Hydrogen embrittlement is a phenomenon where certain materials become brittle and fracture due to the presence and diffusion of hydrogen atoms. This issue is particularly critical in industries like aerospace, automotive, and oil and gas, where materials are exposed to hydrogen-rich environments. Understanding which materials are susceptible to hydrogen embrittlement is essential for selecting appropriate materials for high-stress applications. Materials such as high-strength steels, titanium alloys, and nickel-based alloys are particularly vulnerable. The susceptibility depends on factors like material composition, microstructure, and environmental conditions. This answer explores the materials most prone to hydrogen embrittlement, the mechanisms behind it, and mitigation strategies.
Key Points Explained:
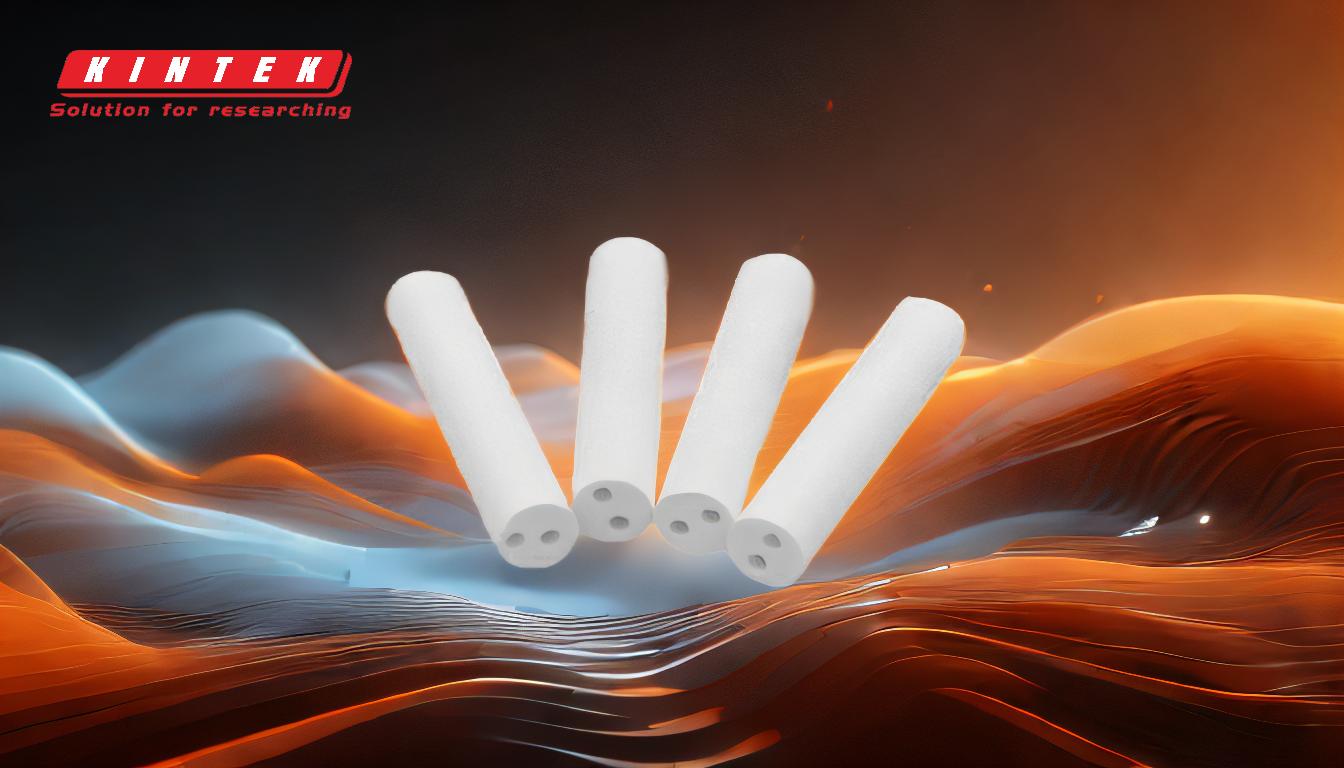
-
High-Strength Steels
- High-strength steels, especially those with tensile strengths above 1,000 MPa, are highly susceptible to hydrogen embrittlement.
- The susceptibility arises from their microstructure, which often contains martensite, a hard and brittle phase that provides high strength but is prone to hydrogen-induced cracking.
