The forging process involves shaping metal using localized compressive forces, and the materials used in this process are critical to achieving the desired properties in the final product. Commonly used materials include carbon steels, alloy steels, stainless steels, aluminum, titanium, and nickel-based alloys. Each material is selected based on its mechanical properties, such as strength, ductility, and resistance to wear and corrosion, as well as its ability to withstand high temperatures and pressures during forging. The choice of material depends on the intended application, whether it be for automotive, aerospace, industrial machinery, or other specialized fields. Understanding the properties and suitability of these materials is essential for optimizing the forging process and ensuring the quality and performance of the forged components.
Key Points Explained:
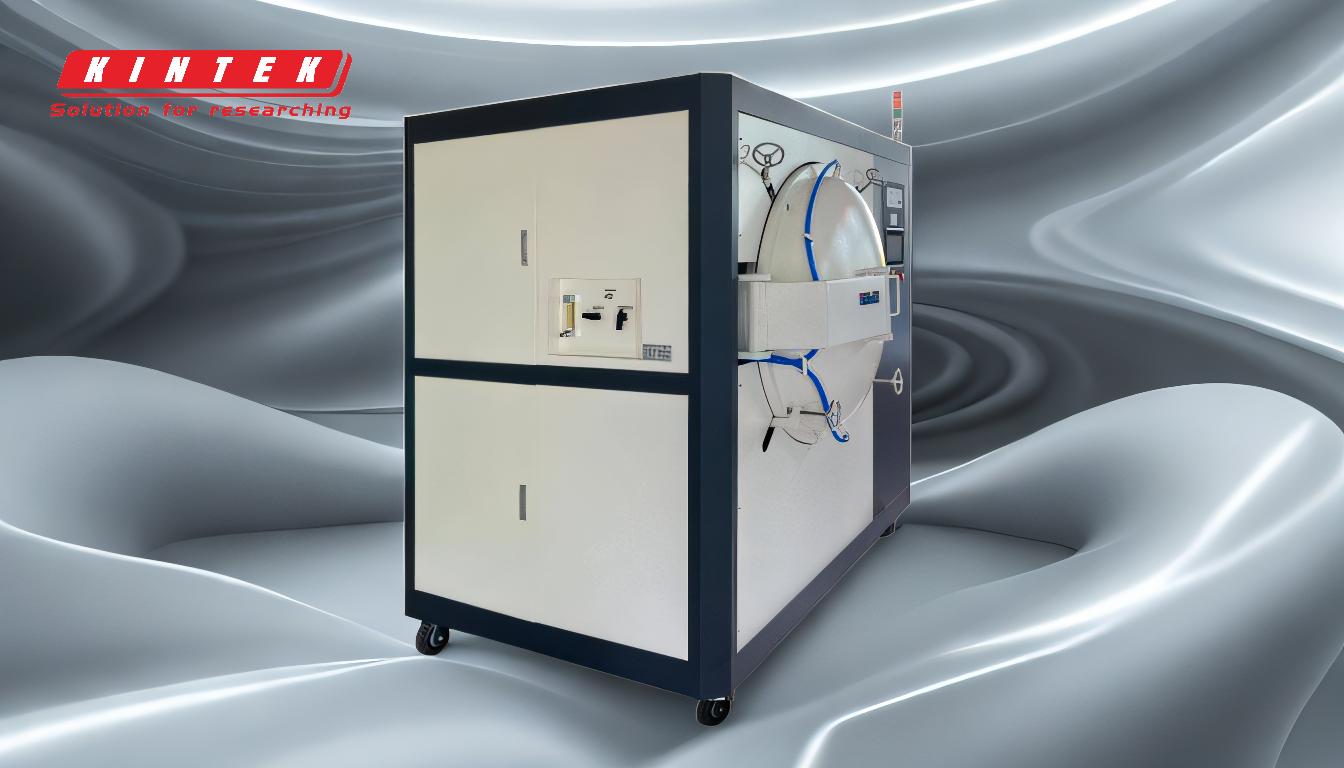
-
Carbon Steels:
- Carbon steels are widely used in forging due to their excellent strength, durability, and affordability.
- They contain varying amounts of carbon, which influences their hardness and tensile strength.
- Low-carbon steels are more ductile and easier to forge, while high-carbon steels offer greater strength and wear resistance.
- Applications include automotive parts, tools, and structural components.
-
Alloy Steels:
- Alloy steels are enhanced with additional elements like chromium, nickel, molybdenum, or vanadium to improve specific properties.
- These materials offer superior strength, toughness, and resistance to wear and corrosion compared to carbon steels.
- Commonly used in high-stress applications such as gears, shafts, and aerospace components.
-
Stainless Steels:
- Stainless steels are known for their exceptional resistance to corrosion and oxidation, making them ideal for harsh environments.
- They contain chromium, which forms a passive layer of chromium oxide to protect against rust.
- Commonly forged into components for the food industry, medical devices, and marine applications.
-
Aluminum:
- Aluminum is lightweight, corrosion-resistant, and has excellent thermal and electrical conductivity.
- It is often forged into parts for the aerospace and automotive industries, where weight reduction is critical.
- Aluminum alloys, such as 6061 and 7075, are commonly used due to their balance of strength and workability.
-
Titanium:
- Titanium is prized for its high strength-to-weight ratio, corrosion resistance, and ability to withstand extreme temperatures.
- It is commonly used in aerospace, medical implants, and chemical processing industries.
- Forging titanium requires specialized equipment and techniques due to its high melting point and reactivity.
-
Nickel-Based Alloys:
- Nickel-based alloys, such as Inconel and Hastelloy, are known for their exceptional resistance to heat, corrosion, and oxidation.
- These materials are used in high-temperature applications, such as jet engines, gas turbines, and nuclear reactors.
- Forging nickel-based alloys requires precise control of temperature and deformation to avoid cracking.
-
Material Selection Criteria:
- The choice of material depends on factors such as the intended application, mechanical properties, and environmental conditions.
- Forging processes must be tailored to the specific material to achieve the desired microstructure and mechanical properties.
- Proper heat treatment and post-forging processes are often required to enhance the material's performance.
-
Importance of Material Properties:
- The mechanical properties of the material, such as tensile strength, ductility, and hardness, directly influence the forging process and the final product.
- Understanding the material's behavior under high temperatures and pressures is crucial for optimizing the forging process.
- Material testing and quality control are essential to ensure the integrity and performance of forged components.
By carefully selecting and processing the appropriate materials, manufacturers can produce forged components that meet the demanding requirements of various industries. The choice of material not only affects the forging process but also determines the performance, durability, and cost-effectiveness of the final product.
Summary Table:
Material | Key Properties | Common Applications |
---|---|---|
Carbon Steels | Strength, durability, affordability | Automotive parts, tools, structures |
Alloy Steels | Enhanced strength, toughness, corrosion | Gears, shafts, aerospace components |
Stainless Steels | Corrosion resistance, oxidation | Food industry, medical devices |
Aluminum | Lightweight, corrosion-resistant | Aerospace, automotive parts |
Titanium | High strength-to-weight, heat resistance | Aerospace, medical implants |
Nickel Alloys | Heat, corrosion, oxidation resistance | Jet engines, gas turbines |
Need help selecting the right material for your forging project? Contact our experts today!