Induction hardening is a highly effective surface hardening process primarily used for steel and cast iron components. It involves localized heating of the metal surface using an alternating magnetic field generated by an inductor coil, followed by rapid cooling (quenching) to achieve surface hardening. This process enhances wear resistance, fatigue strength, and toughness in specific areas of the part while maintaining the core's ductility. Induction hardening is widely used in industries like automotive manufacturing for parts such as crankshafts, camshafts, and gears, where surface durability is critical. The process is versatile, allowing control over hardening depth and intensity by adjusting factors like frequency, power density, and heating time.
Key Points Explained:
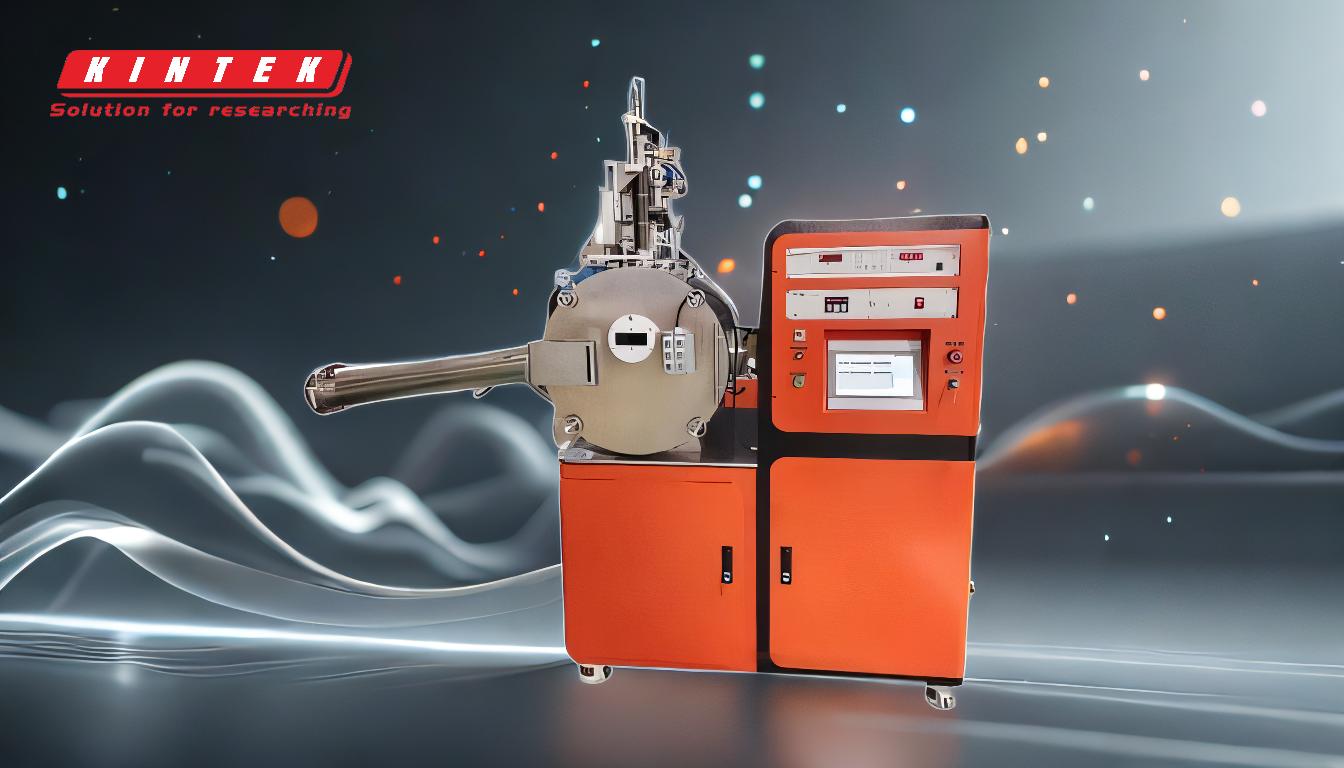
-
Metals Suitable for Induction Hardening:
- Steel: Induction hardening is most commonly applied to steel due to its ability to transform into martensite (a hard, wear-resistant phase) when heated and rapidly cooled. Examples include carbon steels, alloy steels, and tool steels.
