Electric arc furnaces (EAFs) are versatile and widely used in steelmaking, primarily for melting scrap steel. However, they can also utilize other materials like hot metal from blast furnaces or direct-reduced iron when economically viable. The furnace itself is constructed using refractory materials, such as high-purity alumina fiber insulation and Morgan materials brick, to withstand extreme temperatures. Heating elements, often made of graphite or molybdenum strips, play a critical role in generating the high temperatures required for melting. Additionally, the electrodes, typically made of graphite, are essential for conducting electricity into the furnace. This combination of materials ensures the efficiency, durability, and functionality of electric arc furnaces in industrial applications.
Key Points Explained:
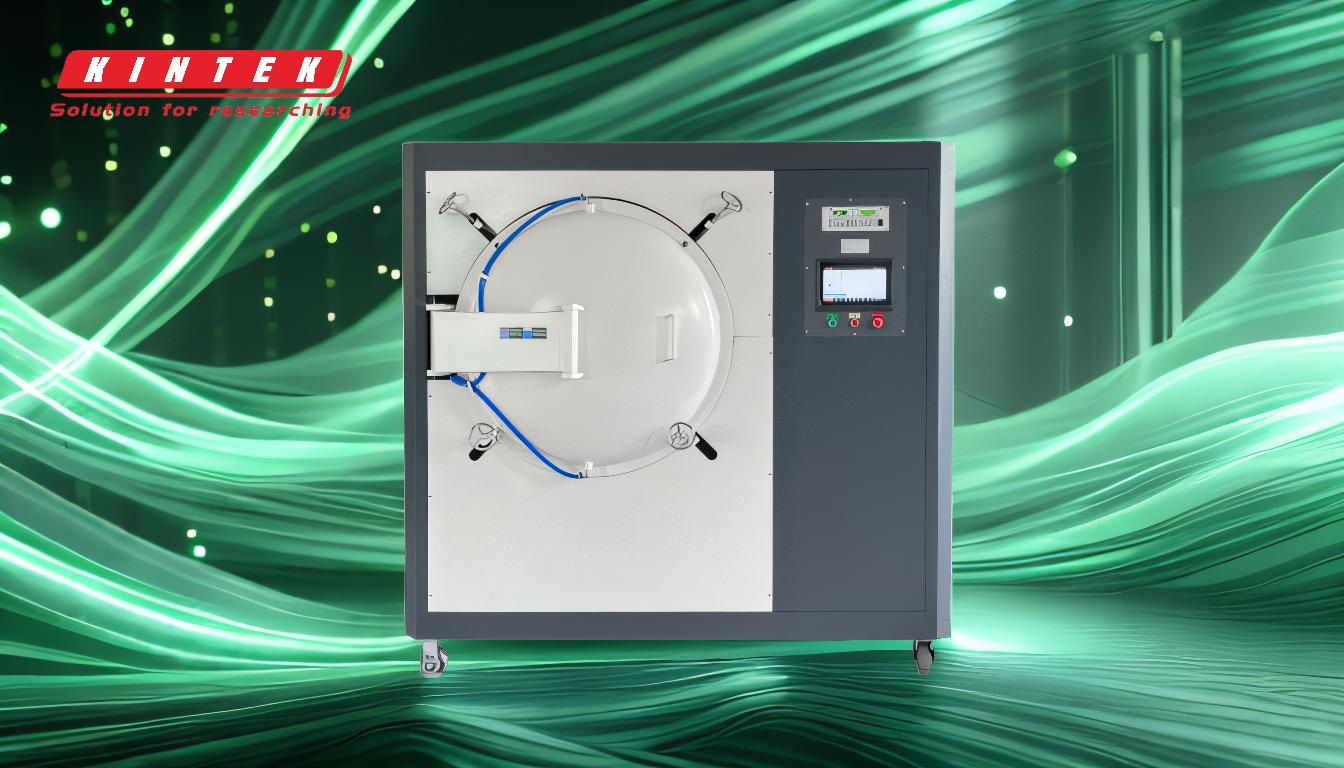
-
Primary Feedstock Materials:
- Scrap Steel: The most common and primary material used in electric arc furnaces. It is cost-effective and readily available, making it ideal for recycling and steel production.
- Hot Metal from Blast Furnaces: Occasionally used when available and economically feasible. It provides an alternative feedstock for EAFs.
- Direct-Reduced Iron (DRI): Another supplementary material used in EAFs, especially when high-quality steel is required. DRI is produced by reducing iron ore in a solid state, making it a cleaner alternative to traditional iron sources.
-
Refractory Materials for Furnace Construction:
- High-Purity Alumina Fiber Insulation: Used to line the furnace, providing excellent thermal insulation and resistance to extreme temperatures.
- Morgan Materials Brick: Known for its durability and efficiency, this material is used in high-temperature applications to ensure the furnace's structural integrity.
- Refractory Metals: Dense, hard, and highly resistant to heat and wear, these metals are essential for constructing parts of the furnace exposed to the highest temperatures.
-
Heating Elements:
- Graphite: Lightweight and curved graphite is commonly used for heating elements due to its ability to withstand high temperatures and excellent electrical conductivity.
- Molybdenum Strips: Available in pure or lanthanated forms, molybdenum strips are used for their high melting point and resistance to thermal stress.
- Iron-Chrome Aluminum or Nickel Chrome Alloys: These materials are shaped into cylindrical, semi-circular, or flat panels and are commonly used in industrial furnaces for their durability and heat resistance.
-
Electrodes:
- Graphite Electrodes: Essential for conducting electricity into the furnace, graphite electrodes are buried within the charge in submerged arc furnaces. They are chosen for their high conductivity and ability to withstand extreme heat.
-
Additional Considerations:
- High-Resistivity Ores: In submerged arc furnaces, ores with high resistivity are used as raw materials. This property ensures efficient heat generation during the melting process.
- Operational Efficiency: The combination of these materials ensures that electric arc furnaces operate efficiently, with minimal wear and tear, even under extreme conditions.
By understanding the materials used in electric arc furnaces, purchasers can make informed decisions about sourcing and maintaining these critical components, ensuring optimal performance and longevity of the furnace.
Summary Table:
Component | Materials Used | Purpose |
---|---|---|
Feedstock Materials | Scrap steel, hot metal from blast furnaces, direct-reduced iron (DRI) | Primary materials for melting and steel production |
Refractory Linings | High-purity alumina fiber insulation, Morgan materials brick, refractory metals | Withstand extreme temperatures and ensure structural integrity |
Heating Elements | Graphite, molybdenum strips, iron-chrome aluminum or nickel chrome alloys | Generate high temperatures required for melting |
Electrodes | Graphite electrodes | Conduct electricity into the furnace for efficient operation |
Additional Materials | High-resistivity ores | Ensure efficient heat generation in submerged arc furnaces |
Optimize your steelmaking process with the right materials—contact our experts today for tailored solutions!