Induction heating is a process that primarily uses electrically conductive materials, typically metals, to generate heat through electromagnetic induction. The process involves creating an alternating magnetic field using an induction coil, which induces eddy currents in the conductive material. These eddy currents, flowing against the material's resistivity, generate heat through Joule heating. Induction heating is widely used in various industries, including metal melting, surface heating, welding, and even in household appliances like induction stoves. Non-conductive materials, such as plastics, can be heated indirectly by first heating a conductive metal inductor and transferring the heat.
Key Points Explained:
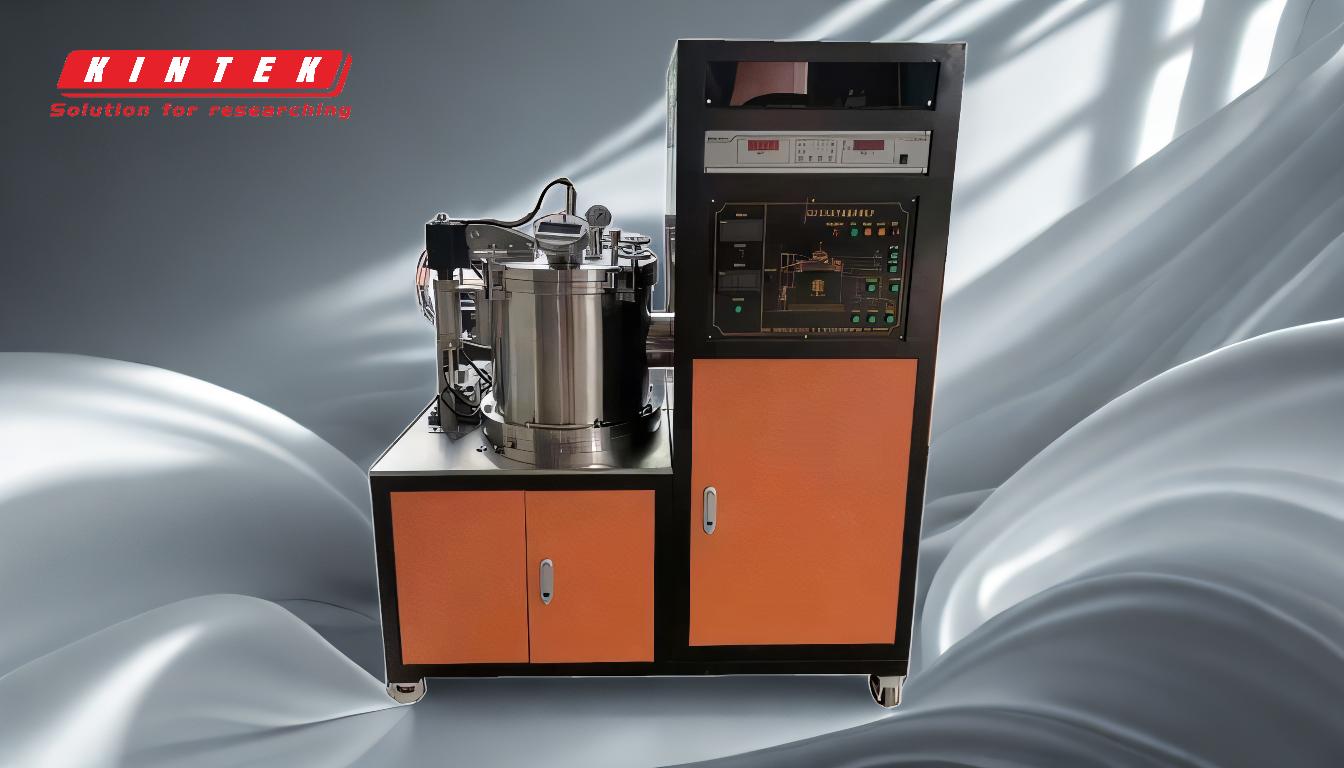
-
Primary Materials Used in Induction Heating
-
Conductive Metals: Induction heating is most effective with materials that are good conductors of electricity. Common metals used include:
- Ferrous Metals: Iron, steel, and their alloys are widely used due to their magnetic properties, which enhance the induction heating process.
