Physical Vapor Deposition (PVD) is a versatile coating technique used to deposit thin films of various materials onto substrates. The process involves vaporizing a solid material in a vacuum and then condensing it onto a substrate to form a thin film. PVD can deposit a wide range of materials, including metals, alloys, ceramics, and even some organic materials. The choice of material depends on the desired properties of the coating, such as hardness, corrosion resistance, electrical conductivity, or optical properties. Common materials used in PVD include titanium, zirconium, aluminum, stainless steel, copper, gold, and various nitrides, carbides, and oxides. Additionally, substrates must be vacuum-compatible, and pre-treatment is often required to ensure proper adhesion and film quality.
Key Points Explained:
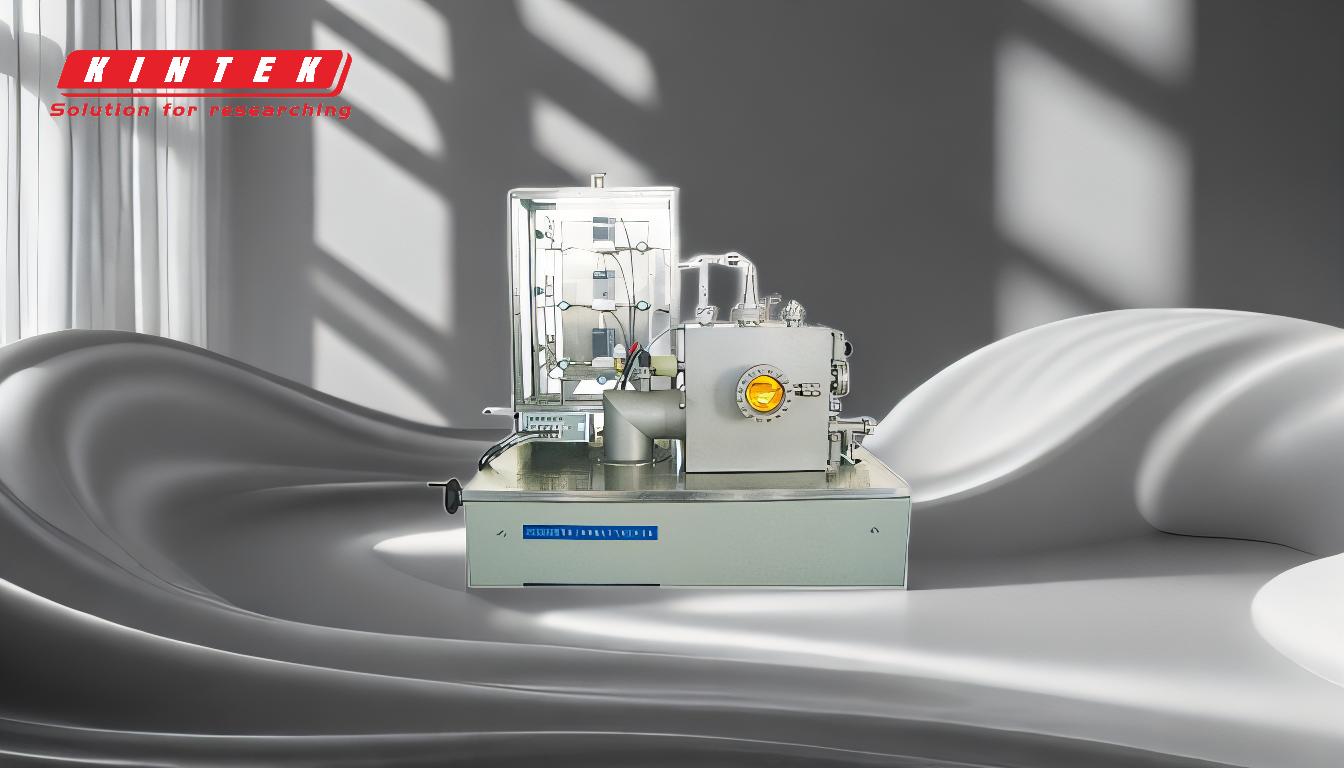
-
Types of Materials Used in PVD:
- Metals: PVD is commonly used to deposit metals such as titanium, zirconium, aluminum, stainless steel, copper, gold, chromium, nickel, tin, platinum, palladium, and tantalum. These metals are chosen for their specific properties, such as corrosion resistance, electrical conductivity, or aesthetic appeal.
