Sintering is a versatile manufacturing process used across various industries to create durable, high-density materials by bonding particles together without melting them. This process is essential in producing metals, ceramics, plastics, and other materials, with applications ranging from industrial tools to dental restorations. Sintering involves three key stages: forming a powder blend with a bonding agent, removing the bonding agent through heating, and fusing the particles at high temperatures. The process is facilitated by specialized equipment like sintering furnaces, which are critical in achieving the desired material properties, such as density and mechanical strength. Industries such as aerospace, automotive, dental, and additive manufacturing rely on sintering for its cost-effectiveness, precision, and ability to produce complex shapes.
Key Points Explained:
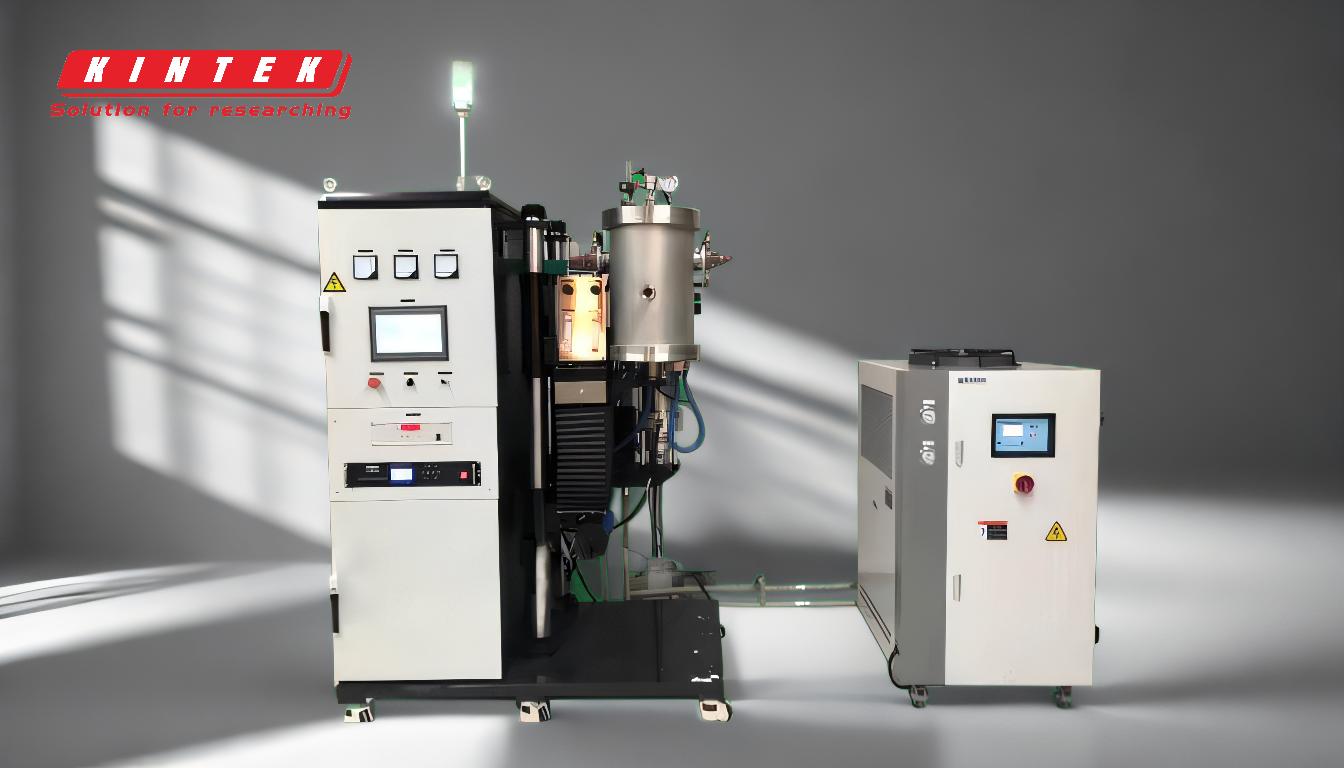
-
What is Sintering?
