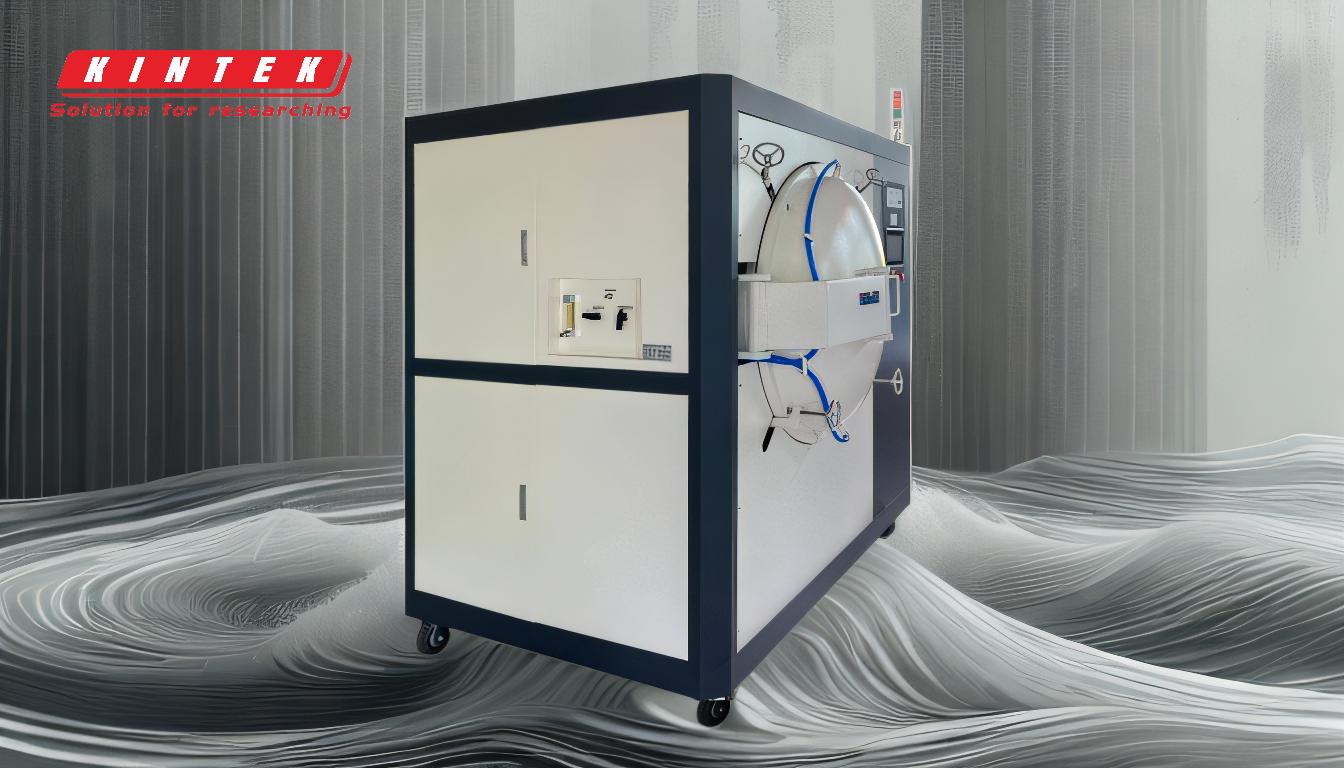
-
Definition and Basic Principles:
- Vacuum Thermal Evaporation: This is a method of vacuum deposition where a material is heated to high temperatures in a vacuum chamber until it vaporizes. The vapor then condenses onto a substrate, forming a thin film. This process is a type of Physical Vapor Deposition (PVD).
- Energy Requirement: For evaporation to occur, atoms or molecules of the material must gain enough energy to overcome the binding forces in their solid or liquid phase and transition into the gas phase.
-
Importance of Vacuum Environment:
- Contamination Reduction: A vacuum environment significantly reduces gaseous contaminants, ensuring that the evaporated atoms undergo essentially collisionless transport from the source to the substrate.
- Pressure Range: The gas pressure in the vacuum chamber typically ranges between 0.0013 Pa to 1.3 × 10−9 Pa, depending on the desired level of contamination control.
-
Applications:
- Electronic and Optical Devices: Vacuum thermal evaporation is commonly used in the production of electronic components such as electrical contacts, as well as optical devices like OLED displays and solar cells.
- Complex Applications: It can also be used for more complex applications, such as the co-deposition of several components by controlling the temperature of individual crucibles.
-
Process Details:
- Heating Mechanism: The material to be evaporated is heated using a resistance heater or an electron beam, depending on the specific requirements of the process.
- Deposition Control: The process allows for precise control over the thickness and uniformity of the deposited film, which is critical for the performance of the final product.
-
Advantages:
- High Purity Films: The vacuum environment ensures that the deposited films are of high purity, with minimal contamination.
- Versatility: This method can be used to deposit a wide range of materials, including metals, alloys, and compounds.
-
Challenges:
- Temperature Control: Precise temperature control is necessary to ensure consistent evaporation rates and film quality.
- Equipment Cost: The equipment required for vacuum thermal evaporation can be expensive, particularly for high-vacuum systems.
Understanding these key points is crucial for anyone involved in the procurement or use of vacuum thermal evaporation equipment and materials. This knowledge ensures that the right choices are made to achieve the desired outcomes in thin-film deposition processes. For more detailed information on related processes, you can explore vacuum heat treatment.
Summary Table:
Aspect | Details |
---|---|
Definition | A vacuum deposition method where materials are heated to vaporize and form thin films. |
Key Principle | Requires energy to transition atoms/molecules from solid/liquid to gas phase. |
Vacuum Environment | Reduces contamination; pressure ranges from 0.0013 Pa to 1.3 × 10−9 Pa. |
Applications | Used in solar cells, OLED displays, MEMS, and electrical contacts. |
Heating Mechanism | Resistance heaters or electron beams for precise temperature control. |
Advantages | High-purity films, versatile material deposition. |
Challenges | Requires precise temperature control; high equipment costs. |
Discover how vacuum thermal evaporation can elevate your thin-film processes—contact our experts today!