Physical Vapor Deposition (PVD) is a versatile technique used to deposit a wide range of materials onto various substrates. The process involves converting the source material into vapor, which then condenses onto the target substrate to form a thin film. PVD is particularly effective for depositing metals, alloys, ceramics, and even some organic materials. The choice of material depends on the desired properties of the final coating, such as conductivity, hardness, or optical characteristics. Common materials used in PVD evaporation include metals like gold, titanium, and aluminum, as well as semiconductors and insulators like silicon dioxide and ITO. The process is carried out in a high-vacuum environment to ensure the purity and quality of the deposited film.
Key Points Explained:
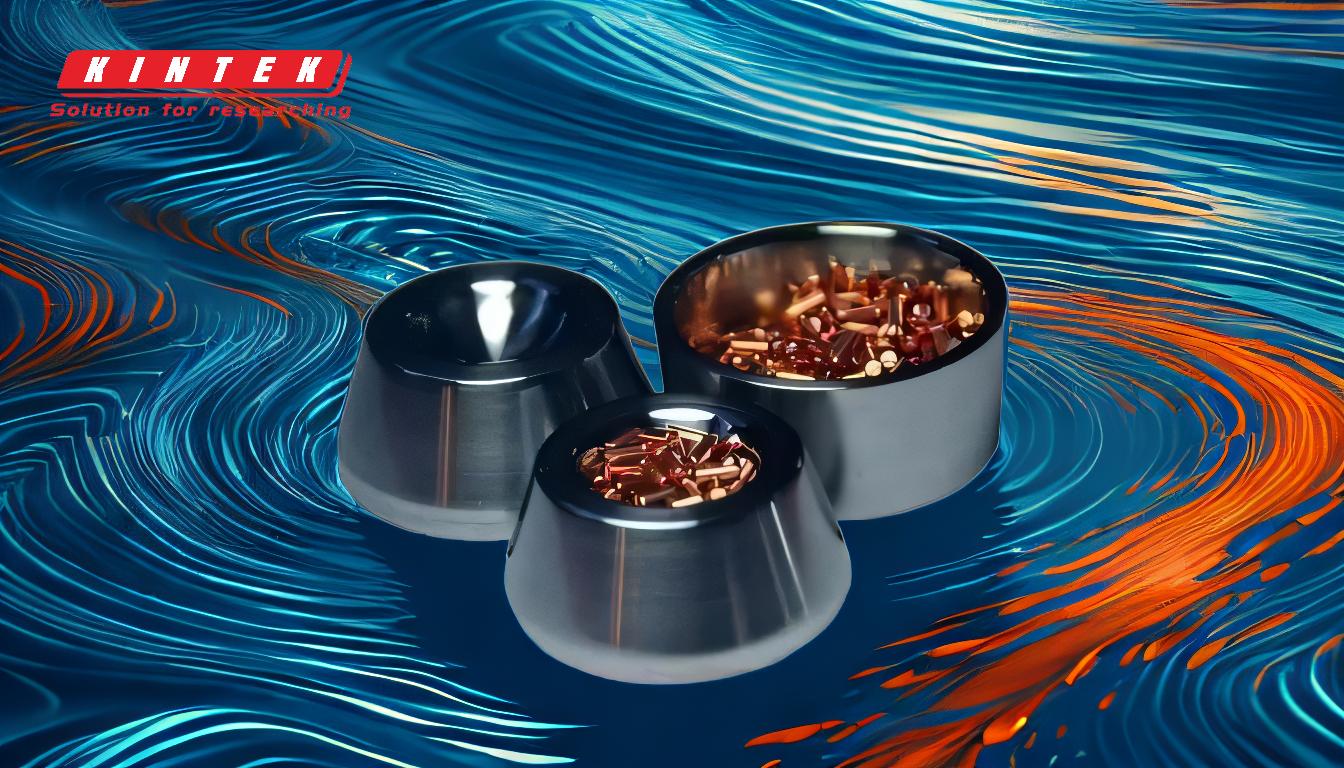
-
Types of Materials Deposited in PVD:
- Metals: Metals are the most commonly deposited materials in PVD. Examples include gold (Au), titanium (Ti), aluminum (Al), chromium (Cr), nickel (Ni), platinum (Pt), palladium (Pd), tantalum (Ta), and copper (Cu). These metals are chosen for their specific properties, such as conductivity, reflectivity, or corrosion resistance.
