Compression molding is a manufacturing process used to shape materials by applying heat and pressure. The plastics used in this process must have specific properties to withstand the conditions of compression molding, such as high temperature and pressure. Common plastics used include thermosetting polymers like phenolic resins, epoxy resins, and unsaturated polyesters, as well as thermoplastics like polyethylene and polypropylene. These materials are chosen for their ability to flow under heat and pressure, cure or solidify into a desired shape, and provide the necessary mechanical properties for the final product.
Key Points Explained:
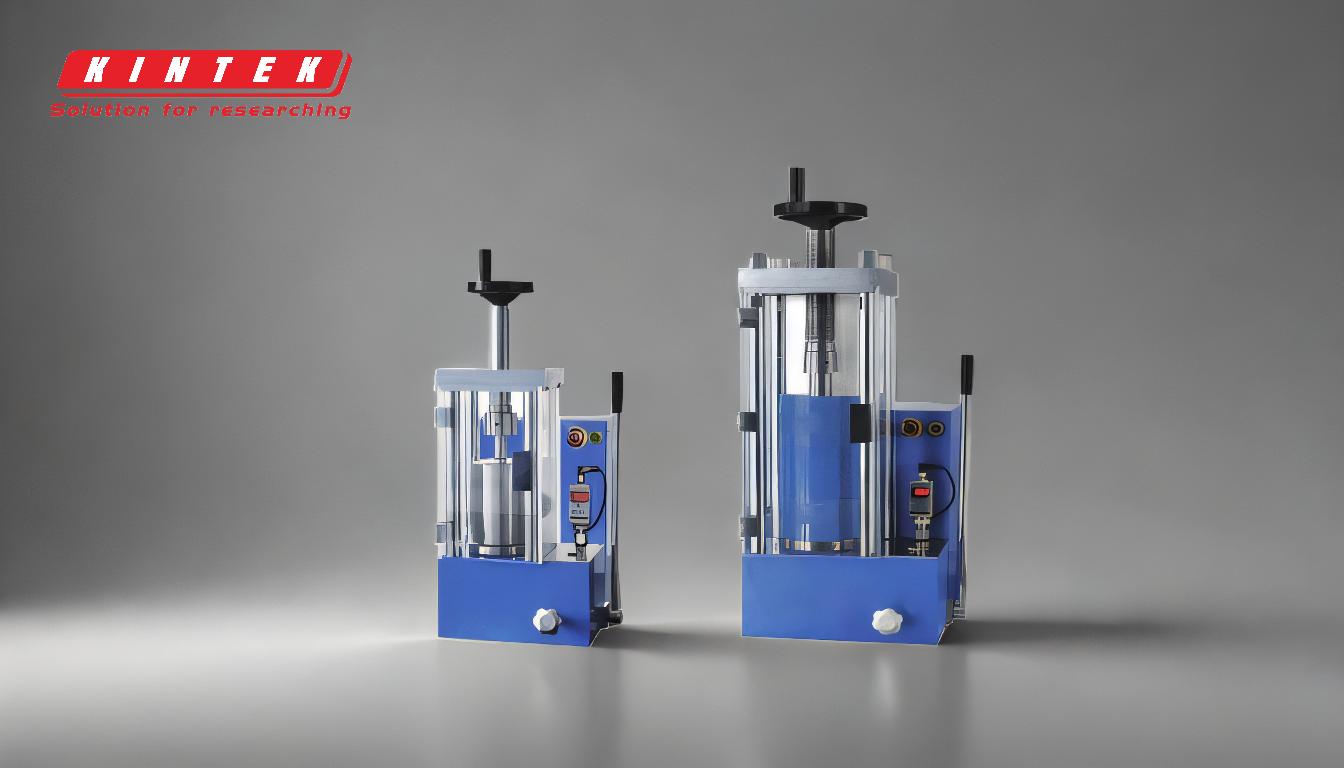
-
Thermosetting Polymers:
- Phenolic Resins: These are widely used in compression molding due to their excellent heat resistance, electrical insulation properties, and mechanical strength. They are commonly used in electrical components, automotive parts, and consumer goods.
- Epoxy Resins: Known for their strong adhesive properties and chemical resistance, epoxy resins are used in applications requiring high strength and durability, such as in aerospace and automotive industries.
- Unsaturated Polyesters: These resins are used for their good mechanical properties and ease of molding. They are often used in the production of fiberglass-reinforced plastics, such as in boat hulls and automotive body panels.
-
Thermoplastics:
- Polyethylene (PE): This plastic is used for its flexibility, impact resistance, and chemical resistance. It is commonly used in packaging, containers, and household goods.
- Polypropylene (PP): Known for its high melting point, chemical resistance, and fatigue resistance, polypropylene is used in a variety of applications, including automotive parts, medical devices, and consumer products.
-
Material Selection Criteria:
- Flow Properties: The material must be able to flow easily under heat and pressure to fill the mold cavity completely.
- Curing or Solidification: The material should cure or solidify properly to retain the desired shape and properties.
- Mechanical Properties: The final product must have the necessary strength, durability, and other mechanical properties required for its intended use.
-
Applications:
- Electrical Components: Phenolic resins are commonly used in the production of electrical insulators and connectors due to their excellent electrical insulation properties.
- Automotive Parts: Both thermosetting and thermoplastic materials are used in the production of various automotive components, such as dashboards, bumpers, and engine parts.
- Consumer Goods: Compression molding is used to produce a wide range of consumer goods, including kitchenware, toys, and household items.
By understanding the properties and applications of these plastics, manufacturers can select the appropriate material for their specific compression molding needs, ensuring the production of high-quality, durable products.
Summary Table:
Material Type | Examples | Key Properties | Common Applications |
---|---|---|---|
Thermosetting Polymers | Phenolic Resins | Heat resistance, electrical insulation, mechanical strength | Electrical components, automotive parts, consumer goods |
Epoxy Resins | Strong adhesive properties, chemical resistance, high strength | Aerospace, automotive industries | |
Unsaturated Polyesters | Good mechanical properties, ease of molding | Fiberglass-reinforced plastics (e.g., boat hulls, automotive body panels) | |
Thermoplastics | Polyethylene (PE) | Flexibility, impact resistance, chemical resistance | Packaging, containers, household goods |
Polypropylene (PP) | High melting point, chemical resistance, fatigue resistance | Automotive parts, medical devices, consumer products |
Need help selecting the right plastic for your compression molding project? Contact our experts today!