- Cast Iron: Certain types of cast iron, such as ductile iron and gray iron, can also be induction hardened. The process improves their surface hardness and wear resistance, making them suitable for demanding applications.
- Limited Applicability to Other Metals: Induction hardening is not typically used for non-ferrous metals (e.g., aluminum, copper) because they lack the necessary phase transformation properties to achieve significant hardening.
-
How Induction Hardening Works:
- The workpiece is placed inside an inductor coil, which carries a high-frequency alternating current.
- The alternating current generates a magnetic field, inducing eddy currents within the workpiece.
- Due to the skin effect, the eddy currents concentrate on the surface, generating heat that raises the surface temperature above the material's critical transformation point.
- Rapid cooling (quenching) follows, transforming the heated surface layer into martensite, a hard and brittle phase.
-
Advantages of Induction Hardening:
- Localized Hardening: Only specific areas of the part are hardened, preserving the toughness of the core material.
- Controlled Depth: The hardening depth can be adjusted by varying the frequency of the alternating current (higher frequencies result in shallower hardening).
- Efficiency: The process is faster and more energy-efficient compared to traditional case-hardening methods.
- Improved Mechanical Properties: Enhanced wear resistance, fatigue strength, and surface hardness are achieved without compromising the part's overall integrity.
-
Applications in the Automotive Industry:
- Induction hardening is extensively used for automotive components like crankshafts, camshafts, gears, and axles.
- These parts operate under harsh conditions and require high wear resistance, bending resistance, and fatigue resistance.
- The process ensures that critical surfaces are hardened while maintaining the ductility of the core, which is essential for durability and performance.
-
Factors Influencing Induction Hardening:
- Material Composition: The carbon content and alloying elements in the metal determine its hardenability.
- Frequency: Higher frequencies (e.g., 100-500 kHz) are used for shallow hardening, while lower frequencies (e.g., 1-10 kHz) are suitable for deeper hardening.
- Power Density and Heating Time: These parameters control the intensity and duration of heating, affecting the hardness and depth of the hardened layer.
- Quenching Medium: The choice of quenching medium (e.g., water, oil, polymer) influences the cooling rate and final hardness.
-
Limitations of Induction Hardening:
- Shape Complexity: The process is best suited for parts with simple geometries. Complex shapes may result in uneven heating and hardening.
- Material Restrictions: Only ferrous metals (steel and cast iron) can be effectively induction hardened due to their phase transformation properties.
- Cost of Equipment: High-frequency induction hardening systems can be expensive, making the process less economical for small-scale applications.
-
Comparison with Other Hardening Methods:
- Case Hardening: Unlike case hardening, which involves diffusing carbon or nitrogen into the surface, induction hardening relies on localized heating and quenching.
- Flame Hardening: Induction hardening is more precise and controllable compared to flame hardening, which uses an open flame for heating.
- Laser Hardening: While laser hardening offers even greater precision, induction hardening is more cost-effective for larger parts and high-volume production.
In summary, induction hardening is a versatile and efficient process for enhancing the surface properties of steel and cast iron components. Its ability to provide localized hardening with controlled depth makes it ideal for applications in the automotive and machinery industries, where wear resistance and durability are critical. However, its suitability is limited to ferrous metals and parts with relatively simple geometries.
Summary Table:
Aspect | Details |
---|---|
Suitable Metals | Steel (carbon, alloy, tool), Cast Iron (ductile, gray) |
Process | Localized heating via alternating magnetic field, followed by rapid cooling |
Key Advantages | Controlled depth, energy efficiency, improved mechanical properties |
Applications | Automotive parts (crankshafts, gears, camshafts, axles) |
Factors Influencing | Material composition, frequency, power density, quenching medium |
Limitations | Limited to ferrous metals, complex shapes, high equipment cost |
Discover how induction hardening can optimize your component performance—contact us today for expert guidance!