- Alloys: Alloys, which are mixtures of two or more metals, can also be deposited using PVD. For example, CuNi (copper-nickel) is a common alloy used in various applications due to its excellent electrical conductivity and corrosion resistance.
- Ceramics and Insulators: Ceramic materials like silicon dioxide (SiO2) and indium tin oxide (ITO) are often used in PVD. These materials are crucial for applications requiring electrical insulation or transparent conductive coatings.
- Semiconductors: Semiconductors such as silicon (Si) and germanium (Ge) can also be deposited using PVD. These materials are essential in the fabrication of electronic devices.
- Organic Materials: Although less common, some organic materials can be deposited using PVD. These are typically used in specialized applications where specific chemical or mechanical properties are required.
-
Process of PVD Evaporation:
- Heating the Source Material: In PVD evaporation, the source material is heated to a high temperature, causing it to vaporize. This can be achieved through various methods, such as resistive heating, electron beam heating, or laser ablation.
- High-Vacuum Environment: The evaporation process occurs in a high-vacuum environment to minimize collisions between the vaporized atoms and other gas molecules. This ensures that the vaporized material travels directly to the substrate without interference, resulting in a high-quality, uniform film.
- Deposition on Substrate: The vaporized material condenses onto the substrate, forming a thin film. The thickness of the film can range from a few nanometers to several hundred nanometers, depending on the application requirements.
-
Factors Influencing Material Choice:
- Adhesion: The ability of the deposited material to adhere to the substrate is crucial. Poor adhesion can lead to delamination or other defects in the film. Materials with good adhesion properties, such as titanium and chromium, are often used as adhesion layers.
- Stress and Thickness: The internal stress within the deposited film can affect its mechanical properties and longevity. Materials that can be deposited with low stress, such as gold and aluminum, are preferred for applications requiring thick films.
- Safety and Suitability: The safety of the material under vacuum conditions is another important consideration. Some materials may release harmful gases or particles when heated, making them unsuitable for PVD. Additionally, the material must be compatible with the substrate and the intended application.
-
Applications of PVD-Deposited Materials:
- Electronics: Metals like gold and copper are used in the fabrication of electronic components due to their excellent electrical conductivity. ITO is commonly used in transparent conductive coatings for displays and touchscreens.
- Optics: Materials like aluminum and titanium are used in optical coatings to enhance reflectivity or reduce glare. Silicon dioxide is used in anti-reflective coatings.
- Mechanical and Wear-Resistant Coatings: Hard materials like titanium nitride (TiN) and chromium nitride (CrN) are used in wear-resistant coatings for tools and machinery.
- Decorative Coatings: Gold and other precious metals are used in decorative coatings for jewelry and consumer goods.
-
Limitations and Considerations:
- Material Compatibility: Not all materials are suitable for PVD. Some materials may not vaporize effectively or may degrade under the high temperatures required for evaporation.
- Film Quality: The quality of the deposited film can be affected by factors such as the purity of the source material, the vacuum level, and the deposition rate. Careful control of these parameters is necessary to achieve a high-quality film.
- Cost: The cost of the source material and the complexity of the PVD process can be significant. This is particularly true for precious metals like gold and platinum, which are expensive and may require specialized equipment.
In summary, PVD evaporation is a highly versatile technique capable of depositing a wide range of materials, including metals, alloys, ceramics, semiconductors, and some organic materials. The choice of material depends on the desired properties of the final coating, such as conductivity, hardness, or optical characteristics. The process is carried out in a high-vacuum environment to ensure the purity and quality of the deposited film. Factors such as adhesion, stress, and material compatibility must be carefully considered to achieve the desired results. PVD is widely used in various industries, including electronics, optics, and mechanical engineering, due to its ability to produce high-quality, uniform coatings.
Summary Table:
Category | Examples | Applications |
---|---|---|
Metals | Gold (Au), Titanium (Ti), Aluminum (Al), Copper (Cu) | Electronics, decorative coatings, optical coatings |
Alloys | CuNi (Copper-Nickel) | Electrical conductivity, corrosion resistance |
Ceramics/Insulators | Silicon Dioxide (SiO2), Indium Tin Oxide (ITO) | Transparent conductive coatings, anti-reflective coatings |
Semiconductors | Silicon (Si), Germanium (Ge) | Electronic device fabrication |
Organic Materials | Specialized organic compounds | Niche applications requiring specific chemical/mechanical properties |
Interested in leveraging PVD for your next project? Contact us today to learn more!