Sintering is a versatile process used to transform powdered or porous materials into solid structures without melting. It is widely applied across various industries, including ceramics, metals, and advanced materials. Materials commonly sintered include metals like stainless steel, bronze, copper, and titanium alloys, as well as ceramics such as glass, aluminum oxide, and zirconium oxide. The process enhances material properties like strength, density, and durability, making it essential for applications in additive manufacturing, tooling, and high-performance components. Spark Plasma Sintering (SPS) further extends the range of sinterable materials by enabling the densification of challenging materials with minimal unwanted reactions.
Key Points Explained:
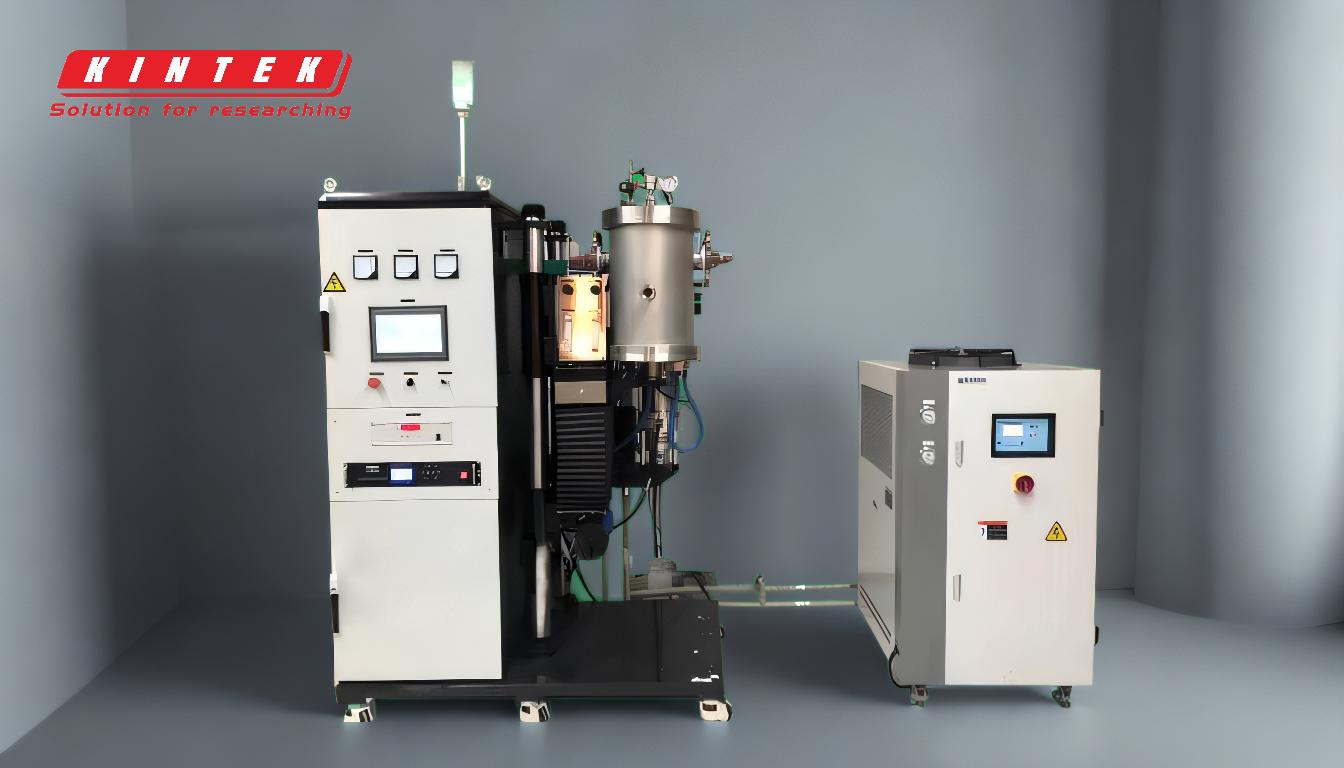
-
Definition of Sintering:
- Sintering is a thermal process that consolidates powdered or porous materials into solid structures without melting. It involves heating the material below its melting point, allowing particles to bond through diffusion.
-
Materials Commonly Sintered:
-
Metals:
- Stainless steels (e.g., 316L, 17-4PH), bronze, copper, nickel alloys (e.g., Inconel 718), and titanium alloys.
- Iron-based materials like iron-copper, iron-nickel, and carbon steels.
-
Ceramics:
- Glass, aluminum oxide (Al2O3), zirconium oxide (ZrO2), silicon dioxide (SiO2), magnesium oxide (MgO), and iron oxide (Fe2O3).
-
Advanced Materials:
- Pyrex and other specialized materials used in 3D printing and additive manufacturing.
-
Metals:
-
Applications of Sintering:
-
Additive Manufacturing:
- Sintering is crucial for 3D printing, enabling the production of complex parts from metal and ceramic powders.
-
Tooling and High-Performance Components:
- Used to create durable tools, bearings, and components for industries like aerospace and automotive.
-
Ceramic Production:
- Essential for manufacturing ceramic products with high strength and thermal stability.
-
Additive Manufacturing:
-
Spark Plasma Sintering (SPS):
- SPS is an advanced sintering technique that uses high heating rates and shorter holding times to densify materials, including those that are difficult to sinter using conventional methods.
- It prevents unwanted reactions and phase formations, making it ideal for highly reactive systems.
-
Benefits of Sintering:
-
Enhanced Material Properties:
- Improves density, strength, and durability of materials.
-
Versatility:
- Suitable for a wide range of materials, including metals, ceramics, and composites.
-
Cost-Effectiveness:
- Reduces material waste and enables the production of complex shapes with minimal machining.
-
Enhanced Material Properties:
-
Challenges and Considerations:
-
Material-Specific Requirements:
- Some materials, like certain ceramics, require pre-sintering treatments or organic additives.
-
Process Control:
- Precise temperature and time control are essential to achieve desired material properties.
-
Material-Specific Requirements:
By understanding the materials and processes involved in sintering, manufacturers can optimize their production techniques to create high-quality, durable components for various applications.
Summary Table:
Category | Materials |
---|---|
Metals | Stainless steels, bronze, copper, nickel alloys, titanium alloys, iron-based materials |
Ceramics | Glass, aluminum oxide (Al2O3), zirconium oxide (ZrO2), silicon dioxide (SiO2), magnesium oxide (MgO), iron oxide (Fe2O3) |
Advanced Materials | Pyrex, specialized materials for 3D printing and additive manufacturing |
Learn how sintering can optimize your production—contact our experts today!