- Hydrogen atoms diffuse into the steel and accumulate at stress concentration points, such as grain boundaries or dislocations, leading to crack initiation and propagation.
- Applications: These steels are commonly used in automotive components, fasteners, and structural parts, making their susceptibility a critical concern.
-
Titanium Alloys
- Titanium alloys, particularly those used in aerospace and medical applications, are prone to hydrogen embrittlement, especially in environments with high hydrogen concentrations.
- The solubility of hydrogen in titanium is relatively high, and hydrogen can form hydrides, which are brittle phases that reduce ductility and toughness.
- Alloys like Ti-6Al-4V are particularly vulnerable, as the alpha phase in their microstructure is more susceptible to hydrogen-induced cracking.
- Applications: Titanium alloys are used in jet engines, airframes, and biomedical implants, where their failure could have catastrophic consequences.
-
Nickel-Based Alloys
- Nickel-based superalloys, such as Inconel and Hastelloy, are widely used in high-temperature and corrosive environments but are also susceptible to hydrogen embrittlement.
- The susceptibility is influenced by the alloy's composition and microstructure, with certain phases being more prone to hydrogen absorption.
- Hydrogen can reduce the ductility of these alloys, leading to premature failure under stress.
- Applications: These alloys are used in gas turbines, chemical processing equipment, and nuclear reactors, where hydrogen exposure is common.
-
Aluminum Alloys
- While aluminum alloys are generally less susceptible to hydrogen embrittlement compared to steels and titanium alloys, certain high-strength aluminum alloys can still be affected.
- Hydrogen can enter the material during manufacturing processes like casting or welding, leading to reduced ductility and fracture toughness.
- Applications: Aluminum alloys are used in aerospace and automotive industries, where their lightweight properties are critical.
-
Stainless Steels
- Austenitic stainless steels (e.g., 304 and 316) are generally resistant to hydrogen embrittlement due to their face-centered cubic (FCC) crystal structure, which limits hydrogen diffusion.
- However, martensitic and precipitation-hardened stainless steels are more susceptible due to their body-centered cubic (BCC) or body-centered tetragonal (BCT) structures, which allow easier hydrogen diffusion.
- Applications: Stainless steels are used in chemical processing, marine environments, and medical devices, where their corrosion resistance is essential.
-
Factors Influencing Susceptibility
- Material Composition: Alloying elements can either increase or decrease susceptibility. For example, chromium in stainless steels improves resistance, while carbon in steels can increase susceptibility.
- Microstructure: Materials with fine-grained structures or high dislocation densities are more prone to hydrogen embrittlement.
- Environmental Conditions: Exposure to hydrogen gas, acidic environments, or cathodic protection can increase hydrogen absorption.
- Stress Levels: Higher applied or residual stresses accelerate hydrogen-induced cracking.
-
Mitigation Strategies
- Material Selection: Choosing materials with lower susceptibility, such as austenitic stainless steels or low-strength alloys, can reduce the risk.
- Coatings and Surface Treatments: Applying coatings or surface treatments can act as barriers to hydrogen ingress.
- Heat Treatment: Post-weld heat treatment or annealing can reduce residual stresses and improve resistance.
- Environmental Control: Limiting exposure to hydrogen-rich environments or using inhibitors can mitigate hydrogen absorption.
By understanding the materials susceptible to hydrogen embrittlement and the factors influencing their behavior, engineers and purchasers can make informed decisions to ensure the reliability and safety of critical components.
Summary Table:
Material Type | Susceptibility Level | Key Characteristics | Common Applications |
---|---|---|---|
High-Strength Steels | High | Martensitic microstructure, prone to hydrogen-induced cracking | Automotive, fasteners, structural parts |
Titanium Alloys | High | Forms brittle hydrides, reduced ductility | Aerospace, medical implants |
Nickel-Based Alloys | Medium-High | High-temperature resistance, susceptible to hydrogen absorption | Gas turbines, nuclear reactors |
Aluminum Alloys | Low-Medium | Less susceptible, but high-strength variants can be affected | Aerospace, automotive |
Stainless Steels | Low (Austenitic) | FCC structure limits hydrogen diffusion; martensitic variants more susceptible | Chemical processing, marine environments |
Ensure your materials are safe from hydrogen embrittlement—contact our experts today for tailored solutions!