- Non-Ferrous Metals: Metals like copper, aluminum, brass, and bronze are also commonly heated using induction. These metals are non-magnetic but are excellent conductors of electricity.
- Precious Metals: Gold, silver, platinum, and palladium, as well as their alloys, are often melted using induction heating due to their high conductivity and value.
- Indirect Heating of Non-Conductive Materials: Materials like plastics, which are non-conductive, can be heated indirectly. This is done by first heating a conductive metal inductor, which then transfers the heat to the non-conductive material.
-
Conductive Metals: Induction heating is most effective with materials that are good conductors of electricity. Common metals used include:
-
Mechanism of Induction Heating
- Electromagnetic Induction: The process begins with an alternating current flowing through an induction coil, creating a transient magnetic field. This magnetic field induces eddy currents in any nearby conductive material.
- Joule Heating: The eddy currents flow against the resistivity of the material, generating heat. This is known as Joule heating, and it is the primary mechanism by which induction heating works.
- Non-Contact Process: Induction heating is a non-contact process, meaning the heat is generated within the material itself without any physical contact with the heat source. This makes it highly efficient and precise.
-
Applications of Induction Heating
- Metal Melting: Induction heating is extensively used for melting metals, especially precious metals like gold and silver, as well as non-ferrous metals like copper and aluminum.
- Surface Heating and Hardening: It is used for surface heating and hardening of metals, which is crucial in manufacturing processes where only the surface of a metal part needs to be treated.
- Welding and Brazing: Induction heating is used in welding and brazing processes, where it provides localized heating, making it ideal for joining metals.
- Induction Stoves: In household appliances, induction stoves use this technology to heat cookware directly, offering a more energy-efficient cooking method.
- Plastic Molding: In the plastic industry, induction heating is used in injection molding machines to improve energy efficiency and reduce cycle times.
- Specialized Applications: Induction heating is also used in specialized applications such as tamper-resistant cap sealing in pharmaceuticals and heating silicon in the semiconductor industry.
-
Advantages of Induction Heating
- Efficiency: Induction heating is highly efficient because the heat is generated directly within the material, reducing energy loss.
- Precision: The process allows for precise control over the heating area, making it ideal for applications that require localized heating.
- Speed: Induction heating can achieve high temperatures very quickly, which is beneficial in industrial processes where time is a critical factor.
- Cleanliness: Since it is a non-contact process, there is no contamination from combustion by-products, making it a clean heating method.
-
Challenges and Considerations
- Material Limitations: Induction heating is limited to conductive materials. Non-conductive materials require indirect heating methods, which can be less efficient.
- Cost: The initial setup cost for induction heating equipment can be high, although this is often offset by the efficiency and precision it offers.
- Heat Distribution: Achieving uniform heat distribution can be challenging, especially in complex geometries. This requires careful design of the induction coil and control of the heating parameters.
In summary, induction heating is a versatile and efficient method for heating conductive materials, primarily metals. It relies on the principles of electromagnetic induction and Joule heating to generate heat within the material itself. While it has some limitations, particularly with non-conductive materials, its advantages in terms of efficiency, precision, and cleanliness make it a valuable technology in various industrial and household applications.
Summary Table:
Aspect | Details |
---|---|
Primary Materials | Ferrous metals (iron, steel), non-ferrous metals (copper, aluminum), precious metals (gold, silver) |
Mechanism | Electromagnetic induction and Joule heating |
Applications | Metal melting, surface hardening, welding, induction stoves, plastic molding |
Advantages | High efficiency, precision, speed, and cleanliness |
Challenges | Limited to conductive materials, high initial cost, heat distribution issues |
Unlock the potential of induction heating for your industry—contact us today to learn more!