- Sintering is a manufacturing process that binds powdered materials into a solid mass using heat and pressure, without fully melting the material. This process is widely used in industries such as metalworking, ceramics, and plastics to create durable and high-density products.
-
Stages of the Sintering Process
-
Stage 1: Forming the Green Part
A powder blend, often combined with a bonding agent like water, wax, or polymer, is shaped into the desired form. This "green part" holds its shape but is not yet fully bonded. -
Stage 2: Debinding
The green part is heated to remove the bonding agent, which evaporates or burns away. This step prepares the material for the final bonding stage. -
Stage 3: Sintering
The temperature is increased to a point where the primary particles begin to fuse at their surfaces. This can involve melting an intermediate bonding agent (e.g., bronze) or surface melting of the primary particles, resulting in a dense, cohesive material.
-
Stage 1: Forming the Green Part
-
Applications of Sintering
-
Industrial Manufacturing
Sintering is used to produce stainless-steel tools, shotgun shells, aircraft hydraulic systems, and other high-performance components. -
Ceramics and Pottery
The process is essential for creating pottery, ceramics, and advanced materials like zirconia for dental restorations. -
Additive Manufacturing
In 3D printing, sintering furnaces are used to sinter and debind ceramic and metal parts, achieving densities of up to 99.5% and desired mechanical properties. -
Dental Industry
Dental sintering furnaces are used to process zirconia crowns, bridges, and frameworks, ensuring high hardness and reduced porosity.
-
Industrial Manufacturing
-
Role of Sintering Furnaces
- Sintering furnaces are specialized equipment designed to achieve the high temperatures required for the sintering process. They are used in industries with stringent manufacturing requirements, such as metal injection molding, carbide cutting tool production, and advanced ceramics manufacturing. These furnaces ensure precise temperature control and uniform heating, which are critical for achieving consistent material properties.
-
Advantages of Sintering
-
Cost-Effectiveness
Sintering is a low-energy process compared to melting, making it economical for large-scale production. -
Versatility
It can be used with a wide range of materials, including metals, ceramics, and plastics. -
Complex Shapes
The process allows for the creation of intricate shapes and designs that would be difficult to achieve with traditional manufacturing methods. -
Improved Material Properties
Sintering enhances density, strength, and wear resistance, making it ideal for high-performance applications.
-
Cost-Effectiveness
-
Industries Relying on Sintering
-
Aerospace and Automotive
Sintering is used to produce components like gears, bearings, and rotors that require high strength and durability. -
Medical and Dental
The process is critical for manufacturing biocompatible materials such as zirconia for dental restorations. -
Additive Manufacturing
Sintering furnaces are integral to 3D printing processes, enabling the production of complex parts with precise mechanical properties.
-
Aerospace and Automotive
-
Examples of Sintering in Action
-
Steel Production
In steel manufacturing, powdered iron ore mixed with coke is sintered to form lumps suitable for use in blast furnaces. -
Diamond Tools
Sintering furnaces are used to produce diamond saw blades and other cutting tools. -
Advanced Ceramics
The process is used to create high-performance ceramics for applications in electronics, energy, and aerospace.
-
Steel Production
By leveraging the sintering process and advanced equipment like sintering furnaces, industries can achieve high-quality, cost-effective production of materials and components with exceptional mechanical properties.
Summary Table:
Key Aspect | Details |
---|---|
Process | Bonds powdered materials using heat and pressure without melting. |
Stages | 1. Forming the green part 2. Debinding 3. Sintering |
Applications | Industrial tools, ceramics, dental restorations, 3D printing |
Advantages | Cost-effective, versatile, enables complex shapes, improves material properties |
Industries | Aerospace, automotive, medical, additive manufacturing |
Equipment | Sintering furnaces for precise temperature control and uniform heating |
Unlock the potential of sintering for your industry—contact our experts today!