Heat treatment is a critical process in metallurgy and materials science, involving controlled heating and cooling of metals to alter their physical and mechanical properties. Proper precautions are essential to ensure safety, achieve desired material properties, and avoid equipment damage. Key considerations include understanding the material's properties, selecting appropriate heating and cooling rates, maintaining a controlled environment, and adhering to safety protocols. This process requires careful planning, monitoring, and execution to prevent defects such as warping, cracking, or uneven hardness. Below, we explore the key precautions to take during heat treatment.
Key Points Explained:
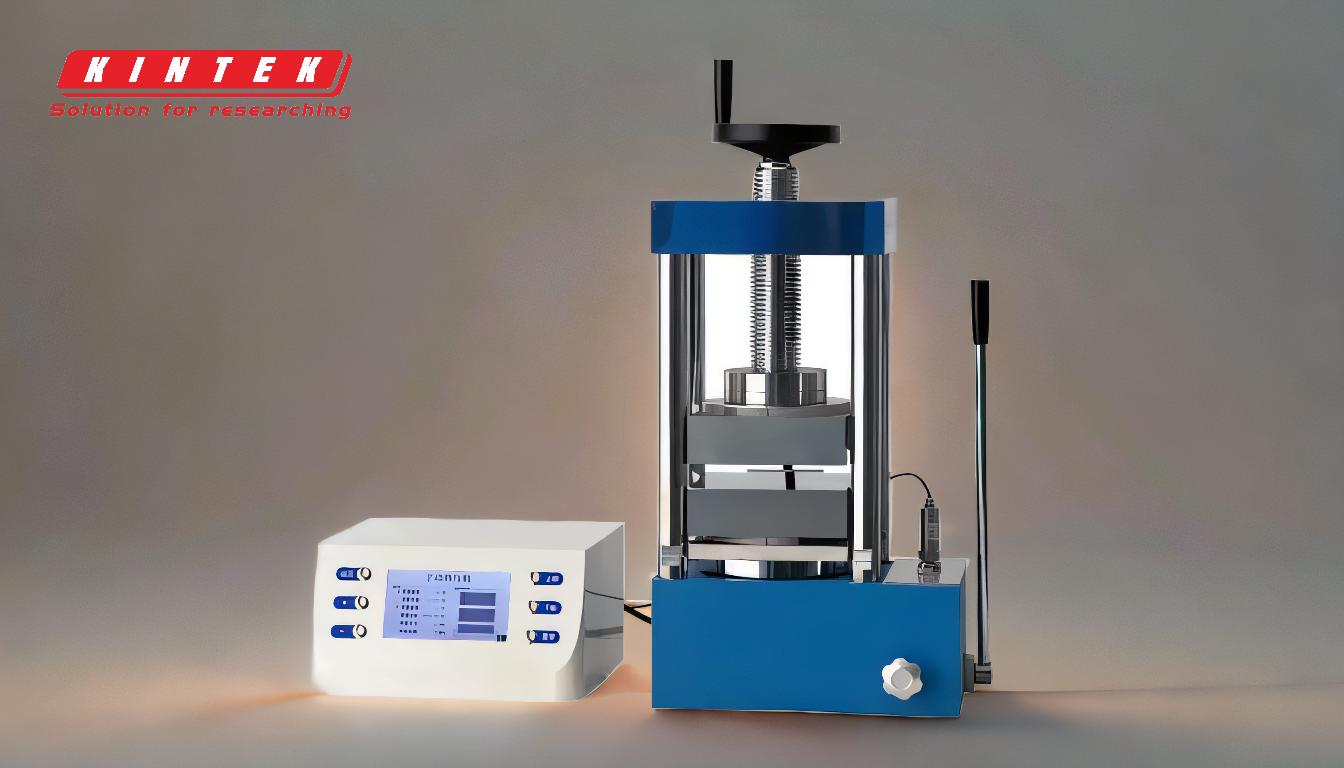
-
Understand Material Properties
- Different materials respond differently to heat treatment. For example, steel and aluminum require distinct temperature ranges and cooling rates.
- Conduct a thorough analysis of the material's composition, including alloying elements, to determine the appropriate heat treatment process.