- Alloys: PVD can also deposit alloys, which are combinations of metals designed to achieve specific properties. Examples include nickel-chrome and copper-nickel alloys.
- Ceramics: Ceramic materials, including nitrides (e.g., titanium nitride), carbides (e.g., silicon carbide), and oxides (e.g., silicon dioxide), are often deposited using PVD. These materials are valued for their hardness, wear resistance, and thermal stability.
- Semiconductors and Insulators: PVD can deposit semiconductor materials like silicon dioxide (SiO2) and indium tin oxide (ITO), which are used in electronic and optical applications. Insulators such as glass can also be coated using PVD.
- Organic Materials: While less common, some organic materials can be deposited using PVD, though this is typically more challenging due to their lower thermal stability.
-
Material Suitability for PVD:
- Vaporization Requirements: Materials used in PVD must be capable of being vaporized or bombarded to form a vapor. This typically involves heating the material to high temperatures or using techniques like sputtering.
- Vacuum Compatibility: The material must be stable under vacuum conditions. Some materials may decompose or react under vacuum, making them unsuitable for PVD.
- Adhesion and Film Quality: The quality of the deposited film, including its adhesion to the substrate, is critical. Poor adhesion or film quality can result in delamination or other defects.
-
Substrate Considerations:
- Vacuum Compatibility: Substrates must be vacuum-compatible or treated to become so. Common substrate materials include tool steels, glass, brass, zinc, and ABS plastic.
- Pre-Treatment: Substrates are often pre-treated to improve adhesion and film quality. This can include cleaning, organic coatings, or electroplating with materials like nickel and chromium.
-
Applications of PVD-Coated Materials:
- Aerospace and Electronics: Gold is often used in aerospace electronics for its excellent conductivity and corrosion resistance.
- Tooling and Cutting Tools: Titanium nitride and other hard coatings are used to extend the life of cutting tools and molds.
- Optical and Decorative Coatings: PVD is used to apply decorative and functional coatings on items like watches, jewelry, and automotive parts.
- Semiconductor Manufacturing: PVD is used to deposit thin films of materials like silicon dioxide and indium tin oxide in the production of semiconductors and displays.
-
Limitations and Challenges:
- Material Limitations: Not all materials are suitable for PVD. Some materials may not vaporize effectively or may degrade under the high temperatures or vacuum conditions required.
- Film Thickness: PVD typically deposits thin films, with thicknesses ranging from a few nanometers to several hundred nanometers. Achieving thicker coatings may require multiple deposition cycles.
- Cost and Complexity: PVD equipment and processes can be expensive and complex, particularly for large-scale or high-precision applications.
In summary, PVD is a highly versatile coating technique capable of depositing a wide range of materials, including metals, alloys, ceramics, and some organic materials. The choice of material depends on the desired properties of the coating and the specific application. Substrates must be vacuum-compatible and often require pre-treatment to ensure proper adhesion and film quality. While PVD offers numerous advantages, it also has limitations, including material suitability, film thickness, and cost.
Summary Table:
Category | Materials | Key Properties |
---|---|---|
Metals | Titanium, Zirconium, Aluminum, Stainless Steel, Copper, Gold, Chromium, etc. | Corrosion resistance, electrical conductivity, aesthetic appeal |
Alloys | Nickel-chrome, Copper-nickel | Tailored properties for specific applications |
Ceramics | Titanium nitride, Silicon carbide, Silicon dioxide | Hardness, wear resistance, thermal stability |
Semiconductors | Silicon dioxide (SiO2), Indium tin oxide (ITO) | Used in electronic and optical applications |
Organic Materials | Limited use due to thermal stability challenges | Specialized applications requiring organic coatings |
Ready to explore PVD coatings for your project? Contact our experts today to get started!