Compression molding is a manufacturing process used to produce a wide range of products by compressing a material into a specific shape using heat and pressure. This method is particularly effective for materials that are difficult to shape using other techniques, such as thermosetting plastics, rubber, and composites. The process involves placing a pre-measured amount of material into a heated mold cavity, closing the mold, and applying pressure to form the material into the desired shape. Once the material has cured or cooled, the mold is opened, and the finished product is removed. Compression molding is favored for its ability to produce strong, durable, and high-quality products with complex geometries. It is widely used in industries such as automotive, aerospace, electronics, and consumer goods.
Key Points Explained:
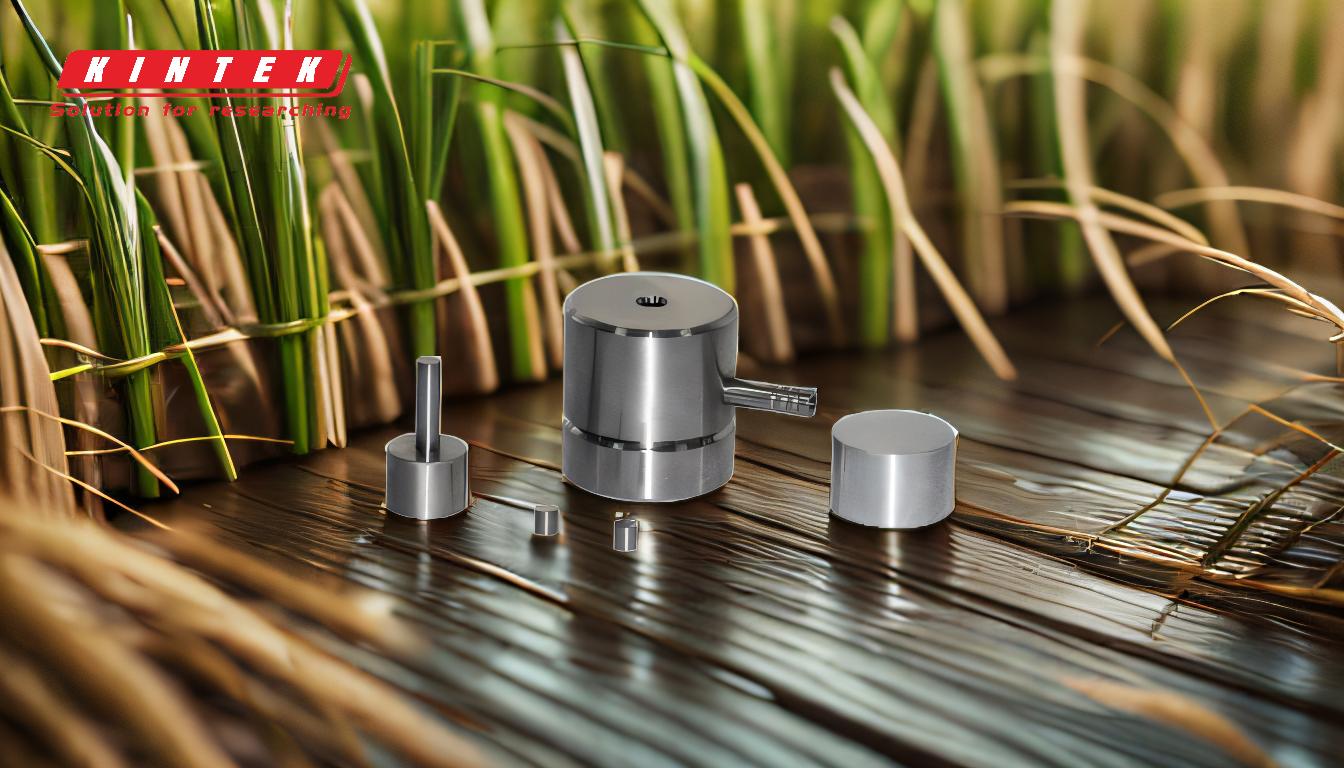
-
Automotive Industry:
- Compression molding is extensively used in the automotive industry to produce various components such as bumpers, dashboards, and interior trim. The process allows for the creation of parts that are both lightweight and strong, which is crucial for improving fuel efficiency and safety in vehicles.
- For example, rubber seals and gaskets, which are essential for preventing leaks and ensuring the proper functioning of various automotive systems, are often made using compression molding. This method ensures that the seals are durable and can withstand the harsh conditions encountered in automotive applications.
-
Aerospace Industry:
- In the aerospace sector, compression molding is used to manufacture components that require high strength-to-weight ratios and excellent thermal and chemical resistance. This includes parts like engine components, interior panels, and structural elements.
- The process is particularly suitable for producing composite materials, which are widely used in aerospace applications due to their superior properties. Compression molding allows for the precise control of material distribution and fiber orientation, resulting in parts that meet the stringent performance requirements of the aerospace industry.
-
Electronics Industry:
- Compression molding is also employed in the electronics industry to produce components such as insulators, connectors, and housings for electronic devices. These parts often need to be electrically insulating, thermally conductive, and resistant to environmental factors like moisture and chemicals.
- The ability to produce parts with complex shapes and fine details makes compression molding an ideal choice for electronic components. Additionally, the process can be used to embed electronic elements directly into the molded part, reducing the need for assembly and improving the overall reliability of the device.
-
Consumer Goods:
- A wide range of consumer products are made using compression molding, including kitchenware, toys, and household items. The process is particularly well-suited for producing items that require a combination of durability, aesthetic appeal, and functionality.
- For instance, compression molding is used to create durable and heat-resistant kitchen utensils, as well as toys that need to be safe, strong, and capable of withstanding rough handling. The process allows for the incorporation of various colors and finishes, making it possible to produce visually appealing products that meet consumer expectations.
-
Medical Industry:
- In the medical field, compression molding is used to produce a variety of devices and components, such as prosthetics, surgical instruments, and medical equipment housings. The process is valued for its ability to produce parts with high precision and consistency, which is critical in medical applications.
- Compression molding is also used to create biocompatible materials that can be safely used in contact with the human body. This includes materials like silicone rubber, which is often used in medical devices due to its flexibility, durability, and resistance to sterilization processes.
-
Industrial Applications:
- Compression molding is widely used in industrial applications to produce parts such as seals, gaskets, and bearings. These components are essential for the proper functioning of machinery and equipment, and they often need to withstand extreme conditions, including high temperatures, pressures, and exposure to chemicals.
- The process is particularly effective for producing parts with complex geometries and tight tolerances, ensuring that they fit and function correctly in their intended applications. Additionally, compression molding allows for the use of a wide range of materials, including high-performance polymers and composites, which can be tailored to meet specific industrial requirements.
In summary, compression molding is a versatile and widely used manufacturing process that is employed across various industries to produce a diverse range of products. Its ability to create strong, durable, and high-quality parts with complex geometries makes it an essential technique in modern manufacturing.
Summary Table:
Industry | Products |
---|---|
Automotive | Bumpers, dashboards, interior trim, rubber seals, gaskets |
Aerospace | Engine components, interior panels, structural elements, composite materials |
Electronics | Insulators, connectors, housings, embedded electronic components |
Consumer Goods | Kitchenware, toys, household items, durable utensils |
Medical | Prosthetics, surgical instruments, medical equipment housings |
Industrial | Seals, gaskets, bearings, high-performance polymer parts |
Interested in learning how compression molding can benefit your industry? Contact us today for expert guidance!