- Refer to material datasheets or consult metallurgical experts to avoid overheating or underheating, which can lead to undesirable outcomes like brittleness or insufficient hardness.
-
Control Heating and Cooling Rates
- Rapid heating or cooling can cause thermal stress, leading to warping, cracking, or distortion.
- Use controlled furnaces or ovens to ensure uniform heating and avoid localized overheating.
- For cooling, select the appropriate medium (e.g., oil, water, or air) based on the material and desired properties. Quenching too quickly can cause cracking, while slow cooling may not achieve the required hardness.
-
Maintain a Controlled Environment
- Ensure the furnace or heat treatment equipment is clean and free from contaminants that could react with the material.
- Use protective atmospheres (e.g., inert gases like argon or nitrogen) to prevent oxidation or decarburization of the material surface.
- Monitor temperature and atmosphere composition throughout the process to maintain consistency.
-
Adhere to Safety Protocols
- Heat treatment involves high temperatures, posing risks such as burns, fires, or exposure to hazardous fumes.
- Wear appropriate personal protective equipment (PPE), including heat-resistant gloves, goggles, and aprons.
- Ensure proper ventilation in the workspace to dissipate heat and fumes.
- Regularly inspect and maintain equipment to prevent malfunctions or accidents.
-
Avoid Overheating or Underheating
- Overheating can cause grain growth, reducing the material's strength and toughness.
- Underheating may result in incomplete phase transformations, leading to inconsistent properties.
- Use calibrated thermocouples or pyrometers to accurately measure and control temperatures.
-
Prevent Warping and Distortion
- Uneven heating or cooling can cause warping, especially in thin or complex-shaped components.
- Use fixtures or supports to hold parts in place during heat treatment.
- Consider stress-relieving treatments before and after heat treatment to minimize residual stresses.
-
Monitor and Document the Process
- Keep detailed records of temperature, time, and cooling methods for each batch of materials.
- Use process control systems to ensure repeatability and consistency.
- Perform post-treatment inspections, such as hardness testing or microstructure analysis, to verify the desired properties have been achieved.
-
Handle Quenching Media Properly
- Quenching media must be selected based on the material and desired cooling rate.
- Ensure the quenching bath is at the correct temperature and free from contaminants.
- Dispose of used quenching media responsibly, as some oils or chemicals may be hazardous.
-
Consider Post-Treatment Processes
- After heat treatment, materials may require additional processes like tempering, annealing, or surface finishing to achieve the desired properties.
- Follow specific guidelines for each post-treatment step to avoid compromising the material's integrity.
-
Train Personnel Thoroughly
- Ensure all operators are trained in heat treatment principles, equipment operation, and safety procedures.
- Regularly update training programs to incorporate new techniques or safety standards.
By following these precautions, you can minimize risks, achieve consistent results, and extend the lifespan of both the materials and equipment involved in heat treatment. Proper planning, monitoring, and adherence to safety protocols are essential for successful heat treatment operations.
Summary Table:
Precaution | Key Considerations |
---|---|
Understand Material Properties | Analyze composition, alloying elements, and refer to datasheets or experts. |
Control Heating/Cooling Rates | Use controlled furnaces, avoid rapid heating/cooling, and select proper quenching media. |
Maintain Controlled Environment | Clean equipment, use protective atmospheres, and monitor temperature and atmosphere. |
Adhere to Safety Protocols | Wear PPE, ensure ventilation, and regularly inspect equipment. |
Avoid Overheating/Underheating | Use calibrated thermocouples to prevent grain growth or incomplete transformations. |
Prevent Warping/Distortion | Use fixtures, stress-relieving treatments, and ensure uniform heating/cooling. |
Monitor and Document Process | Record temperature, time, cooling methods, and perform post-treatment inspections. |
Handle Quenching Media Properly | Select appropriate media, maintain bath temperature, and dispose of media responsibly. |
Consider Post-Treatment Processes | Follow guidelines for tempering, annealing, or surface finishing. |
Train Personnel Thoroughly | Ensure operators are trained in principles, equipment operation, and safety protocols. |
Optimize your heat treatment process with expert guidance—contact us today!